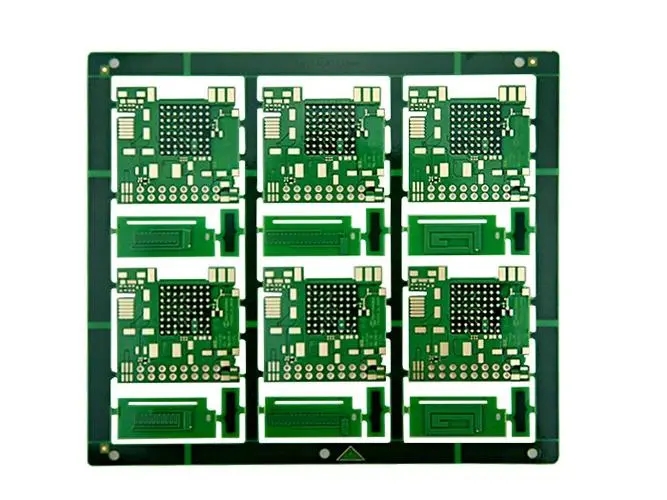
Detailed explanation of grid point setting in PCB layout design
Printed circuit board (PCB for short) is the base plate for assembling electronic parts, and is a printed board that forms point to point connection and printed components on a universal substrate according to a predetermined design. The main function of this product is to make all kinds of electronic components form the connection of predetermined circuit, play the role of relay transmission, and is the key electronic interconnection of electronic products. The manufacturing quality of printed circuit boards not only directly affects the manufacturing quality of electronic printed circuit boards, not only directly affects the reliability of electronic products, but also affects the overall competitiveness of system products. Therefore, printed circuit boards are called "the mother of electronic system products". The development level of PCB industry can reflect the development speed and technical level of electronic industry in a country or region to a certain extent.
Glass fiber yarn: glass fiber yarn is calcined into liquid state from silica sand and other raw materials in the kiln, pulled into very fine glass fiber through a very small alloy nozzle, and then hundreds of glass fibers are twisted into glass fiber yarn. Kiln construction investment is huge. It is a capital intensive industry. A 30000 ton kiln needs 400 million yuan. It takes 18 months to build a new kiln. It is difficult to grasp the business cycle. Once the ignition is started, it must be produced 24 hours a day. After about five years, it must be stopped for half a year for maintenance. The cost of entry and exit is huge. Glass fiber cloth: glass fiber cloth is one of the raw materials of copper clad laminate, which is woven from glass fiber yarn, accounting for about 40% (thick plate) and 25% (thin plate) of the cost of copper clad laminate. The manufacturing of glass fiber cloth is similar to that of weaving enterprises. The production capacity and quality can be controlled by controlling the rotation speed, and the specifications are relatively simple and stable. There has been little change in specifications since World War II. Different from CCL, the price of glass fiber cloth is most affected by the supply and demand relationship, and the price in recent years fluctuates between 0.50 and 1.00 dollars/meter. At present, Taiwan and mainland China account for about 70% of the world's production capacity. The relationship between upstream and downstream is the key to operation. The price of a loom is 100000~150000 yuan, and more than 100 looms can be normally produced. However, the capital requirements for subsequent heat treatment and chemical treatment equipment are high, reaching tens of millions. The capacity of weaving is easy to expand and flexible.
Copper foil: copper foil is the raw material that accounts for the largest proportion of the cost of copper clad laminate, accounting for more than 30% (thick plate) and 50% (thin plate) of the cost of copper clad laminate. Therefore, the price increase of copper foil is the main driving force for the price increase of copper clad laminate. Copper foil is widely used, not only in the CCL industry. When the CCL industry is in recession, copper foil manufacturers can switch to copper foil for other purposes. The price of copper foil is closely reflected in the price change of copper. With the rising of copper price, copper foil manufacturers shift the cost pressure to the downstream. High technical barriers in the copper foil industry lead to insufficient domestic supply. High grade copper foil still needs to be imported in large quantities, and the cost of investing in factories is also high. Copper clad laminate (CCL for short): It is a direct raw material of PCB, which is made of electronic grade glass fiber cloth as the base material, dipped in epoxy resin, dried, made into a bonding sheet in the semi curing state, and then coated with thin copper foil on one side, two sides, or multiple layers of the board.
The demand for capital in the CCL industry is relatively large, with about 50 million yuan for small-scale plants and a high concentration of about 100 in China. The CCL industry is a cost driven cyclical industry. In the upstream and downstream industrial chain structure, CCL has a strong bargaining power over PCB. As long as downstream demand is fair, it can transfer the pressure of rising costs to downstream PCB manufacturers. However, only the large-scale CCL can have a strong voice in the procurement of raw materials such as glass fiber cloth and copper foil. Due to the single use of CCL products, they can only be sold to PCB manufacturers. When PCB is in recession, they can only lower the price to ensure the utilization of production capacity.
PCB: Compared with upstream and downstream industries, the industrial concentration of printed circuit board is not high due to its characteristics; In the fierce market competition environment, only those enterprises with good market positioning and high operational efficiency can have long-term competitiveness. An ordinary PCB production line needs more than 20 million yuan, multilayer boards need to invest 50 million yuan, and HDI needs to invest more than 200 million yuan. Due to the huge industry and fine division of labor, there is a single station process outsourcing specializing in drilling, and the supply of low-grade products exceeds the demand. High end PCB industries, such as HDI, are capital and labor intensive industries and have high requirements for management and technology, which often become the bottleneck of capacity expansion.
PCB manufacturers, PCB designers and PCBA manufacturers will explain grid point settings in PCB layout design in detail.