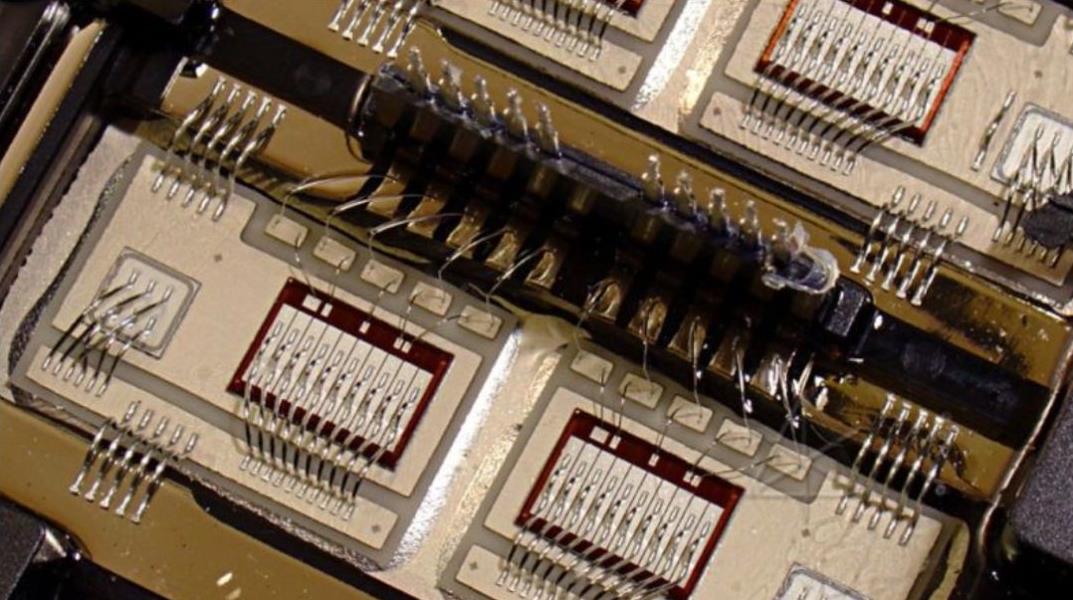
Key points of PCB design for switching power supply
In the design of switching power supply, PCB design is a very critical step, which has a great impact on the efficiency of power supply, electromagnetic compatibility requirements, reliability, and manufacturability With the development of electronic technology, the switching power supply is becoming smaller and smaller in size, higher in operating frequency and higher in density of internal components, which makes the anti-interference requirements for PCB layout and wiring more and more strict, Reasonable and scientific PCB design will make your work twice the result with half the effort
PCB board
1. Layout requirements
The layout of the PCB is more delicate, not just putting it on and pressing it down Layout should follow seven points of all PCB boards:
(1) The first principle of the layout is to ensure the wiring rate, when mobile devices, pay attention to the connection of flying wires, and put the devices with connection relationships together
(2) Take the components of each functional circuit as the center and lay out around it. The components should be evenly, neatly and compactly arranged on the PCB, so it is not only beautiful, but also easy to install, weld and mass produce Minimize and shorten the leads and connections between components; The oscillator circuit and filter decoupling capacitor shall be close to the integrated circuit, and the grounding wire shall be short
(3) When placing components, consider future welding and maintenance Try to avoid placing short components between two high height components This is unfavorable to production and maintenance The module should not be too dense. However, with the development of electronic technology, the current switching power supply is becoming smaller and more compact. In conclusion, it is necessary to balance the degree between the two, not only for welding and maintenance, but also for compactness The actual chip processing capacity also needs to be considered According to IPC-A-610E standard, the accuracy of component side deviation shall be considered, otherwise it is easy to lead to tin connection between components, and even the component distance is not enough due to component deviation
(4) Photoelectric coupling devices and current sampling circuits are easy to be interfered. They should be far away from equipment with strong electric and magnetic fields, such as large current wiring, transformers, and high potential pulsating devices
(5) When placing components, give priority to the loop area of high-frequency pulse current and large current, and minimize their impact to suppress the radiated interference of switching power supply
(6) The area where the high frequency pulse current flows should be false away from the input and output terminals The transformer is too close to the inlet, and the electromagnetic radiation energy directly acts on the input and output Therefore, the EMI test failed After the method on the right side is changed, the transformer is far away from the inlet, and the distance between the electromagnetic radiation energy and the input and output terminals is increased. The effect is significantly improved, and the electromagnetic interference test is passed
(7) The layout of heating elements (such as transformers, switch tubes, rectifier diodes, etc.) should consider the effect of heat dissipation, and key components (such as IC) that are sensitive to temperature should be far away from the heating elements and generate more heat The equipment shall be kept at a certain distance from electrolytic capacitors and other equipment that may affect the service life of the whole machine
(8) Pay attention to the height of the bottom element when laying out the board. For example, because the DC-DC power module used for packaging is relatively small, if the height of the bottom assembly is unbalanced on all four sides, the pin height on both sides will be higher while the pin height on the other side will be lower during packaging
(9) Pay attention to the opposite ability of the control pins during layout. The distance between the corresponding circuit components should be long enough, for example, the Ctrl pin (low level shutdown). The capacitance of the circuit is different from that of the input and output terminals Filtering. In addition, the anti-static ability of the whole module is weak, so you must ensure that there is a sufficient safety distance
2. Wiring principle
(1) Small signal traces should be kept away from high current traces as much as possible If it is unavoidable to be parallel, keep enough distance to avoid interference of small signal track
(2) The key small signal wiring, such as current sampling signal line and optocoupler echo signal line, etc, Minimize the area enclosed by the loop
