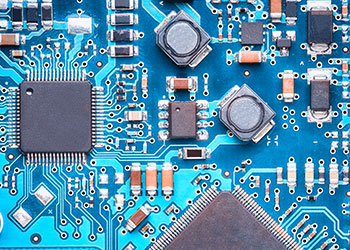
PCB Design and PCB Layout of Switching Power Supply
1 PCB layout: The impulse voltage connection should be as short as possible, where the input switch tube is connected to the transformer and the output transformer is connected to the rectifier tube The pulse current loop should be as small as possible, because the input filter capacitor is positive to the transformer and switch tube, while the loop capacitor is negative The output part of the transformer output terminal, from the rectifier tube to the output inductor to the output capacitor, returns to the transformer circuit X, and the capacitor should be as close to the input terminal of the switching power supply as possible. The input line should not be in parallel with other circuits, and should be avoided Y capacitor shall be placed at chassis grounding terminal or FG connection terminal A certain distance shall be kept between the common contact induction and the transformer to avoid magnetic coupling If it is not easy to handle, you can add a mask between the common mode inductor and the transformer The above items have a great impact on the EMC performance of switching power supply Generally, two output capacitors can be used, one close to the rectifier tube and the other close to the output terminal, which will affect the output ripple index of the power supply The parallel connection effect of two small capacity capacitors should be better than that of one large capacity capacitor The heating device must be kept at a certain distance from the electrolytic capacitor to extend the life of the whole machine Electrolytic capacitors are key to the life of switching power supplies, such as transformers, power transistors, and high-power resistors Keep a certain distance from electrolysis, and leave a space for heat dissipation between electrolysis. If conditions permit, it can be placed in the air inlet Attention shall be paid to the control part: the connection of high impedance weak signal circuit shall be as short as possible, such as sampling echo circuit Try to avoid interference during processing Current sampling signal circuit, especially current control circuit, is not easy to handle accident.
PCB board
2. Design and implementation of PCB switching power supply PCB layout
2.1 Switching power supply printed board wiring principle
Line spacing: With the continuous improvement and improvement of the printed circuit board manufacturing process Considering the components and production process used in the switching power supply, the line spacing of double-sided boards is usually set to 0.3mm, the line spacing of single-sided circuit boards is set to 0.5mm, and the line spacing of pad and pad, pad and via or via and via is set to 0.5mm to avoid "bridging" during welding With this kind of pipe, most sheet metal plants can easily meet the production requirements, control the production rate very high, and achieve a reasonable wiring density with more economic costs Line spacing is only applicable to signal control circuits and low-voltage circuits with voltage lower than 63V When the line to line voltage is greater than this value, the line spacing can generally be selected according to the empirical value of 500V/1mm In view of the clear provisions on line spacing in some relevant standards, the standards must be strictly followed, such as the connection between the AC input terminal and the fuse terminal Some power supplies have high capacity requirements, such as modular power supplies Generally, the distance between the conductors on the input side of the transformer is 1mm, which has been proved feasible in practice For power products with AC input and (isolated) DC output, the more stringent requirement is that the safety distance must be greater than or equal to 6mm Of course, it depends on the relevant standards and implementation methods Generally, the safety distance can be referred to by the distance on both sides of the echo optocoupler, and the principle is greater than or equal to this distance Slots can also be made on the printed board below the optocoupler to increase the creepage distance to meet the insulation requirements Generally, the distance between the input side wiring or components on the board of the AC input side and the uninsulated enclosure and radiator should be greater than 5mm, and the distance between the output side wiring or components and the enclosure or radiator should be greater than 2mm, or the safety regulations should be strictly observed
PCB board
Common methods:
Method 1. The above circuit board slotting method is applicable to some occasions with insufficient spacing By the way, this method is also commonly used to protect the discharge gap, which is very common in the tailboard of the TV picture tube and the AC input of the power supply This method has been widely used in modular power supply, and good results can be obtained under the condition of encapsulation
The second method is to use insulating paper, such as blue shell paper, polyester film, polytetrafluoroethylene orientation film, etc Generally, green paper or polyester film is used for general power supply to pad between the circuit board and the metal housing This material has high mechanical strength and certain moisture resistance Polytetrafluoroethylene (PTFE) alignment film is widely used in module power supply because of its high temperature resistance An insulating film can also be placed between the component and the surrounding conductor to improve the insulation resistance Note: The insulating layer of some equipment cannot be used as insulating medium to reduce the safety distance, such as the shell of electrolytic capacitor Under high temperature conditions, the outer skin may shrink A space shall be reserved at the front end of the large electrolytic explosion-proof tank to ensure that the electrolytic capacitor is free from pressure under special circumstances
2.2 Precautions for PCB copper wire routing
