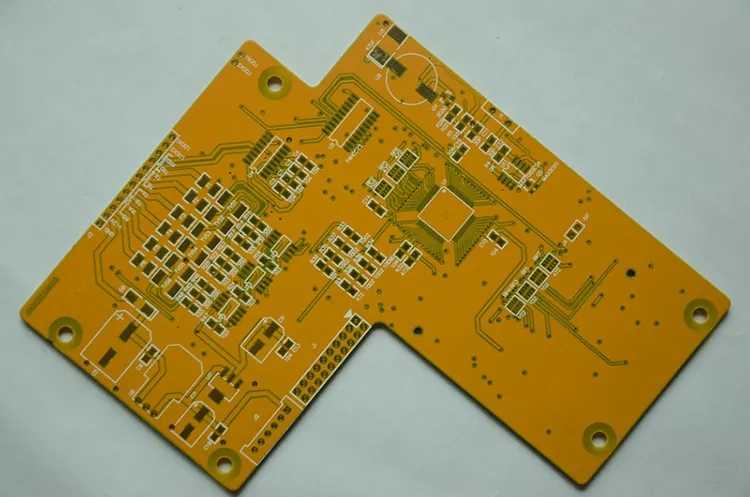
Rules for PCB manufacturers to share PCB power layout
PCB Layout Guide
Grounding
Unless space is limited, the circuit board design is allowed to include a solid power ground plane to provide electromagnetic shielding. If the whole layer cannot be put into use, at least consider the grounding polygon covering the whole area under the power supply component.
The ground plane of the power supply shall be separated from the common ground of the rest of the circuit to reduce noise coupling effect. In addition, the connection between these two grounds should be limited to a point on the board to prevent ground loops.
Micro conductivity
Make the wiring of power circuit as short and wide as possible to reduce resistance loss and electromagnetic noise radiation. If space permits, it is recommended to use polygon pouring. This is particularly important for linear power supplies where thermal conductivity is critical.
It is recommended that the circuit board design include a solid filled inner layer that uses through holes to connect power and ground planes for greater effect. The use of through holes to switch the power wiring from one layer to another should be avoided, as the through hole will act as a point of increasing impedance. Multiple through holes connecting polygons provide a better solution.
The performance will be affected by the thickness of the copper layer, although increasing the thickness will bring a price premium, so there may be a trade-off between cost and performance.
Another option to increase conductivity is to add a solder layer to the outer plate layer by changing the solder mask. However, you can achieve better performance by adding PCB bus bars or external wires between the points where power components are installed on the circuit board.
Component placement
As the shortest possible routing is required, the power supply components should be as close together as possible in a better direction to achieve a shorter routing length. This can include installing parts on both sides of the circuit board to achieve this.
Trace Route
Ideally, the wiring carrying sensitive signals should be kept away from the power supply on the unconnected board layer and separated from the power wiring through the ground plane. The signal wiring shall not be parallel to the power wiring carrying the power supply to prevent noise coupling from the power supply to the signal. If the approach is unavoidable, the signal wiring shall cross the power wiring at 90 degrees to minimize the noise coupling effect.
Thermal management
All power circuits generate heat, so the circuit board design needs to include thermal management. Therefore, the primary consideration of layout should be component placement, separating heating elements from thermal sensing elements as much as possible, while maintaining a short wiring length.
The next consideration is to use the copper of the circuit board to provide thermal conductivity, so as to distribute the heat more evenly in the area away from hot spots and allow heat dissipation.
A potential problem with switching mode power supplies is that feedback control circuits often contain temperature sensing elements that need to be co located with thermal switching elements. If not checked, hot spots can cause unstable power supplies and exacerbate cooling problems.
generalization
Power supply may be the source of most heat and noise problems in PCB, so PCB design must consider this from the beginning. A good board design starts with a good power layout.
It is unusual to design a PCB without power supply components, but just because it is a general-purpose component does not mean that it will not bring challenges to PCB design. There are two main variants to consider, linear power supply and switching mode power supply. These are challenges to PCB layout.
