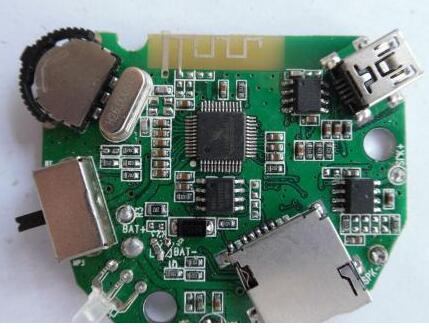
kingford is a PCBA manufacturer with its own SMT plant, providing one-stop service from PCB design, PCB manufacturing, SMT patch processing, DIP plug-in processing to finished product assembly and testing. We have rich SMT SMT processing experience, the next to introduce SMT processing how to solve the solder joint stripping problem. Reasons for solder joint stripping in SMT patch processing The problem of solder joint stripping sometimes occurs in through-hole wave soldering, and also in SMT reflow welding.
This phenomenon is that there is a fault between the solder joint and the pad, and stripping occurs. The main reason for this phenomenon is that the coefficient of thermal expansion between the lead-free alloy and the substrate is different, which leads to excessive stress on the stripped parts during the solidification process and causes them to separate. The non-eutectic properties of some solder alloys also contribute to this phenomenon. SMT patch processing to solve the solder joint stripping method There are two ways to solve this PCBA problem. One is to choose the appropriate solder alloy; The other is to choose the appropriate solder alloy.
The second is to control the cooling speed, so that the solder joint solidification as soon as possible, forming a strong binding force. In addition to these methods, PCB designs can also be used to reduce stress amplitude, i.e. the area of the copper ring through the hole. In Japan, a popular practice is to use SMD pads, which limit the area of the copper ring by using a green oil-proof layer. But this approach has two drawbacks. One is that the lighter peel is not easy to see.
Secondly, an SMD pad is formed at the interface between the source oil and the pad, which is not ideal from the point of view of service life. Some tearing occurs in the solder joint and is called tearing or tearing. Some suppliers in the industry believe this problem is acceptable if it occurs at the top through the solder joint. Mainly because the key part of the through-hole mass is not there. However, if it occurs in reflow solder joints, it should be treated as a quality problem unless the extent is small (similar to wrinkles)
How to solve the SMT solder paste problem
kingford has its own SMT SMT plant, which is equipped with Fujifilm high-speed SMT assembly line, AOI optical detector, automatic solder paste printing machine and other advanced processing equipment, and can provide SMT SMT processing services of minimum package 0201 components. Next, we will introduce how to solve the problem of SMT welding paste printing.
SMT common solder paste printing problems and solutions
1. The reason for pulling the tip: most of these problems are caused by too large a gap of the scraper or too large a viscosity of the solder paste. Solution: Determine the cause. If the gap of the scraper is too large, adjust the gap of the small scraper to the appropriate position during SMT processing. If the viscosity of the solder paste is too large, the SMT factory will need to select the solder paste with the appropriate viscosity during processing.
2. Reasons for too thin solder paste: Generally, there are three possible reasons for too thin solder paste in SMT processing:
(1) the template is too thin; (2) the scraper pressure is too large; (3) poor fluidity of solder paste can not meet the requirements. Solution: First determine the reason why solder paste is too thin in SMT patch processing, and then solve the problem. If the template is too thin, replace it with a suitable thickness. If the scraper pressure is too large, adjust the scraper pressure appropriately; The fluidity of the solder paste is generally related to the particle size and viscosity of the solder paste, and the appropriate solder paste can be selected.
3. Reasons for the uneven thickness of the solder paste on the pad: There are generally two reasons for the uneven thickness of the solder paste on the pad:
1. Uneven mixing of welding paste; 2. The template is not parallel to the printed board. Solution: Determine the cause of the problem and then solve the problem according to the cause. Mix the solder paste fully before printing so that the particle size of the solder paste is unified; Adjust the orientation of the template relative to the printed board so that it is parallel.
4, the thickness is different, the edge and the appearance of burr cause: most of it is caused by the viscosity of the solder paste is too low or the template hole wall is rough. Solution: Re-select solder paste with higher viscosity, and carefully check the quality of etching process before SMT factory processing.
5. Causes of subsidence: there are generally three causes of subsidence:
(1) The printing board positioning is not stable enough; (2) the pressure of the scraper is too large; (3) the viscosity of welding paste is too low or the metal content of welding paste is too low. Solution: Determine the cause of the collapse in SMT processing, and then take the corresponding solution according to the cause: (1) re-fix the printed board and keep it stable; (2) Adjust the pressure of the scraper to an appropriate degree; (3) Select the solder paste again to make the viscosity or metal content of the solder paste meet the requirements of SMT patch processing solder paste printing.
6, printing is not complete cause: there are many reasons, the common is generally the following four:
(1) The opening is blocked or the solder paste is stuck to the bottom of the template; (2) insufficient viscosity of solder paste; (3) There are large metal powder particles in the solder paste; (4) Scraper wear.
Solution: According to different causes to adopt the corresponding solution:
(1) Clean the holes and the bottom of the template; (2) re-select the appropriate solder paste; (3) re-select the solder paste, so that the selected metal powder particle size and hole size match; (4) Replace the scraper.