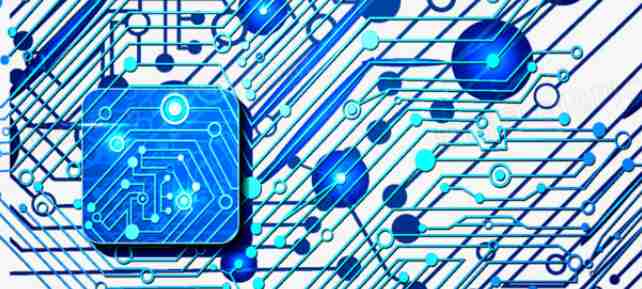
In order to ensure the normal process of SMT patch processing, we must strengthen the quality check of each process, and then monitor its operation status. Therefore, it is particularly important to set up quality control points after some key processes, so as to timely discover the quality of the previous process and correct, the root is not qualified products into the next process. The setting of quality control points is related to the production process. We can set the following quality control points in the processing process:
1. Check PCB incoming materials. Whether the welding plate is oxidized, the printed board is deformed, the printed board is scratched; Inspection method: Visual inspection according to the inspection specification.
2, plug-in view. Whether there are wrong parts; There are no leaking parts; The cartridge state of the component; Inspection method: Visual inspection according to the inspection specification.
3, solder paste print check. Thickness can be uniform, there is no bridge, there is no collapse, printing can be thorough, printing error; Inspection method: According to the inspection specification visual inspection or inspection with a magnifying glass.
4. Check the patch before reflow welding furnace after processing. There is no missing piece; Whether there is displacement; Whether there are wrong parts; Mounting orientation of components; Inspection method: According to the inspection specification visual inspection or inspection with a magnifying glass.
5. Check after reflow welding furnace. Component welding condition, there is no bridge, standing tablet, dislocation, solder ball, welding and other bad welding appearance, solder joint condition. Inspection method: According to the inspection specification visual inspection or inspection with a magnifying glass.
Brief introduction to SMT dispensing process and technical requirements
I. SMT Patch processing glue and its technical requirements:
The glue used in SMT is mainly used in the wave soldering process of chip components, SOTs, SOics and other surface mounted devices. The purpose of using glue to fix the surface mounted components on the PCB is to avoid the removal or displacement of the components which may be caused by the impact of high temperature crest. The general production of epoxy resin thermal curing glue, rather than acrylic acid glue (UV irradiation curing).
2. Requirements for SMT glue:
1. Glue should have good thixotropic characteristics;
2. No wire drawing;
3. High wet strength;
4. No bubbles;
5. Low curing temperature and short curing time of glue;
6. Sufficient curing strength;
7. Low hygroscopicity;
8. Good repair characteristics;
9. No toxicity;
10 color is easy to identify, easy to check the quality of the glue point;
11. Packing. The packaging type shall be convenient for the use of the equipment.
Three, in the process of dispensing process control plays a very important role.
The following process defects are likely to occur in the production: unqualified glue point size, wire drawing, glue dye pad, poor curing strength and easy to fall off pieces. To solve these problems, we should study the technical parameters as a whole, so as to find the solution to the problem.
1. The size of the dispensing amount
According to work experience, the size of the glue point diameter should be half of the pad spacing, and the glue point diameter should be 1.5 times of the glue point diameter after the patch. This ensures that there is plenty of glue to bond the components and avoids overwetting the pad with glue. The amount of glue is determined by the length of rotation time of the screw pump. In practice, the rotation time of the pump should be selected according to the production situation (room temperature, glue viscosity, etc.).
2. Dispensing pressure (back pressure)
At present, the dispensing machine uses a screw pump to supply the dispensing needle hose to take a pressure to ensure that enough glue to supply the screw pump. Back pressure is too large easy to cause glue overflow, glue amount is too much; If the pressure is too small, there will be intermittent phenomenon of dispensing, leakage point, resulting in defects. The pressure should be selected according to the glue of the same quality and the temperature of the working environment. High ambient temperature will make the glue viscosity smaller, better liquidity, then need to lower the back pressure to ensure the supply of glue, and vice versa.
3. The size of a pinhead
In practice, the inner diameter of the needle should be 1/2 of the diameter of the dispensing point. In the dispensing process, the dispensing needle should be selected according to the size of the welding pad on the PCB: If the size of the pads of 0805 and 1206 is not very different, the same needle can be selected, but different needles should be selected for the pads with a big difference, which can not only ensure the quality of the glue point, but also improve production efficiency.
4. Distance between needle and PCB board
Different dispensing machines use different needles, some needles have A certain degree of stop (such as CAM/A LOT 5000). Calibration of the distance between the needle and PCB should be done at the beginning of each work, that is, Z-axis height calibration.