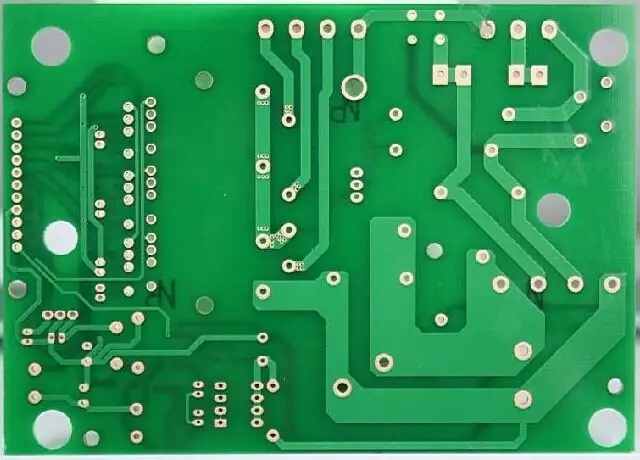
How to Design Mixed PCB Stack Sharing in PCB Design
The radar evaluation module is one of the best ways to design a PCB. The PCB contains a complete millimeter wave part, with RF routing and high power transmission, and a medium speed digital part with multiple ICs. I am not affiliated with TI, but the main reason why I like this board as an educational tool is that it shows a way to use PTFE based laminates such as Rogers or Taconic to build commercial RF products. Sometimes, when we talk about using PTFE laminates or alternatives such as low Dk glass cloth laminates, we are not talking about using expensive PTFE materials with adhesive layers or low loss materials such as Megtron to build the entire stack.
In some cases, it makes sense to build boards entirely from PTFE laminates or low Dk laminates. I have completed this work with a high-speed backplane, which supports dozens of long interconnects on multiple layers, and the bandwidth cut-off frequency is~80 GHz. When you need to route multiple gigabit serial channels between two connectors in 15 inch board space, you need to minimize the loss to ensure that the signal at the receiver can be recovered. However, in other cases, you actually only need a low loss laminate on one layer. This is the essence of mixed PCB stack, which may be a better choice for your PCB.
When to use mixed PCB stack
The first question that should arise when selecting materials and planning stacks is: What materials are needed and how many layers should be used? Assuming that you have determined the need for low loss laminates and the number of layers required, it is time to consider whether mixed laminations should be used. In a wide range of cases, you can consider using mixed layers with low loss laminates in PCBs:
Cost saving: removing all PTFE or all low DK can be expensive. For prototypes, the cost differences are not large, but they are accumulated in large batches.
Number of low RF interconnects: If you can place all high-speed/RF signals on one layer, it is meaningless to use a special low loss laminate to build the entire stack. You might consider increasing the board size to reduce the number of vias and place everything on the low loss layer.
Millimeter wave design: As long as the interconnection is short, some RF systems operating in ISM band or 6-7 GHz WiFi can operate normally on the FR4 laminate. Once the vehicle radar frequency is reached or higher, you usually need a low loss laminate, unless your interconnects are too short to be practical.
The above layers are also suitable for digital systems where the bandwidth is well extended to the millimeter wave range, but pay attention to the dispersion in the low loss laminate. RF board material manufacturers try to build their laminate systems with flat dispersion in the high GHz frequency range. However, above some high-frequency limits, dispersion will occur again, resulting in more loss and phase distortion in the digital signal. If you work at very high frequencies above the dispersion free limit, be sure to contact the laminate supplier to obtain dielectric constant data so that you can run accurate impedance and S parameter calculations.
In addition, some manufacturers may tell you that this stack cannot be made because you place PWR and SIG adjacent in two internal layers. If the board is small, it doesn't matter; The plate will not show any bending until its span reaches the multi U backplane size. If necessary, you can also use copper cladding to balance the inner layer.
Talk to your manufacturer early
If you have assembled a hybrid stack based on the loss requirements, board thickness, and number of layers, you should send the stack to the manufacturer before starting the design. This is important because your manufacturer can determine if the plate will go through the lamination cycle without decomposition or delamination because some materials require higher temperatures and pressures than others. Don't be afraid to contact the manufacturer as early as possible and ask for their advice on the use of the required low loss laminate in the composite laminate. Be sure to give them:
Number of layers required
Required layer thickness
Cap low loss laminated material
Packing laminated material
Try to determine which requirements are necessary and which can be owned, because you may need to compromise on some requirements.
After the adhesive layer is added, your manufacturer can give you an in-depth understanding of the thickness changes of the finished board. This must be taken into account when planning the stack. You usually do not need to worry about the dielectric constant of the adhesive layer, unless you need to wire it. If you have designed a low loss laminate on the top floor, the adhesive layer may need to be located between L2 and L3 in order for the low loss material to adhere to the FR4 grade laminate. Your manufacturer can provide you with more information on this.
Submit preliminary stack
Even after you create a preliminary stack, you should send it to your manufacturer so that they can check it before manufacturing. Sometimes, you cannot arbitrarily select any material system and low loss laminate to be used in the mixed laminate. Your manufacturer will have the right to decide which materials are available, which delivery times are short, or whether they must outsource manufacturing. If you can check the lamination before creating the rest of the design, your manufacturer can recommend alternative material systems that are compatible with the required PCB laminate process. They may also recommend alternative laminate thicknesses to help you meet the overall board thickness requirements.
Reading Material Data Sheet
If you are selecting materials for the mix stack and want to play a more active role in building the mix stack, check the data sheet for materials before creating the recommended stack. Try to match CTE value, Tg value, resin flow temperature and curing temperature to ensure full compatibility. You should still send the stack for review to ensure manufacturability. PCB assembly and PCBA manufacturer will introduce how to design mixed PCB stack for PCB design.