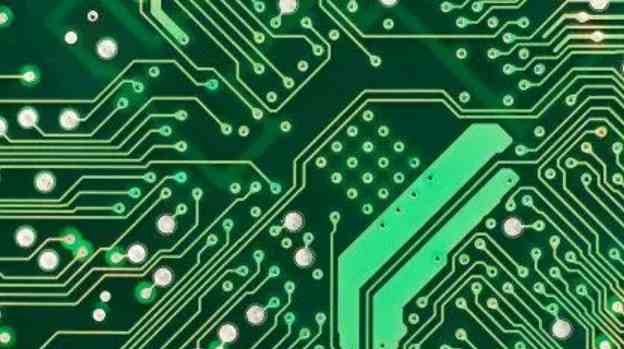
1. Method for control of electroplating thickness
1. Principle: The thickness of each metal plating is related to current density and plating time.
2. Method: Firstly, the area of each workpiece should be calculated, and then the current density of each workpiece should be determined according to the requirements of electroplating process. For example, the RF port area of BYD's plug is about 0.13dm2, and the current density required by the tinning process is 1.5A/dm2, so the plating current of each workpiece is about 0.20A. If 72 pieces per hang, the plating current of each hang should be 15A. After the current is determined, the thickness is only related to time. According to electrochemical calculation, when the current density is 1.5A/dm2, it takes about 1.5 minutes to electroplate the tin coating of 1u, and 4.5 minutes to electroplate the tin coating if the coating thickness is 4u.
3. The thickness mentioned in the second point above is the average thickness of the coating, because the workpiece has concave and convex, so the current density of each place is not the same, resulting in different parts of the thickness is not the same, the more complex the workpiece, the greater the thickness difference. There are mainly the following ways to reduce the thickness difference:
A. Add additives to the plating solution to reduce the thickness difference;
B. Electroplating with low current as far as possible; Using cathode movement;
C. Adopt appropriate shielding measures in the high current area of the workpiece, etc.
Two, coating thickness calculation common unit
1, micron nm conversion 0.001 mm (mm)=1 micron (μm) is one thousandth of a millimeter
2, micro inch uin is usually said u" (read mai) convert 1um=39.4uin≈40uin
3. Milli-inch mil is commonly known as Mille. This translates to 1mil=25.4um
Three, coating thickness calculation formula:
1. Theoretical calculation formula: Q=I×TI=J×S
Q: represents electric quantity, reflected on PCB is coating thickness;
I: indicates the current used in electroplating, in A(ampere);
T: indicates the time required for electroplating, expressed in min(minute);
J: Electroplating density, which refers to the number of amperes of current passing through the unit area per square foot, expressed in ASF(A/Ft2);
S: indicates the plated area, expressed in Ft2(square feet).
2. Calculation formula: [Note :1um=39.37 microinches (μ")=0.03937 milliinches (mil)]
(1), copper plating thickness (um) = current density (ASF) * electroplating electroplating time (min) efficiency (%) x 0.0202 (electroplating coefficient)
(2), nickel plating thickness (um) = current density (ASF) * electroplating electroplating time (min) efficiency (%) x 0.0182 (electroplating coefficient)
(3), tin plating thickness (um) = current density (ASF) * electroplating electroplating time (min) efficiency (%) x 0.0456 (electroplating coefficient)
Iv. Calculation method of electroplating cost:
Plating cost = area (CM2) (CM) x x thickness metal density (g/CM3) * (1 + out of the attrition rate (%)] x metal unit price (RMB/g)
Example 1: Electroplating Costing [Thickness 3 microinches (μ")]
A, calculate the gold-plated area: S=1.0dm2=100CM2
Then: 3μ"=(1÷39.37)×3=0.0762(um)=0.00000762(cm)
Gold salt unit price: 220 yuan /g
Gold density: 19.3g/CM3
B, gold-plated cost = [gilded area (CM2) * gold plating thickness (CM) density (g/CM3)] present gold salt content * gold salts unit price (RMB/g) * (1 + (%)] out of the loss
= [100 (CM2) x 0.00000762 (CM) x 19.3 (g/CM3)] present 68.3% by 220 (RMB) x (1 + 10%) = 5.20 yuan
How to maintain the stability of PCB chemical copper solution?
In the manufacturing technology of PCB circuit board, chemical copper deposition is widely used in plastic electroplating because of its low cost, simple operation and no need for heating. However, chemical copper deposition skills have the disadvantages of poor stability and low accumulation speed, so how to adhere to the stability of chemical copper deposition is an important problem. The reaction of chemical copper deposition using formaldehyde as rehabilitation agent is not only carried out on the non-metallic surface after activation, but also can be carried out in the solution itself. When a certain amount of reaction product copper powder is generated, the reaction is catalyzed and sensitive, which will soon make the chemical copper completely ineffective. In order to control the rehabilitation response of the solution itself, pcb manufacturers can usually choose the following methods:
(1) Increase the stability of copper ion complex, appropriately improve the complex concentration or use strong complexing agents, such as adding EDTA, tetraethylenepentamine, triethylenetetramine, etc.
(2) Add stabilizer, such as adding disulfide compounds, sodium thiosulfate, etc.
(3) Continuous filtration solution. The occurrence of autocatalysis can be prevented by continuous filtration to remove solid metal impurities from the solution.
(4) Reduce the load.
(5) air stirring. Stirring can not only increase the deposition rate, but also control the reduction reaction of copper in solution.
The method to make electroless copper plating stable and improve the deposition rate are often contradictory, so the stability should be the main, and then improve the speed, otherwise, the gain is not worth the loss.