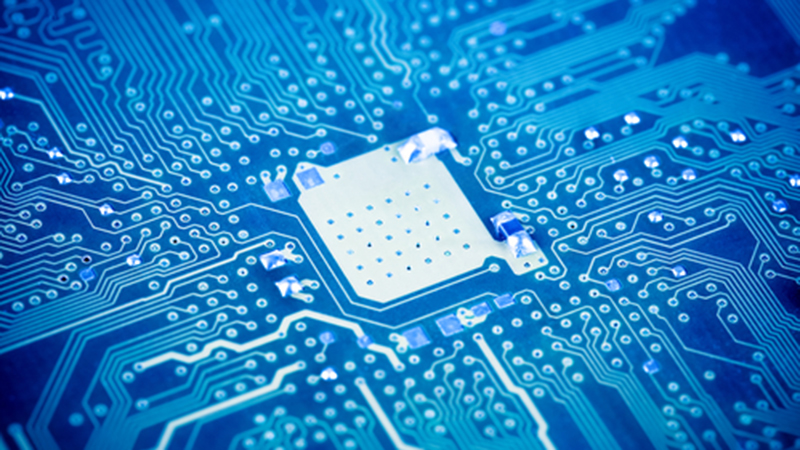
PCB operational amplifier circuit design skills
Printed circuit board (PCB) layout plays a critical role in high-speed circuits, but it is often one of the last steps in the circuit design process. There are many aspects of high-speed PCB routing, and a great deal of literature has been written on this topic. This paper mainly discusses the layout of high-speed circuits from a practical point of view. The main purpose is to help new users draw attention to the many different issues that need to be considered when designing PCB layouts for high-speed circuits. Another purpose is to provide a kind of refresher material for customers who have not touched PCB layout for some time. Due to the limited space, it is impossible to discuss all the issues in detail in this article, but we will discuss the key parts that have the greatest effect on improving circuit performance, shortening design time, and saving modification time.
Although the focus here is on circuits related to high-speed operational amplifiers, the issues and methods discussed here are generally applicable to the layout of most other high-speed analog circuits. When operational amplifiers operate at very high radio frequency (RF) frequency bands, the performance of the circuit is largely dependent on the PCB layout. A high-performance circuit design that looks good on the "paper sheet" ends up with mediocre performance if it is compromised by sloppy layout. Forethought and attention to important details throughout the layout process will help ensure expected circuit performance.
schematic diagram
Although a good schematic does not guarantee a good layout, good layout starts with a good schematic. Be deliberate when drawing a schematic and must consider the flow of signals throughout the circuit. If you have normal steady signal flow from left to right in the schematic, you should have equally good signal flow on the PCB. Give as much useful information as possible on the schematic. Because sometimes the circuit design engineer is not there, the customer will ask us to help solve the problem of the circuit, and the designers, technicians and engineers who do this work will be very grateful, including us.
Besides the usual reference designators, power consumption, and error margins, what information should be given in the schematic? Here are some suggestions for turning an ordinary schematic into a top-notch one. Add waveforms, mechanical information about the shell, printed line length, and blank areas; indicate which components need to be placed on the PCB; give adjustment information, component value ranges, heat dissipation information, control impedance printed lines, notes, and brief circuits Action descriptions... (and others).
don't believe anyone
If you did not design the wiring yourself, be sure to allow ample time to double-check the wiring person's design. A small prevention is worth a hundred times the remedy here. Don't expect the wiring guy to understand your thinking. Your input and guidance are most important early in the wiring design process. The more information you can provide, and the more involved you are in the overall layout process, the better the resulting PCB will be. Set a tentative completion point for the wiring design engineer - follow your desired wiring progress report for a quick check. This "closed loop" approach prevents wiring from going astray, minimizing the possibility of rework.
Instructions that need to be given to the layout engineer include: a short description of the function of the circuit, a sketch of the PCB showing where the inputs and Consumption, ground, analog, digital, and RF); what signals are needed on each layer; where important components are required; where exactly are bypass components; which traces are important; which lines require controlled impedance traces ; which lines need to match the length; the size of the components; which printed lines need to be far away from each other (or close); which lines need to be far away from each other (or close); On the top of the PCB, which ones are placed below. Never complain that you need to give someone too much information - too little? Yes; too much? No.
