Building 6, Zone 3, Yuekang Road,Bao'an District, Shenzhen, China
+86-13923401642Mon.-Sat.08:00-20:00
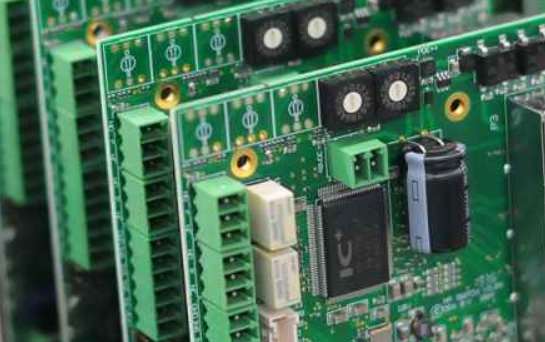
PCBA lead-free solder joint and SMT testing equipment
Reliability test PCBA lead-free solder joint
PCBA lead-free solder joint reliability test is mainly to conduct thermal load test (temperature impact or temperature loop test) on electronic assembly products; According to the fatigue life test conditions, the mechanical stress test is carried out on the electronic equipment joints; Use the model for life assessment. The reliability testing methods of PCBA lead-free solder joints mainly include visual inspection, X-ray inspection, metallographic section analysis, strength (tensile, shear), fatigue life, high temperature and humidity, drop test, random vibration and reliability testing methods. Here are some of them:
1. Visual inspection
Lead free and lead-free PCBA solder joints are different from the outside, which will affect the correctness of AOI system. The stripe of PCBA lead-free solder joint is more obvious and rougher than the corresponding lead solder joint, which is caused by the phase transition from liquid to solid. This type of solder joint looks rougher and uneven. In addition, because of the high surface tension of lead-free solder in PCBA processing, it is not as easy to flow as lead solder, and the fillets formed are also different.
2. X-ray inspection
In the spherical solder joints of PCBA lead-free welding, the number of virtual welding is increased. PCBA lead-free solder has high welding density, which can detect cracks and faulty soldering during welding.
Copper, tin and silver should be classified as "high density" data In order to characterize the characteristics of excellent welding, it is necessary to recalibrate the X-ray system Test equipment has higher requirements
3. Metallographic section analysis
Metallographic analysis is one of the important methods for experimental research of metal materials. In the reliability analysis of PCBA solder joints, the metallographic structure of the solder joint contour is often observed and analyzed, which is called metallographic section analysis. Metallographic section analysis is a destructive examination. The sample production cycle is long and the cost is high. It is usually used for analysis after solder joint failure, but it has the advantages of intuition and seeking truth from facts.
4. Automatic solder joint reliability detection technology
Automatic solder joint reliability detection technology is an advanced technology that uses photothermal method to detect the solder joint quality of circuit boards point by point. It has the characteristics of high detection accuracy, good reliability, and no need to touch or damage the solder joint to be tested during the test. During the inspection, a certain amount of laser energy is injected into the solder joints of PCBA board point by point, and the infrared detector is used to monitor the thermal radiation generated after the solder joints are irradiated by laser. Since the thermal radiation characteristics are related to the quality of solder joints, the quality of solder joints can be judged accordingly.
5. Conduct temperature related fatigue test
In the reliability test of PCBA lead-free solder joints, it is more important to conduct temperature related fatigue tests for different thermal expansion coefficients of solder joints and connecting parts, including isothermal mechanical fatigue test and thermal fatigue test.
When evaluating the reliability of PCBA lead-free solder joints, the most important point is to select the most relevant test methods and clearly determine the test parameters of specific methods. In the reliability test of PCBA lead-free solder joints, it is more important to carry out temperature related fatigue tests for different thermal expansion coefficients of solder joints and connecting parts, including isothermal mechanical fatigue test, thermal fatigue test and corrosion resistance test. According to the test results, it can be confirmed that different lead-free materials have different resistance to mechanical stress at the same temperature. At the same time, research shows that different lead-free data show different failure mechanisms and failure modes.
Common test equipment and functions in SMT chip processing
The chip processing process is complex and complicated, and problems may occur in each link. In order to ensure that the product quality is qualified, it is necessary to use various test equipment to detect faults and defects and solve problems in time. So, what is the common test equipment in SMT chip processing? What is its function?
1. MVI (manual visual inspection)
2. AOI test equipment
(1) Where AOI inspection equipment is used: AOI can be used at multiple locations on the production line, and each location can detect special defects, but AOI inspection equipment should be placed at a location where most defects can be identified and corrected as soon as possible.
(2) Defects that AOI can detect: AOI usually checks after PCB etching, mainly to find missing and redundant parts.
3. X-ray detector
(1) Where the X-ray detector is used: it can detect all solder joints on the circuit board, including those invisible to the naked eye, such as BGA.
(2) Defects that can be detected by X-ray detector: defects that can be detected by X-ray detector are mainly defects such as bridge after welding, cavity, too many welding spots, too small welding spots, etc.
