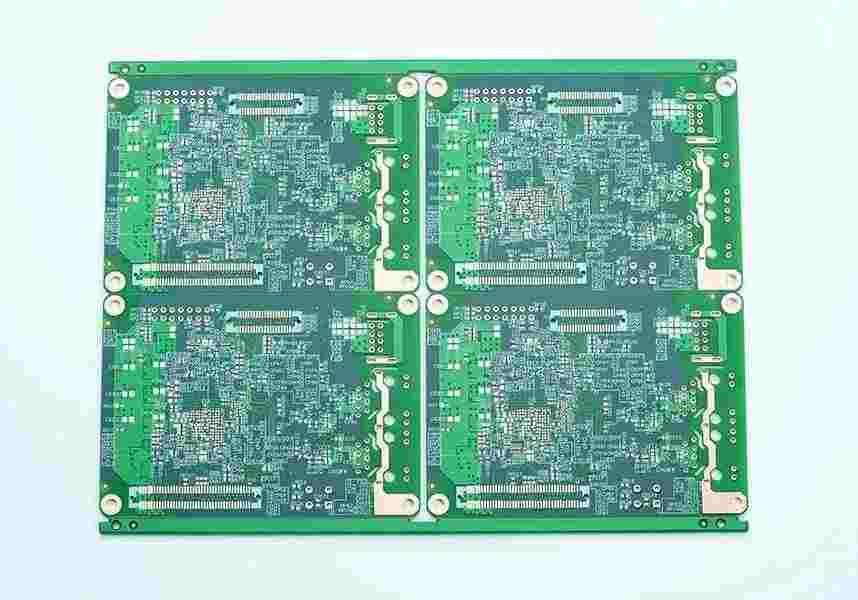
Best Practices for PCB Grounding Plane in Multilayer Stacking
When I first started to use modern CAD tools for PCB design, I took a fairly simple view of PCB grounding. As a physicist, I have been trained to think about things according to reference potential, image charge and many other terms in electromagnetic theory. Once the production of the first PCB is completed and abnormal noise and EMI are found in the design, the importance of clearly defining grounding will become more obvious.
Using a PCB ground plane in the stack is the first step to ensure power and signal integrity and maintain low EMI. However, some wrong statements about the grounding plane still seem to exist, and I have seen that experienced designers make some simple mistakes when defining grounding in PCB layout. If you are interested in preventing excessive radiation and ensuring signal integrity in the layout, follow these simple guidelines to achieve PCB ground plane on the next board.
Why use PCB grounding plate?
Before outlining how to use grounding and PCB grounding in your design, there are some important design goals to help you achieve grounding:
Clearly defined impedance: High speed/high frequency interconnects need to have a well-defined impedance so that the signal can be connected to other components with a specific system impedance (typically 50 ohms).
Return path: The PCB ground plane provides a clear return path for the current on the interconnection, which propagates in the grounding area in the form of displacement current. This makes the loop inductance smaller and ensures low EMI radiation, which is the main reason for using ground plane or grounded copper powder in the multilayer PCB stack.
EMI shielding and suppression: EMI is bidirectional, and the grounding copper in the design can shield external EMI sources.
Decoupling and stabilizing the power supply: This is probably the most unknown reason for using a ground plane in a multilayer PCB. A pair of large power planes and ground planes will act as a large decoupling capacitor, helping to keep the power supply on the circuit board stable.
In some cases, it may be difficult to meet the design goals listed above by casting copper in sections rather than in split planes. These wiring problems, as well as maintaining a well-defined ground plane, can create large loop inductances, which can lead to EMI.
Note that even if your ground plane is uniform, if the layout of the system is not compact, it will still form a long return path. There is no need to form zigzag routing on the whole board, and in this case, having a unified ground plane will not solve the EMI problem.
How to handle multiple ground references
Many times, there will be two different grounding grids in the schematic diagram, and then copy them to the PCB. As an example, this is common in electrically isolated power converters (e.g., resonant LLC converters) and many industrial Ethernet designs where the high/low voltage side or digital/analog side of the system has its own grounding area. The grounding area is then tied together with each other through a 0 ohm resistor or capacitor.
If your circuit board needs multiple grounding, your PCB layout and routing strategy now needs to consider where your real grounding reference is and how the return current propagates to the reference grid. This is related to points 1 and 2 in the above table. It is still common to see that experienced designers follow outdated design practices, which will cause EMI problems: dividing the ground plane into multiple copper casting areas. It is difficult to define a clear return path when PCB ground planes are separated by this method, which leads to large loop inductance, incorrect impedance and radiated EMI.
Reasons for division and what should not be done
Consider the example layout shown below. In this example, we have two grounding areas, which are physically isolated at the top level. There are sewing vias on layer 3 to bind the GND area back to the same polygon, and there are other low-speed signals on layer 2.
If we want to process slower signals, it may be very good in terms of EMI, because the parasitic loop inductance in this special arrangement is not very large. Since we are dealing with USB, it is best to use USB safely and place a uniform ground plane under these areas. In copper casting, the lack of ground plane below this gap will cause differential impedance discontinuity and lead to a long return path through the capacitor. This return path will have a higher loop inductance, resulting in greater EMI and crosstalk.
Personally, I will not worry about capacitors, nor will I completely separate the grounding area, unless there are some reasons for isolation in this type of system (for example, low voltage area and high voltage area, operator safety issues, some industry standards, etc.). Unless current isolation is required and a high-speed return path is not designed, only a uniform ground plane should be used. It can also be poured into the ground on the entire surface layer, and then tied back to the main PCB board ground plane. You will eliminate the radiated EMI problems you will see when wiring in gaps on the ground plane, and ensure a high degree of isolation between different signals on the surface layer.
In summary, when you need to provide a clear return path, use a PCB ground plane, and do not place gaps and gaps in the ground plane to create areas with different component blocks. Some techniques are needed to ensure that the return paths between different parts of the PCB do not overlap and generate crosstalk
If for some reason it is necessary to use a star grounding strategy in different grounded areas, under no circumstances should you start routing digital signals on ungrounded areas between different ground plane areas. This is the secret of high radiation EMI and EMC test failure. PCB assembly and PCB processing manufacturers explain the best practices of PCB grounding plane in multi-layer stacking.