(3) There should not be too long parallel lines between adjacent ones (of course, parallel wiring of the same current loop is possible) The wiring should not be surprisingly centered (ie: ⤠90 °), right angles and acute angles will affect The power efficiency of high-frequency circuits
(4) The power circuit and the control circuit should be separated The components around the main PWM control IC are grounded to the ground pin of the IC, then led from the ground pin to the large capacitance ground wire, and then connected to the power ground The components around the auxiliary TL431 are grounded to pin 3 of the TL431 and then to the ground of the output capacitor In the case of multiple integrated circuits, parallel single point grounding pipes are used
(5) Do not route high frequency components (such as transformers and inductors) on the bottom layer If it is unavoidable, masks can be used, such as the top layer high frequency component, and the control circuit faces the bottom layer Pay attention to the copper mask of the layer where the high-frequency components are located to prevent high-frequency noise radiation from interfering with the control circuit at the bottom
(6) Pay special attention to the routing of the filter capacitor. A part of the ripple & noise will go out through the routing. The filtering effect of the image on the right will be better The ripple & noise will be completely filtered out by the filter capacitor.
(7) The power line and the ground line are as close as possible to reduce the enclosed area, so as to reduce the electromagnetic interference caused by cutting the external magnetic field circuit and reduce the external electromagnetic radiation of the circuit The wiring of power line and ground wire shall be as thick and short as possible to reduce the circuit resistance. The corners shall be smooth and the wire width shall not change suddenly
(8) A large area of bare copper can be used for heat dispersion under components with large heat (such as TO-252 packaged MOS tubes), which can improve the reliability of components The narrow part of the power tracking copper foil can be used for tinning with bare copper to ensure the flow of high current
3. Safety distance and process requirements
(1) Electrical clearance: the short distance measured along the air between two adjacent conductors or a conductor and the surface of an adjacent conductive housing. Creepage distance: the short distance measured along the insulating surface between two adjacent conductors or conductors and adjacent conductive enclosure surface If the space of module PCB is limited and the creepage distance is not enough, slotting can be used As shown in Figure 14, open the isolation slot at the optocoupler to achieve good primary and secondary isolation Generally, the slot width is 1mm If you want to open a smaller slot (such as 0.6 mm, 0.8 mm), you usually need special instructions Find manufacturers with high PCB processing accuracy Of course, the cost will increase
(2) The distance requirement from the component to the edge of the board. The distance between the components at the edge of the circuit board and the edge of the circuit board is usually not less than 2mm It is used for small DC-DC modules of 10W or less. Because the module volume and height are relatively small and the input and output voltages are not high, in order to meet the miniaturization requirements, it is necessary to leave a distance of at least 0.5mm or more The distance between the large area copper foil and the outer frame shall be at least 0.20mm or more Because it is easy to mill the copper foil when milling the shape, the copper foil will lift and the flux will fall off
(3) If the width of the trace into the round pad or the via hole is smaller than the diameter of the round pad
(4) When the pins of the SMD device are connected to a large area of copper foil, thermal isolation shall be carried out. Otherwise, due to the rapid heat dissipation during reflow soldering, it is easy to cause faulty soldering or desoldering
(5) When the PCB board has been assembled, it is necessary to consider the feasibility of transshipment to ensure that the distance between the component and the edge of the circuit board is sufficient, and at the same time, consider whether the stress of the sub board will cause the component to warp It can be properly grooved to reduce the stress when the PCB is broken Component A is placed parallel to the direction of the V-shaped notch, and the stress at fracture is less than that of component B; Component C is farther away from the V-notch than component A, and when it breaks, the stress is less than that of component A Of course, the above is just some personal experience in PCB design of switching power supply