Trace current density: Now most electronic circuits are made of insulating board bound copper. The thickness of copper sheet of common circuit board is 35mm, and the current density value can be taken as the empirical value of/mm wiring according to 1A For specific calculation, please refer to the textbook To ensure the mechanical strength of the wiring, the line width should be greater than or equal to 0.3 mm (other non power circuit boards may have a smaller line width) The copper sheet is 70mm thick. The circuit board is also commonly used for switching power supply. This current density can be higher Add. Common PCB design tool software usually has design specification items, such as line width and line spacing. You can set dry board through-hole size and other parameters When designing a circuit board, the design software can automatically execute according to the specifications, which can save a lot of time, reduce part of the workload, and reduce the error rate Generally, double-sided boards can be used for circuits with high reliability requirements or high wire density It is characterized by moderate cost, high reliability and can meet most applications Some products in the modular power supply line also use multilayer boards, which are mainly convenient for integrating power devices such as transformer inductors, optimizing wiring and heat dissipation of power tubes It has the advantages of good processability, good consistency and good heat dissipation of transformer, but its disadvantages are high cost, poor flexibility and only suitable for industrial large-scale production Single panel and general switching power supply circulating in the market almost all use single side circuit board, which has the advantage of low cost. Some measures in design and production process can also ensure its efficiency Today, I will talk about some experience in the design of single-sided printed circuit boards Single panel is widely used in switching power supply circuits because of its low cost and ease of manufacture Because it has only one copper junction, it requires electrical connection and mechanical fixation of equipment Rely on that layer of copper and be careful when handling In order to ensure good welding mechanical structure efficiency, the single panel pad shall be slightly larger to ensure a good bonding force between the copper sheet and the base plate. When subjected to vibration, the copper sheet will not peel or break Generally, the width of the welding ring should be greater than 0.3 mm. The diameter of the backing hole should be slightly larger than the diameter of the device pin, but it should not be too large Ensure that the welding connection distance between the pin and the bonding pad is short, and the size of the disk hole does not hinder the normal inspection. The diameter of the pad hole is usually 0.1-0.2mm larger than the pin diameter. The multi pin device can also be larger to ensure smooth inspection The power connection should be as wide as possible, in principle, the width should be greater than the diameter of the gasket The wire must be wired when the connection meets the pad (commonly known as teardrop generation) to avoid breaking the wire and the pad under certain conditions In principle, the line width should be greater than 0.5mm. Components on a single panel should be close to the circuit board For equipment requiring overhead heat dissipation, bushings shall be added on the pins between the equipment and the circuit board to support the equipment and add insulation It is necessary to minimize or avoid external influences on the connection between pads and pins And improve the firmness of welding Heavy components on the circuit board can add support connection points to enhance the connection strength with the circuit board, such as transformers and power equipment radiators Single welded surface pins can remain longer without affecting the distance from the housing The advantage is that the strength of the welding part can be improved, and the welding area and virtual welding phenomenon can be found immediately When the pin is very long and cut to the leg, the force on the welding part is small In Taiwan and Japan, the device pin is usually bent at a 45 degree angle with the circuit board on the welding surface, and then welded. The principle is the same as above Today, I will talk about some problems in double-sided board design In some applications with higher requirements or higher track density, double-sided printed boards are much better than single panel in efficiency and number of seats The double-sided plate pad has higher strength, because the hole has been metallized, the welding ring can be smaller than the single panel, and the hole diameter of the pad hole can be slightly larger than the pin diameter, because during welding, the solder solution can penetrate to the top layer through the solder hole Add pads for welding reliability But there is also a disadvantage If the hole is too large, part of the equipment may float under the influence of tin spraying during wave soldering, resulting in some defects
2.3 It is used to deal with traces of high current. Line width can be handled according to the previous post If the width is not enough, it can usually be solved by adding thickness through tinning trace There are many ways
1. Set the track as the pad content, and remember that during the manufacturing process of the circuit board, the trace will not be covered by the solder mask, and tin will be plated during the hot air leveling process
2. Place a pad on the wiring, set the pad to the shape that needs wiring, and pay attention to setting the pad hole to zero
3. Place the wire on the solder mask This method is flexible, but not all circuit board manufacturers will understand your intention. You need to explain it in words Do not use solder resist on the solder mask where the wires are placed
Several methods of tinning circuits are as follows It should be noted that if wide traces are tinned, a large amount of solder will be bonded after welding, and the distribution will be uneven, which will affect the appearance Generally, the thin strip with a tin plating width of 1~1 is 5mm, and the length can be determined according to the circuit The tin plating part is separated by 0. 5~1mm. The double-sided circuit board is used for layout and wiring, which makes the wiring more reasonable As for grounding, power grounding and signal grounding must be separated The two grounds can be combined at the filter capacitor to avoid accidental instability caused by large pulse current passing through the signal ground connection The signal control loop shall be grounded as far as possible A trick is to try to place ungrounded traces on the same wiring layer and ground wires on another layer The output line usually passes through the filter capacitor first and then is loaded The input line must also pass through the capacitor first, and then the transformer The theoretical basis is to let ripple current pass through the filter capacitor Voltage reverberation sampling. In order to avoid the influence of large current passing through the wiring, the sampling point of the reverberation voltage must be placed at the power output to improve the load effect index of the whole machine The wiring change from one wiring layer to another is usually connected through via, and is not suitable for being realized through the device pin pad, because this connection relationship may be destroyed when inserting the device. When every 1A current passes through, there should be at least two via, and the diameter of the via should be greater than 0. In principle, 5mm. Generally, it is 0.8mm to ensure the processing reliability. The device heats up In some low-power power supplies, circuit board traces can also be used for heat dissipation Its feature is that the trace is as wide as possible to increase the heat dissipation area Solder resist is not used If possible, through holes can be placed evenly to enhance PCB