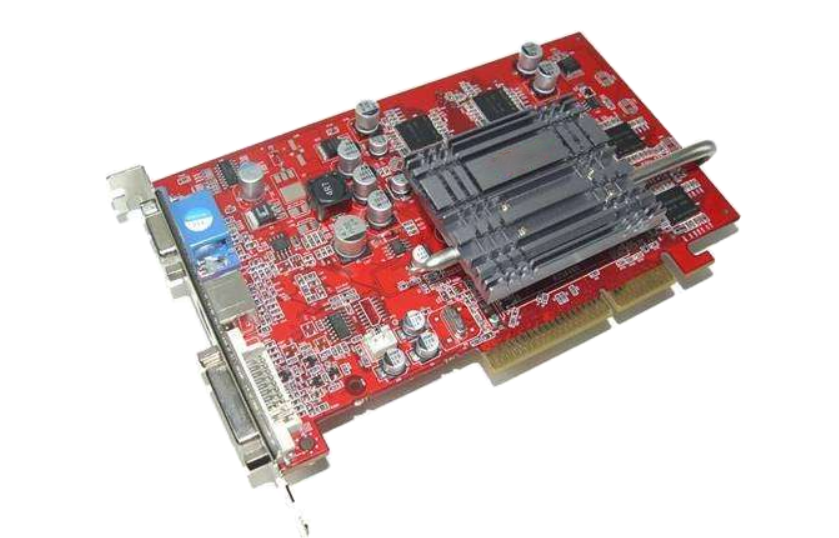
What is through hole reflow (PHR)
1、 What is through hole reflow (PHR)
In PCB assembly process, through hole reflow (THR) is used to complete the welding of through hole plug-in components.
When traditional methods are used to weld hybrid assembled PCBs, the general process flow is:
Printing solder paste → mounting SMC/SMD → reflow soldering surface mounted components → inserting → THC/THD → wave soldering THC/THD.
THR uses a special template with many needle tubes installed, adjusts the position of the template to align the needle tubes with the through hole pads of the inserted components, and uses a scraper to leak the solder paste on the template onto the pads,
Then install the plug-in components. Finally, the plug-in components and the SMD components are welded together through reflow soldering.
When THR is used, both SMC/SMD and THC/THD are completed in the reflow welding process
Welded. The appearance of THR has enriched the welding means, simplified the process flow and improved the production efficiency.
2、 Advantages of through-hole reflow process:
1. The existing SMT equipment can be used to group THC/THD to save cost and investment.
2. THC/THD can be mounted on current automatic multi-function mounting equipment; THR is used on surface mount PCBs, abandoning the traditional wave soldering process and manual insertion process, and realizing a single SMT production line can complete the assembly of all PCBs.
3. Multiple operations are simplified into a comprehensive process.
4. Less equipment, materials and personnel are required.
5. It can reduce production cost and shorten production cycle.
6. It can reduce the high defect rate caused by wave soldering.
7. One or more heat treatment steps can be omitted, thus improving solderability and reliability of electronic components.
THR has special requirements for temperature resistance of components, through hole pad design, template design, solder paste printing and reflow soldering.
3、 Disadvantages of through-hole reflow welding process
1. The amount of solder paste is very large.
2. There are many residues formed after the flux volatilizes, which will pollute the machine and PCB.
3. The probability of voids in solder joints increases.
3. As through-hole components go through the entire reflow temperature curve, they must withstand the thermal shock with a peak temperature of 240 ℃ for 30s. Through hole components must consider the adaptability of reflow soldering. Elements shall be made of resins that do not deteriorate in 183 ℃ (preferably 220 ℃ for 40s), 235 ℃ peak temperature, and (60~90) seconds. Component manufacturers also need standards for bending, dimensional stability, shrinkage, and dielectric properties.
4. The standard of QJ165B butt through hole welding point is the existence of welding wetting angle on PCB welding surface (side B) and the filler metal is filled with at least 100% through hole of plate thickness. The main technical challenge of THR is how to print enough solder paste in and around the through-hole of components with high-density pins, so as to form an acceptable solder joint on side B to meet the requirements of QJ165B. Because in THR, it is not a problem to form a welding wetting angle on side A, because solder paste is printed from side A.
5. Since the volume of metal components in the solder paste accounts for about 50% of the volume of the solder paste, it is necessary to optimize the through hole pad design and template design to ensure sufficient amount of solder paste and prevent less tin and voids.
6. Compared with the common wave soldering process, the technical difficulty of THR is relatively high: PCB thickness, hole size, PCB pad size, solder paste printing amount, component lead diameter, component pin spacing, metal content of solder paste, design of printing screen, component installation and solder joint detection will affect the shape of solder joints. In addition, the filler amount of the metallized hole is also related to the opening size of the printed screen.
7. THR has special requirements for component installation design
1) Metallized hole design
(1) Round lead: the hole diameter of standard metallized hole is round lead diameter+0.254mm.
(2) Rectangular lead: the hole diameter of standard metallized hole is diagonal+1.27mm.
2) Pad size
When considering the minimum pad size, the metallized hole size, PCB manufacturing tolerance and the required minimum land must be considered.
Minimum land is defined as the minimum amount of metal from the edge of the metallized hole to the outer diameter of the pad.
Minimum pad diameter=last metallized hole diameter+2 (minimum ring)+PCB manufacturing tolerance
The minimum pad size reduces the amount of solder paste needed to form the wetting angle of A and B faces.
3) Clearance between pad and adjacent conductor
There should be enough clearance between the pad of the metallized hole components and the adjacent metal conductors around. If there are metallized holes too close, the solder will be equally divided between the metallized holes and the pad, causing bridging. There shall be no other exposed metal, hole or legend solder mask in the required clearance area around the pad of metallized hole components. Legend The solder mask may affect the flow of solder paste during reflow and separate it to form solder beads.
4、 Conclusion
THR is a reflow soldering technology that emerged in the 1990s to fill the gap between traditional reflow soldering and through hole plug-in components. THR overcomes many shortcomings of wave soldering, simplifies the process flow, and improves the production efficiency,
It is more suitable for welding plug-in components in high-density circuit boards. However, due to the limitation of pin length, pin end shape and the volume of metal components in the solder paste, especially the complexity of calculation and control of the amount of solder paste when using THR, it is difficult for THR to meet the through hole penetration rate of more than 100%. Therefore, for high reliability circuit boards, especially for through hole plug-in components such as connectors that need to bear a certain amount of mechanical force for military products, THR should be used with caution.
Both THR and selective wave soldering are process technologies to solve the problem of soldering through hole plug-in components on PCB. Comparatively speaking, we prefer to use selective wave soldering. Especially for gold plated electrical connectors, selective wave soldering has incomparable advantages over THR.
To sum up, the main direction of THR process development is still to improve the process and components, especially for aerospace, aviation and military electronic equipment with high reliability requirements, which must be carefully considered.