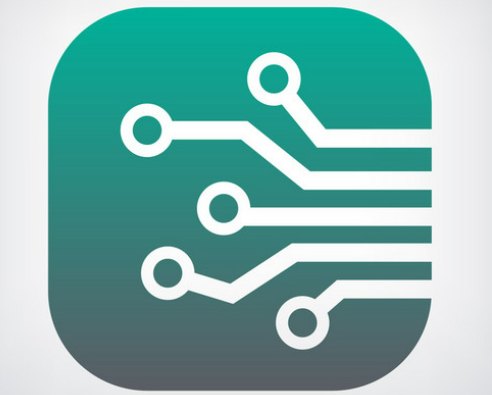
With the development of electronic products towards miniaturization and thinness, surface mounting technology (SMT)SMT patch processing emerges as The Times require and has become the mainstream of electronic production. In this chapter, we will introduce SMT patch processing process, installation components and production equipment, SMT circuit boardrepair, and introduce the application of microassembly technology (MPT).
SMT is a fourth-generation technology for mounting electronic products that integrates surface electronic components, assembly equipment, auxiliary materials and welding methods.
First, surface mount technology (SMT) development
Surface mounting technology has experienced the following four stages of development from its emergence to the present:
The primary technical objective of the first phase (1970-1985) was the application of miniaturized chip components in hybrid circuits.
The second stage (1976-1985) was the stage in which surface mounting technology made electronic products develop towards multi-function and miniaturization, and at the same time promoted the development of surface mounting equipment, which laid the foundation for the development of surface mounting technology.
The third stage (1986-1995) In this stage, screen printing, reflow welding technology was applied, product cost decreased, cost-effective improvement.
The fourth stage (1996-present) mass production of large-capacity, multifunctional, highly reliable, multi-layer and three-dimensional micro-chip components, with higher automation and faster production equipment. Welding towards the development of lead-free environmental protection, reverse welding, special welding began to use.
Two, surface mount technology (SMT) characteristics
1. Realize miniaturization on the electrodes of SMT components, some welding ends have no leads at all, and some only have very short leads; The distance between adjacent electrodes is much smaller than the lead spacing (2.54mm) of the traditional dual-in-line integrated circuit, and the minimum pin center spacing has reached 0.3mm. With the same degree of integration, SMT components are 60% to 90% smaller in volume and 60% to 90% less weight than traditional THT components.
2. Electrical performance greatly improved surface assembly components reduce parasitic leads and conductor inductance, while improving the characteristics of capacitors, resistors and other components. The transmission delay is small, the signal transmission speed is accelerated, and the radio frequency interference is eliminated at the same time, so that the high frequency characteristics of the circuit is better, the working speed is faster, the noise is significantly reduced.
3. Easy to achieve automation, mass production, high efficiency because of the standardization, serialization of chip element appearance, and consistency of welding conditions, and because of the continuous birth of advanced high-speed SMT machine, surface installation of a high degree of automation, production efficiency is greatly improved. For example, advanced technologies such as "laser alignment" and "in-flight alignment detection" are widely used in all kinds of new SMT machines.
4. Material cost and production cost are generally reduced. As the volume of SMT components is generally reduced, the packaging material consumption of components is reduced. And in SMT assembly, components do not need to be pre-shaped, cut feet, printed circuit boards do not need to punch holes, greatly saving manpower and material resources, so the production cost is generally reduced. For example, Datang Telecom company production of program control telephone switching equipment, after the adoption of SMT technology, the production cost of each "line" of the switch is reduced by 40 yuan.
5. Product quality improvement Due to the small size and strong function of chip integrated circuit, one chip integrated circuit can realize the functions of several THT circuits on the SMT circuit board, so the probability of failure of the circuit board is greatly reduced, and the work is more reliable and stable.
The reason of tin not full on SMT patch processing is discussed
In SMT patch processing, soldering tin is an important link, which is related to the performance and appearance of the circuit board. In actual production and processing, some reasons will lead to bad tin, such as the common solder joint is not full, which will directly affect the quality of SMT patch processing. Then what is the reason why the tin is not full on SMT patch processing?
The main reasons for solder joints not full on SMT patch processing are as follows:
1. The wettability of flux in solder paste is not good, and it can not meet the requirements of good tin;
2. The activity of flux in solder paste is not enough to complete the removal of oxidized substances in PCB pad or SMD welding site;
3, the flux flux expansion rate in the solder paste is too high, easy to appear empty;
4, PCB pad or SMD welding position has serious oxidation phenomenon, affecting the tinning effect;
5. The amount of solder paste in the welding spot is not enough, leading to the tin is not full and there is a vacancy;
6. If some solder joints are not full of tin, the reason may be that the solder paste is not fully stirred before use, and the flux and tin powder can not be fully integrated;
7. In over-reflow welding, the preheating time is too long or the preheating temperature is too high, resulting in the failure of flux activity in the solder paste;
When the tin is not full in SMT patch processing, the staff of SMT patch processing factory can analyze and check according to the above points, and solve the problem of tin is not full, so as to avoid scrap and increase the cost.