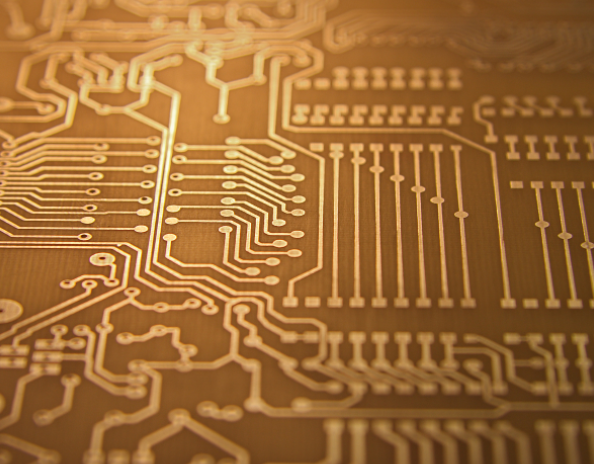
What problems should not be ignored in pcb design
With the development of PCB industry, better and better, more and more engineering and technical personnel join in PCB design and PCB manufacturing. But because PCB manufacturing involves a wider range of fields, and a consistent number of PCB design engineers (Layout personnel) Did not enable in or separated in the PCB manufacturing process, which leads to the importance of power efficiency and product functions in the design process, but downstream PCB processing plants receive orders, Because the design did not consider that this would bring difficulties to the product processing, there are many problems in the actual production process, such as the extension of the processing cycle or product hidden dangers
1. The cutting data mainly consider the plate thickness and copper thickness:
For plates thicker than 0.8MM, the standard series is 1.0 1.2 1.6 2.0 3.2 MM. If the thickness of the plate is less than 0.8MM, it is not considered as a standard series. The thickness can be determined as required, but the common thickness is 0.1 0.15 0.2 0.3 0.4 0.6MM. This data is mainly used for the inner layer of the multilayer plate.
When making the inner layer, the thickness after lamination can be adjusted through the thickness and structure of prepreg (PP). The selection range of core boards can be flexible. For example, the thickness of finished boards is 1.6 mm, and the selection of boards (core boards) can be 1.2 mm or 1.0 mm. As long as the thickness of laminates is controlled within a certain range, the thickness of finished boards can be met.
When designing the outer layer of PCB, pay attention to the thickness of the board Production and processing need to increase copper plating thickness, welding mask thickness, surface treatment (tin scattering, gold plating, etc.) thickness and the thickness of characters, carbon oil, etc The actual production thickness of metal plate will be greater than 0.05-0.1mm, and the thickness of tin plate will be 0.075-0.15mm For example, when the finished product requires a thickness of 2 For the design of 0 mm, when 2. usually select 0 mm plate for cutting, the thickness of the finished product will reach 2.1-2. Considering the plate tolerance and processing tolerance, it is 3 mm If the design must require that the finished product thickness is less than 2.0 mm, the plate shall be made of one. 9 mm non-traditional plate PCB processing plants need to temporarily order from sheet manufacturers, and the lead time will become very long
Circuit board
The other is PCB thickness tolerance. PCB designers shall consider product assembly tolerance and PCB thickness tolerance after PCB processing. There are three main aspects affecting the tolerance of finished products: plate tolerance, laminate tolerance and outer layer thickening tolerance. Now several conventional sheet tolerances are provided for reference: (0.8-1.0) ± 0.1 (1.2-1.6) ± 0.13 2.0 ± 0.18 3.0 ± 0.23 The lamination tolerance is controlled within ± 0.05-0.1 according to different layers and thickness MM. Especially for boards with board edge connectors (such as printed plugs), the thickness and tolerance of the board shall be determined according to the requirements of matching the connectors.
The thickness of copper is a problem on the PCB surface, because the hole copper needs to be finished by electroless copper plating and copper electroplating. If no special treatment is carried out, when the hole copper becomes thicker, the surface copper thickness will become thicker According to IPC-A-600G standard, the minimum copper plating thickness of Class 1 is 20um, and that of Class 3 is 2 and 25um Therefore, in circuit board production, if the copper thickness requires 1OZ (minimum 30.9 μ m) copper thickness, the cutting may times select HOZ (minimum 15.4 μ m) cutting according to the line width/line spacing, the allowable tolerance of 2-3um is deleted, and the minimum is 33.4um If 1OZ cutting is selected, the minimum thickness of finished copper will reach 47.9um Other copper thickness calculations can be inferred by analogy
2. PCB board drilling mainly considers hole size tolerance, pre amplification of drilling, processing from hole to board edge, and design of nonmetallic hole and locating hole:
At present, the minimum machining bit used for mechanical drilling is 0.2mm. However, due to the copper thickness of the hole wall and the thickness of the protective layer, the design hole diameter needs to be expanded in the production process. The tin spraying plate needs to be added 0.15mm, and the gold plating plate needs to be added 0.1mm. The key question here is, if the diameter of the hole increases, does the distance between the hole and the circuit and the copper sheet meet the processing requirements? Is the original design of the circuit board sufficient? For example, during the design process, the diameter of the through hole is 0.2 mm. The diameter of the liner is 0.35mm. The theoretical calculation shows that 0.075mm on one side of the welding ring can be completely machined, but there is no welding ring after enlarging the drilling according to the tin plate. If the CAM engineer is unable to expand the pad due to the spacing problem, the circuit board cannot be processed and produced.
Aperture tolerance: At present, the tolerance of most domestic drilling rigs is ± 0.05mm. With the tolerance of coating thickness in the hole, the tolerance of metallized holes is controlled within ± 0.075mm, and the tolerance of nonmetallic holes is controlled within ± 0.05mm.
Another problem that is easily overlooked is the distance between the drilled hole and the copper or conductor inner layer of the multilayer plate. Since the drilling positioning tolerance is ± 0.075mm, the expansion and contraction tolerance of the pattern after inner lamination is ± 0.1mm during lamination. In the design, the distance between the hole edge and the line or copper sheet of 4-layer plate shall be more than 0.15 mm, and the isolation of 6-layer or 8-layer plate shall be more than 0.2 mm, so as to facilitate production.
There are three common methods for making nonmetallic holes: dry film sealing or rubber particle plugging, so that the copper plated in the hole is not protected by corrosion resistance, and the copper layer on the hole wall can be removed during the etching process. Pay attention to the dry film seal. The hole diameter shall not be greater than 6.0mm, and the rubber plug hole shall not be less than 11.5mm. The other is to use secondary drilling to make nonmetallic holes. No matter what method is used, the copper content of nonmetallic pores must be within 0.2mm.
The design of locating hole is often a problem that is easy to ignore. In the process of PCB processing, testing, forming punching or electric milling, holes larger than 1.5mm shall be used as the positioning holes of the board. In the design, it is necessary to distribute the holes on the three corners of the circuit board into three corners as much as possible.