Linear power supply
Linear power supply circuit is simple in nature, and few components can be directly installed on PCB. The challenge is that these circuits are inefficient, which leads to the need to manage a large amount of power losses as radiant and conducted heat. When temperature sensing elements are mounted on a PCB or enclosed in an environmentally sealed enclosure for protection, this issue can be challenging, limiting cooling options.
Switching Mode Power Supply
The switching power supply circuit is more complex than the linear power supply, but it is more efficient. This is good because it reduces the engineering time for PCB designers to deal with thermal management, but unfortunately, it brings a series of different problems. The switching circuit may produce a lot of electromagnetic noise, and PCB designers need to manage it. This electrical noise will affect other circuit components on the PCB, and will be emitted outside the circuit board to affect nearby equipment. In extreme cases, the noise generated by the power circuit will be transmitted back through the main power line, thus affecting other equipment connected to the same main power supply.
Another potential noise problem is that switching mode circuits often generate ripple voltage at the output. If not properly managed, it may cause interference on the circuit board through capacitive or inductive coupling between parallel or bundled wire runs. A more subtle problem is that the grounding rebound may occur on the PCB where the switch circuit is installed. Fast switching causes a transient change in the ground potential at the point in the circuit board where the switch assembly is connected to the ground plane. This will cause a temporary potential difference on the circuit board ground plane. In extreme cases, this difference may cause components at a distance of the circuit board to observe and react to the sensing signal caused by this false potential difference.
Grounding
Unless space is limited, the circuit board design is allowed to include a solid power ground plane to provide electromagnetic shielding. If the whole layer cannot be put into use, at least consider the grounding polygon covering the whole area under the power supply component.
The ground plane of the power supply shall be separated from the common ground of the rest of the circuit to reduce noise coupling effect. In addition, the connection between these two grounds should be limited to a point on the board to prevent ground loops.
Micro conductivity
Make the wiring of power circuit as short and wide as possible to reduce resistance loss and electromagnetic noise radiation. If space permits, it is recommended to use polygon pouring. This is particularly important for linear power supplies where thermal conductivity is critical.
It is recommended that the circuit board design include a solid filled inner layer that uses through holes to connect power and ground planes for greater effect. The use of through holes to switch the power wiring from one layer to another should be avoided, as the through hole will act as a point of increasing impedance. Multiple through holes connecting polygons provide a better solution.
The performance will be affected by the thickness of the copper layer, although increasing the thickness will bring a price premium, so there may be a trade-off between cost and performance.
Another option to increase conductivity is to add a solder layer to the outer plate layer by changing the solder mask. However, you can achieve better performance by adding PCB bus bars or external wires between the points where power components are installed on the circuit board.
Component placement
As the shortest possible routing is required, the power supply components should be as close together as possible in a better direction to achieve a shorter routing length. This can include installing parts on both sides of the circuit board to achieve this.
Trace Route
Ideally, the wiring carrying sensitive signals should be kept away from the power supply on the unconnected board layer and separated from the power wiring through the ground plane. The signal wiring shall not be parallel to the power wiring carrying the power supply to prevent noise coupling from the power supply to the signal. If the approach is unavoidable, the signal wiring shall cross the power wiring at 90 degrees to minimize the noise coupling effect.
Thermal management
All power circuits generate heat, so the circuit board design needs to include thermal management. Therefore, the primary consideration of layout should be component placement, separating heating elements from thermal sensing elements as much as possible, while maintaining a short wiring length.
The next consideration is to use the copper of the circuit board to provide thermal conductivity, so as to distribute the heat more evenly in the area away from hot spots and allow heat dissipation.
A potential problem with switching mode power supplies is that feedback control circuits often contain temperature sensing elements that need to be co located with thermal switching elements. If not checked, hot spots can cause unstable power supplies and exacerbate cooling problems.
generalization
Power supply may be the source of most heat and noise problems in PCB, so PCB design must consider this from the beginning. A good board design starts with a good power layout. PCB design and PCB manufacturer introduce grounding, micro conductivity, component placement, etc. of PCB power supply layout.