A learning experience: About 10 years ago, I designed a multi-layer surface mount circuit board - the board has components on both sides. The board is fixed in a gold-plated aluminum case with many screws (because of the strict shock resistance index). The pins that provide the bias feedthrough go through the board. This pin is connected to the PCB with a solder wire. This is a very complicated device. Some components on the board are for test setup (SAT). But I have clearly specified the position of these components. Can you guess where these components are installed? By the way, under the board. It's not happy when product engineers and technicians have to take the whole thing apart, set it up, and put it back together again. I haven't made that mistake since then.
Location
Just like in a PCB, location is everything. Where to place a circuit on the PCB, where to place its specific circuit components, and what other circuits it is adjacent to are all very important.
Usually, the location of the input, output, and power supply is predetermined, but the circuitry between them requires "individual creativity." That's why paying attention to wiring details will pay off hugely. Starting from the location of key components, consider it according to the specific circuit and the entire PCB. Specifying the location of critical components and the routing of signals from the start helps ensure that the design works as intended. Getting the design right the first time reduces cost and stress—and shortens development cycles.
Bypass power
Bypassing the power supply at the power supply side of the amplifier to reduce noise is an important aspect of the PCB design process—whether for high-speed op amps or other high-speed circuits. There are two common configurations for bypassing high-speed op amps.
Power Supply Ground: This method, which is most effective in most cases, uses multiple capacitors in parallel to connect the power supply pins of the op amp directly to ground. Usually two capacitors in parallel are sufficient—but adding parallel capacitors may benefit some circuits.
Capacitors of different capacitances in parallel help ensure that the power supply pins see only low alternating current (AC) impedance over a wide frequency band. This is especially important at frequencies where the op amp power supply rejection ratio (PSR) rolls off. This capacitor helps compensate for the reduced PSR of the amplifier. Maintaining a low-impedance ground path over many decades will help ensure that unwanted noise cannot enter the op amp. Figure 1 shows the advantage of using multiple capacitors in parallel. At low frequencies, large capacitors provide a low impedance path to ground. But once the frequency reaches their own resonant frequency, capacitors become less capacitive and gradually become inductive. This is why it is important to use multiple capacitors: as the frequency response of one capacitor starts to roll off, the frequency response of the other capacitor kicks in, so the AC impedance can be kept very low over many decades.
Figure 1. Capacitor impedance vs. frequency.
Start directly at the op amp's supply pins; capacitors with the smallest capacitance value and physical size should be placed on the same side of the PCB as the op amp—and as close to the amplifier as possible. The ground terminal of the capacitor should be connected directly to the ground plane with the shortest lead or trace. The aforementioned ground connections should be made as close as possible to the load side of the amplifier to minimize interference between the power supply and ground terminals. Figure 2 shows this connection method.
Figure 2. Shunt capacitors to bypass supply terminals and ground.
This process should be repeated for the next largest value capacitor. It's best to start with a 0.01 µF minimum capacitor value and close by with a 2.2 µF (or larger) electrolytic capacitor with low equivalent series resistance (ESR). The 0.01 µF capacitors in an 0508 case size have very low series inductance and excellent high frequency performance.
Supply-to-supply: Another configuration uses one or more bypass capacitors across the positive and negative supply terminals of the op amp. This method is usually used when it is difficult to arrange four capacitors in the circuit. Its disadvantage is that the case size of the capacitor may increase because the voltage across the capacitor is twice the value in the single-supply bypass method. Increasing the voltage requires increasing the rated breakdown voltage of the device, which means increasing the case size. However, this approach can improve PSR and distortion performance.
Because each circuit and wiring are different, the configuration, quantity and capacitance value of capacitors should be determined according to the requirements of the actual circuit.
parasitic effect
Parasitics are those little glitches (literally) that sneak into your PCB and wreak havoc in your circuit, giving you headaches and not knowing why. They are the hidden parasitic capacitances and inductances that permeate high-speed circuits. These include parasitic inductance formed by package leads and excessive trace length; parasitic capacitance formed between pad to ground, pad to power plane and pad to trace; interaction between vias, and Many other possible parasitic effects. Figure 3(a) shows a typical non-inverting operational amplifier schematic. However, if the parasitic effects are considered, the same circuit may become as shown in Figure 3(b).