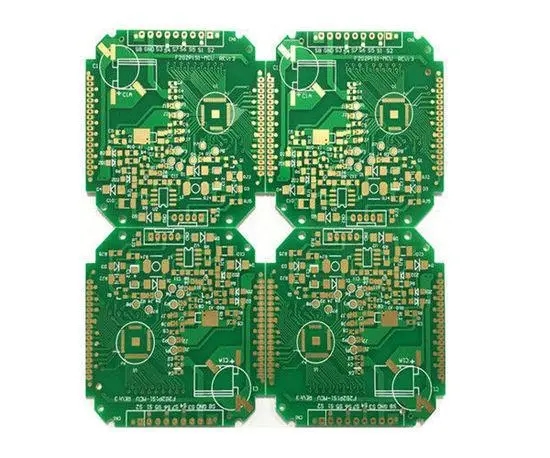
Precautions for drawing PCB by welding angle and welding defects of circuit board
Circuit board manufacturing, circuit board design, PCBA processing manufacturer will explain to you the welding angle drawing PCB precautions and circuit board welding defects
From the perspective of welding, what should be paid attention to when drawing PCB?
After analyzing the principle of the whole circuit, you can start to lay out and route the whole circuit. Now, let's introduce the ideas and principles of layout.
First of all, we will place the components with structural requirements. According to the imported structure, the connector should pay attention to the placement of one pin.
2. Pay attention to the height limit requirements in the structure during layout.
3. If the layout is to be beautiful, it is generally positioned according to the outer frame or centerline coordinates of the component (aligned in the center).
4. The overall layout shall consider heat dissipation.
5. In the layout, it is necessary to consider the routing channel evaluation and the space required for equal length.
6. The power flow direction shall be considered and the power channel shall be evaluated during the layout.
7. High speed, medium speed and low speed circuits shall be separated.
8. High current, high voltage and strong radiation components shall be far away from low current, low voltage and sensitive components.
9. Analog, digital, power supply and protection circuits shall be separated.
10. The interface protection devices shall be placed as close to the interface as possible.
11. Requirements for the placement order of interface protection devices: (1) The order of general power lightning protection devices is: varistors, fuses, suppression diodes, EMI filters, inductors or common mode inductors. If the schematic diagram is missing, any of the above devices shall be placed in sequence; (2) Generally, the sequence of protective devices for interface signals is: ESD (TVS tube), isolation transformer, common mode inductance, capacitance, resistance, and any device above shall be arranged in sequence if the schematic diagram is missing; The "line type" layout shall be carried out in strict accordance with the sequence of schematic diagrams (with the ability to judge whether the schematic diagrams are correct).
12. The level conversion chip (such as RS232) is placed close to the connector (such as serial port).
13. Devices susceptible to ESD interference, such as NMOS and CMOS devices, should be as far away from areas susceptible to ESD interference as possible (such as the edge area of a single board).
14. Clock device layout: (1) The crystal, crystal oscillator and clock distributor shall be as close as possible to the relevant IC devices; (2) The filter of the clock circuit ("Π" type filter shall be used as far as possible) shall be close to the power input pin of the clock circuit; (3) Whether the output of crystal oscillator and clock distributor is connected with a 22 ohm resistor in series; (4) Whether the unused output pins of the clock distributor are grounded through resistance; (5) The layout of crystal, crystal oscillator and clock distributor shall be far away from high-power components, radiator and other heating devices; (6) Whether the distance between crystal oscillator and board edge and interface device is greater than 1 inch.
15. Whether the switching power supply is far away from AD DA converter, analog devices, sensitive devices and clock devices.
16. The layout of switching power supply shall be compact, and the input/output shall be separated. The layout shall be strictly in accordance with the requirements of the schematic diagram, and the capacitors of switching power supply shall not be placed randomly.
17. Capacitor and filter device: (1) The capacitor must be placed close to the power supply pin, and the smaller the capacitance is, the closer the capacitor is to the power supply pin; (2) EMI filter shall be close to the input port of chip power supply; (3) In principle, one 0.1uf small capacitor for each power supply pin, one or more 10uf large capacitors for an integrated circuit can be increased or decreased according to the specific situation.
Detailed explanation of three major factors causing PCB welding defects
There are three reasons for the welding defects of circuit boards:
1. Solderability of PCB holes affects welding quality
Poor solderability of circuit board holes will lead to faulty soldering defects, which will affect the parameters of components in the circuit, lead to unstable conduction of components and inner wires of multilayer board, and cause the functional failure of the whole circuit. Solderability is the property that the metal surface is wetted by molten solder, that is, a relatively uniform, continuous and smooth adhesive film is formed on the metal surface where the solder is located.
The factors affecting the solderability of PCB mainly include: (1) the composition of solder and the properties of solder. Solder is an important part of welding chemical treatment process. It is composed of chemical materials containing flux. The commonly used low melting point eutectic metal is Sn Pb or Sn Pb Ag The impurity content shall be controlled in proportion to prevent the oxide produced by impurities from being dissolved by the flux. The function of the flux is to help the solder to wet the circuit surface of the soldered board by transferring heat and removing rust. White rosin and isopropanol solvent are generally used.
(2) The weldability is also affected by the welding temperature and the cleanliness of the metal plate surface. If the temperature is too high, the solder diffusion speed will be accelerated. At this time, the solder has high activity, which will cause rapid oxidation of the circuit board and solder melting surface, resulting in welding defects. If the circuit board surface is polluted, the solderability will also be affected, resulting in defects. These defects include solder beads, solder balls, open circuit, poor gloss, etc.
2. Welding defects caused by warping
The circuit board and components are warped during welding, and defects such as false soldering and short circuit are caused due to stress deformation. Warpage is often caused by the temperature imbalance between the upper and lower parts of the circuit board. For large PCBs, warping will also occur due to the weight of the board itself. Ordinary PBGA devices are about 0.5mm away from the printed circuit board. If the components on the circuit board are large, the solder joints will be under stress for a long time as the circuit board returns to its normal shape after cooling down. If the components are raised by 0.1mm, it will be enough to cause open circuit due to faulty soldering.
3. The design of circuit board affects the welding quality
In the layout, when the size of the circuit board is too large, although the welding is easier to control, the printing line is long, the impedance increases, the noise resistance decreases, and the cost increases; If it is too small, the heat dissipation will drop, the welding is not easy to control, and the adjacent lines will easily interfere with each other, such as the electromagnetic interference of the circuit board. Therefore, PCB design must be optimized:
(1) Shorten the connection between high-frequency components and reduce EMI interference.
(2) Components with large weight (such as more than 20g) shall be fixed with supports and then welded.
(3) Heat dissipation shall be considered for heating elements to prevent large Δ In case of defects and rework, the thermal sensor shall be far away from the heat source.
(4) The arrangement of elements shall be as parallel as possible, which is not only beautiful but also easy to weld, and it is suitable for mass production. It is better to design the circuit board as a 4 ∶ 3 rectangle. The wire width shall not be abrupt to avoid the discontinuity of wiring. When the circuit board is heated for a long time, the copper foil is easy to expand and fall off. Therefore, large area copper foil should be avoided. PCB manufacturing, PCB design and PCBA processing manufacturers will explain the precautions for PCB drawing at welding angle and PCB welding defects.