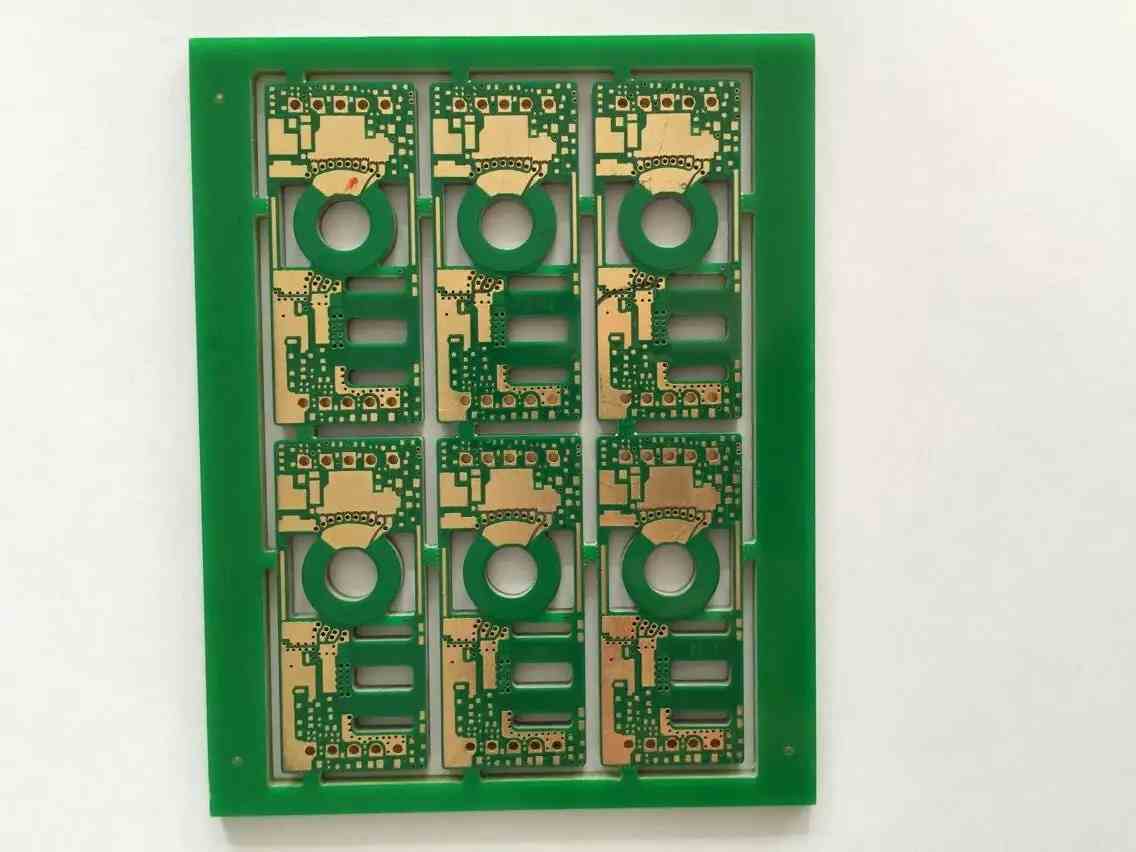
Electronic and Mechanical Design 3D Functions in PCB Space of PCB PCB Design
3D function in PCB space
Now many mechanical design tools have been able to support 3D models in PCBs created by third-party tools, but in addition to providing visualization of PCB board and housing assembly results, they cannot provide PCB designers with feedback on critical dimensions, gaps or other space compliance issues. In addition, mechanical design engineers are often unable to meet the positioning requirements of specific components, especially in the case of high-speed, mixed signal or high-voltage signal.
Altium Designer uses STEP format to overcome these limitations. It not only enables engineers to use the 3D model of the shell to present the final situation of the product, but also provides engineers with a 3D design method. Enough data is embedded in the AP214 file format, so engineers can really use the imported shell model to determine the size of PCB. It completely solves the problem of manually transferring key data from one field to another. By closely linking mechanical design with electronic design processes, electronic design engineers have taken a big step forward in designing for manufacturing.
In addition, the ability to define gaps in 3D format means that engineers in both mechanical and electronic fields can immediately see the impact of design changes. By combining the shell and PCB model in Altium Designer, engineers can generate 3D displays of products and measure the gap between them. This unprecedented capability means that electronic engineers can confidently hand over their designs to manufacturers.
To make this process more efficient, you can use the linked model method. In this way, changes made in one area can be reliably reflected in the other area. This means that the electronic engineer can see any changes to the housing, and similarly, any changes made to PCB or components will also be seen by the mechanical engineer.
The key to this function is not only to generate a single 3D model, but also to establish the coordinates of each model in 3D space based on the reference point. By accurately positioning the model of the housing and PCB components, the design engineer can verify the gap between them to ensure whether the PCB can be installed into the housing or whether the strong ribs and fixing devices are added, while maintaining the overall market target of the product.
Another advantage of working in a virtual world is that engineers can try all kinds of things at no cost. For example, when three reference points are used to align a component, it is likely that one component passes through another. Please think about the case where the circuit board passes through the housing during adjustment. This seems unconventional, but it provides clues to solve the bottleneck problems in the design. Using a real model to achieve this effect will be time-consuming and costly, but in the virtual field, it is as simple as changing a single reference point. Only with STEP format, close interaction between electronic field and mechanical field becomes possible. The inclusion of STEP format in PCB design environment indicates that we have made great achievements in creating a unified electronic product development method. Circuit board assembly, circuit board design, and circuit board processing manufacturers explain the 3D functions in the PCB space of electronic and mechanical design PCB circuit board design.