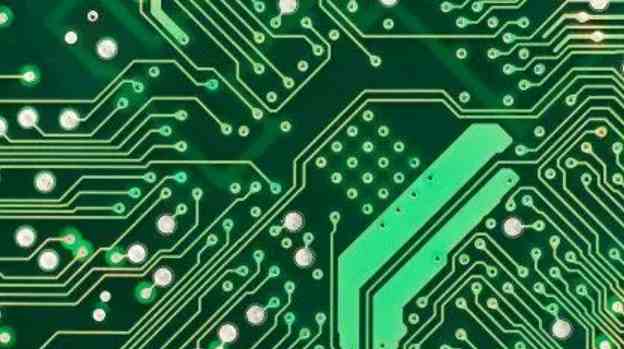
PCB circuit board and FPC flexible circuit board hot pressing machine heating methods now mainly have steam, superhot water, hot oil three methods.
A. Steam heating
The steam is sent directly from the steam boiler to the laminator. The temperature of steam is directly proportional to the steam pressure, only need to control the steam pressure, can reach the purpose of temperature control. When steam is used as heat source, the temperature difference of laminating machine fluctuates greatly. Hot plate cooling can be cooled directly with cold water. The composition of steam heating equipment is simple and less investment, so it is still selected by many copper clad factories.
B. Heat with overheated water
The steam boiler heats the superheated water storage tank. When the temperature reaches the set value, the steam boiler only compensates the heat loss of the superheated water storage tank. Therefore, this plan is selected to save energy by comparison. The superhot water storage tank and the laminating machine have a loop. When the laminating machine needs heating, the superheat in the storage tank is pumped into the hot press plate of the laminating machine by the pump. The hot press plate itself has a heat cycle. When the heat loss fails to meet the set requirements, the storage tank will fill in some fresh superhot water to ensure that the temperature of the hot press plate adheres to the range of skill requirements. So the temperature difference can reach within the range of ±1℃. When cooling, the laminator is returned to the hot water through a heat exchanger to gradually cool the hot water to end. Can also be a cooling water circuit alone to end the hot plate cooling. The choice of hot water relatively large investment, in the domestic copper clad plant has not seen the use of reports, foreign copper clad plant used more.
C. Heat with hot oil
Hot oil heating method is similar to superhot water, also through a hot oil storage tank to end. The hot oil boiler heats the hot oil storage tank and the hot oil storage tank heats the laminator. The hot press plate itself has a heat cycle, when the temperature of the hot press plate is lower than the set value, the hot storage tank will be filled with some fresh hot oil to adhere to the hot press plate temperature within the set range, usually the temperature difference can be controlled within the range of ±1℃, to meet the production needs of copper clad plate. Cooling is to circulate the hot oil of the hot press plate through one or several heat exchangers to gradually cool the hot oil to end the purpose of gradually cooling the hot press plate. Because the cooling process has a certain impact on the warping degree and scale stability of goods, there are a variety of methods to plan the cooling of laminating machine. It not only needs to get used to the slow and then fast cooling demand of skills, in order to ensure the quality of goods, but also will not make the production cycle too long, and should be conducive to energy saving. Heating with superheated water, like steam, superheated water temperature is also proportional to pressure, so the system pressure is high, very dangerous. The heating of hot oil is normal pressure, and the system pressure is the pressure of transporting hot oil pump, which will not be dangerous. The cost of hot oil system is also high. Because of its high temperature control precision, it is assumed that the production demand for higher heating temperature can also end, because the thermal decomposition temperature of hot oil is above 310℃, and steam and superhot water is not up to, and there are many domestic copper clad plants choose oil heating system.
When superheated water and hot oil are selected as the heat source of laminating machine, the heat demand of laminating machine should be carefully calculated to determine the heating ability of hot oil boiler and the volume of hot oil storage tank. When planning, leave room for plant expansion.
Using this process can better let the anti-rust layer and product combination, so as to better protect the workpiece. Aiming at this process, some customers have done salt spray test, and the results found that the products treated by this process can greatly extend the salt spray test time.
When is the CULLYGRAT chemical deburring process most effective?
• When complex parts with internal holes or perforated, multi-sided edges and acute angles cannot be treated by conventional processes
• When small, delicate workpieces can be treated as bulk materials using the CULLYGRAT® process without risk of surface damage
• When the workpiece not only needs to be deburred, but also needs to change the macro geometry
• When a clean metal surface must be obtained
• When continuous batch production is required
• When the required dimensional tolerance range is very small, and the accuracy must be guaranteed to be accurate reproduction
The advantages of CULLYGRAT burr removal process
• Reliable process (simple equipment such as bucket, basket, tray or hanging device can be soaked)
• The quality and service life of CULLYGRAT® processed work is significantly improved
• The burr removal amount of each batch of goods can be accurately controlled, the treatment effect is uniform, so it can be processed standard parts
• Burrs on flexible, delicate workpieces that do not require mechanical treatment, the CullygratO treatment is not limited by their structure and size
• Superior to traditional deburring processes such as scraping, roller polishing or grinding without damaging parts with extremely sensitive surfaces
• burrs that are extremely difficult to remove and cannot be removed by conventional processes (e.g. corner burrs) or, if they can be removed, require a great deal of Labour and material, or are removed piece by piece by explosion. With the CULLYGRAT® process, burrs can be removed in large batches, all at once, without distortion
• After treatment, the workpiece surface is very clean. The subsequent electroplating treatment can be carried out smoothly
• The surface is smooth and smooth, with residual roughness up to 0.1µl
• The holes that form under the surface due to mechanical treatment, leading to corrosion after electroplating or coating, are not available for CULLYGRAT®
• Cullygrat® parts were subjected to salt spray corrosion tests for a full 95 hours longer than other parts
• No hydrogen embrittlement occurs during processing
• The solution can be stored indefinitely. You just need to increase the concentration
• The resulting wastewater is easy to treat and does not pollute the environment. About 16% can be disposed of by combustion
• The CULLYGRAT® burr soaking process does not form crystals or deposits, eliminates the need for costly cleaning of containers and pumps, or costly waste disposal for crystallization
• Compared with conventional deburring process, it can save personnel and production costs
• Production equipment can never stop.