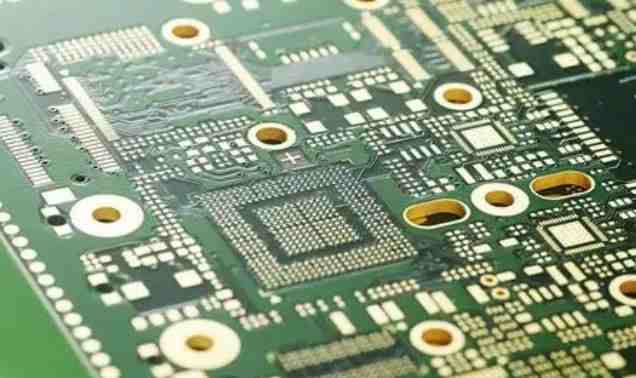
PCB manufacturers in the PCB process, the use of PCB dry film technology generally encountered some PCB film faults,PCB film common faults and solutions are as follows:
1. Dry film is not firmly attached to copper foil
(1) Copper foil surface is not clean, there is oil or oxidation layer. Clean the board again and wear gloves.
(2) The solvent volatilization and deterioration in the dry film solvent. Store at low temperature, do not use expired dry film.
(3) Fast transmission speed, low PCB film temperature. Change the PCB coating speed and PCB coating temperature.
(4) The ambient humidity is too low. Maintain the relative humidity of the production environment at 50%.
2. Bubbles appear between dry film and copper foil surface
(1) The surface of copper foil is uneven, with pits and scratches. Increase the PCB film pressure, the plate transfer should be handled lightly
Put it down gently.
(2) The surface of the hot press roll is uneven, and there are pits and rubber film drilling. Pay attention to protect the flat surface of the hot press roll.
(3) The PCB film temperature is too high, reduce the PCB film temperature.
3, dry film wrinkles
(1) The dry film is too sticky, put the board carefully.
(2)PCB film before the board is too hot, the board preheating temperature should not be too high.
4. Leftover glue
(1) The dry film quality is poor, replace the dry film.
(2) The exposure time is too long, shorten the exposure time.
(3) Developer failure, change the developer.
Analysis PCB circuit board electroplating copper common problems
At present, the plating of domestic circuit board manufacturers is more and more advanced, bright copper plating is based on copper sulfate and sulfuric acid as the basic components, the introduction of appropriate additives or other brighteners, so that the process characteristics of the plating solution can be improved and improved, and directly obtain the mirror bright copper layer. It is widely used in decorative multi-layer plating intermediate layer and copper plating layer of printed circuit board, eliminating mechanical polishing. However, the coating is sometimes not bright in production. The common copper sulfate and sulfuric acid used in the new plating solution are not pure, such as the mass fraction of industrial sulfuric acid ≥92.5%, containing a lot of iron and organic impurities, if not treated, the plating will make the coating not bright. Even with reagent grade sulfuric acid, this situation will occur if not treated, because copper sulfate has impurities more or less. Before adding sulfuric acid, H2O21~2mL/L with mass fraction of 30% and activated carbon 0.5~1.0g/L can be combined with dissolved copper sulfate solution (pH 4). The property of easy precipitation of trivalent iron hydroxide is used to remove iron impurities. The effect of organic impurities can be eliminated at the same time by adding activated carbon for adsorption. So you start plating, you get a bright copper layer.
The metal impurities and organic impurities produced by the long-term use of the plating solution will accumulate more and more, obviously, the plating solution is not pure. If the circuit board manufacturer does not do regular treatment according to the process requirements, when the mass concentration of iron impurities reaches more than 10g/L, the current efficiency and the brightness of the coating decrease significantly. 40g/L. According to the observation, the color of the plating solution is light, and under the condition of confirming the low mass concentration of the components in the plating solution, 40g/L copper sulfate and 15g/L sulfuric acid are added to reduce the influence of iron impurities; Then the plating tank was restored to normal and the bright copper layer was plated.
The consumption of brightener in acid bright copper plating solution is related to many factors, such as the type, shape, surface state of the workpiece and the mass concentration of inorganic and organic impurities and copper sulfate in the plating solution. Especially the lack of Cl-, even the brightener in the normal range is difficult to obtain good levelling bright coating; When the mass concentration of Cl- is too high, the consumption of brightener will be accelerated.
In the plating solution used for a long time, part of the brightener is consumed with the removal of the workpiece and the inclusion of the coating. Some will break down into organic impurities; Some of them remain in the plating solution and change the composition of the brightener itself. These conditions may affect the brightness of the coating, resulting in coating defects. In addition to the use of brightener according to the instructions used in the production, but also strive to accurately grasp the consumption of brightener, and pay attention to the accumulation of experience and careful observation, the use of less and more methods in time to add brightener, in order to keep the brightener constant in the plating solution.
Excellent bright levelling and small brittleness of coating; High allowable current density, high cathode current efficiency, fast plating speed; No complexing agent, little ammonia nitrogen content, simple wastewater treatment; This process has become the mainstream process of cyanide-free copper plating and is widely used by domestic PCB manufacturers. Especially in plastic electroplating, indispensable. It is expected that in a long time, it is difficult to replace other copper plating processes.