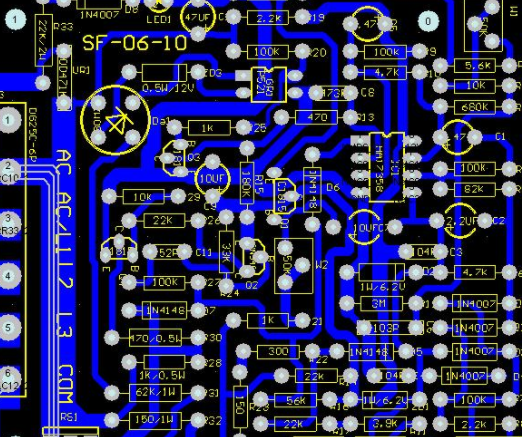
How much do you know about PCB proofing process
PCB proofing refers to the trial production of printed circuit boards before mass production The main application is that electronic engineers design circuits and complete the PCB process, and then go to the factory for small batch trial production, that is, PCB proofing The specific process PCB proofing details are as follows:
1. Contact the manufacturer
1 First, you need to inform the manufacturer of the dossier, process requirements and quantities.
Taking Shenzhen PCB Factory as an example, first enter kingford, then register the customer number (code "R"), and then a professional will quote you, place an order, and follow up the production progress.
2. Cutting
1 Purpose: According to the requirements of the engineering data MI, cut into small pieces and produce plates on the large plates that meet the requirements. Small plates meeting customer requirements.
Process: large plate - cutting plate according to MI requirements - ceria plate - beer tablet grinding - plate out
3. Drilling
1. Purpose: According to the engineering data, drill the required hole diameter at the corresponding position on the plate meeting the required size.
Process: folding pin - upper plate - drilling - lower plate - inspection maintenance
Fourth, copper deposition
1 Purpose: Copper dipping is to deposit a thin layer of copper on the wall of insulating hole by chemical method.
Process flow: rough grinding - hanging plate - automatic copper sinking wire - lower plate - dipping 1% dilute H2SO4 - coarse copper
5、 Graphic transmission
1 Purpose: Graphic transfer is to transfer the image on the production film to the circuit board
Circuit board
Process flow: (blue oil process): Grinding plate - first side of printing - drying - second side of printing - drying - explosion - development - inspection; (Dry film process): hemp board lamination vertical right bit exposure vertical development inspection
6、 Graphic electroplating
1 Purpose: Pattern electroplating refers to electroplating copper layer with required thickness and gold nickel or tin layer with required thickness on bare copper skin or hole wall of circuit pattern.
Process flow: upper plate - degreasing - secondary water washing - micro etching - water washing - acid washing - copper plating - water washing - acid washing - tin plating - water washing - lower plate
7、 Remove the film
1 Purpose: Remove the anti plating coating with NaOH solution to expose the non electroplating coating - circuit copper layer
Process: water film: rack inserting - alkali dipping - rinsing - scrubbing - machine passing; Dry film: release plate through machine
8、 Etching
1 Purpose: Etching is to use chemical reaction method to etch the copper layer of non circuit parts.
9、 Green oil
1 Purpose: Green oil is to transfer the pattern of green oil film to the circuit board to protect the circuit and prevent tin from welding parts on the circuit board
Process: Grinding plate printing, photosensitive green oil plate exposure; Grinding plate printing first side drying plate printing second side drying plate
10、 Character
1 Purpose: To provide characters as marks for easy recognition
Process: After finishing the green oil - cooling and standing - adjusting the screen printing characters - rear cubic
Eleven gold-plated fingers
1 Purpose: Plating a layer of nickel/gold on the finger of the plug according to the required thickness to make it harder and more wear-resistant
Process flow: upper plate - degreasing - twice cleaning - micro etching - twice cleaning - pickling - copper plating - cleaning - nickel plating - cleaning - gold plating
2 Tinplate (parallel process)
Purpose: Tin spraying is to spray a layer of lead tin on the exposed copper surface without covering the solder mask to protect the copper surface from corrosion and oxidation and ensure good welding efficiency.
Process flow: micro erosion - air drying - preheating - rosin coating - solder coating - hot air leveling - air cooling - cleaning and air drying
The above is the explanation given by the editor of pcb circuit board company.
If you want to know more about PCBA, you can go to our company's home page to learn about it.
In addition, our company also sells various circuit boards,
High frequency circuit board and SMT chip are waiting for your presence again.