4. ICT test equipment
(1) Where to use ICT: ICT is oriented to production process control and can measure resistance, capacitance, inductance and integrated circuit. It is particularly effective in detecting open circuit, short circuit, component damage, etc., with accurate fault location and convenient maintenance.
(2) ICT can detect defects: it can test problems such as virtual welding, open circuit, short circuit, component failure and incorrect data after welding.
In addition, to the use of these testing equipment, quality assurance SMT chip processing can not be separated from the strict quality control and monitoring of chip manufacturers
Reliability test PCBA lead-free solder joint
PCBA lead-free solder joint reliability test is mainly to conduct thermal load test (temperature impact or temperature loop test) on electronic assembly products; According to the fatigue life test conditions, the mechanical stress test is carried out on the electronic equipment joints; Use the model for life assessment. The reliability testing methods of PCBA lead-free solder joints mainly include visual inspection, X-ray inspection, metallographic section analysis, strength (tensile, shear), fatigue life, high temperature and humidity, drop test, random vibration and reliability testing methods. Here are some of them:
1. Visual inspection
Lead free and lead-free PCBA solder joints are different from the outside, which will affect the correctness of AOI system. The stripe of PCBA lead-free solder joint is more obvious and rougher than the corresponding lead solder joint, which is caused by the phase transition from liquid to solid. This type of solder joint looks rougher and uneven. In addition, because of the high surface tension of lead-free solder in PCBA processing, it is not as easy to flow as lead solder, and the fillets formed are also different.
2. X-ray inspection
In the spherical solder joints of PCBA lead-free welding, the number of virtual welding is increased. PCBA lead-free solder has high welding density, which can detect cracks and faulty soldering during welding.
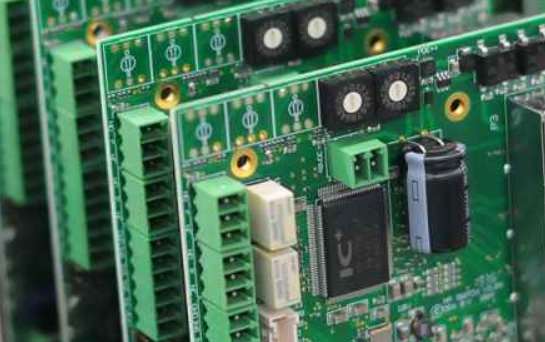
3. Metallographic section analysis
Metallographic analysis is one of the important methods for experimental research of metal materials. In the reliability analysis of PCBA solder joints, the metallographic structure of the solder joint contour is often observed and analyzed, which is called metallographic section analysis. Metallographic section analysis is a destructive examination. The sample production cycle is long and the cost is high. It is usually used for analysis after solder joint failure, but it has the advantages of intuition and seeking truth from facts.
4. Automatic solder joint reliability detection technology
Automatic solder joint reliability detection technology is an advanced technology that uses photothermal method to detect the solder joint quality of circuit boards point by point. It has the characteristics of high detection accuracy, good reliability, and no need to touch or damage the solder joint to be tested during the test. During the inspection, a certain amount of laser energy is injected into the solder joints of PCBA board point by point, and the infrared detector is used to monitor the thermal radiation generated after the solder joints are irradiated by laser. Since the thermal radiation characteristics are related to the quality of solder joints, the quality of solder joints can be judged accordingly.
5. Conduct temperature related fatigue test
In the reliability test of PCBA lead-free solder joints, it is more important to conduct temperature related fatigue tests for different thermal expansion coefficients of solder joints and connecting parts, including isothermal mechanical fatigue test and thermal fatigue test.
When evaluating the reliability of PCBA lead-free solder joints, the most important point is to select the most relevant test methods and clearly determine the test parameters of specific methods. In the reliability test of PCBA lead-free solder joints, it is more important to carry out temperature related fatigue tests for different thermal expansion coefficients of solder joints and connecting parts, including isothermal mechanical fatigue test, thermal fatigue test and corrosion resistance test. According to the test results, it can be confirmed that different lead-free materials have different resistance to mechanical stress at the same temperature. At the same time, research shows that different lead-free data show different failure mechanisms and failure modes.
Common test equipment and functions in SMT chip processing
The chip processing process is complex and complicated, and problems may occur in each link. In order to ensure that the product quality is qualified, it is necessary to use various test equipment to detect faults and defects and solve problems in time. So, what is the common test equipment in SMT chip processing? What is its function?
1. MVI (manual visual inspection)
2. AOI test equipment
(1) Where AOI inspection equipment is used: AOI can be used at multiple locations on the production line, and each location can detect special defects, but AOI inspection equipment should be placed at a location where most defects can be identified and corrected as soon as possible.
(2) Defects that AOI can detect: AOI usually checks after PCB etching, mainly to find missing and redundant parts.
3. X-ray detector
(1) Where the X-ray detector is used: it can detect all solder joints on the circuit board, including those invisible to the naked eye, such as BGA.
(2) Defects that can be detected by X-ray detector: defects that can be detected by X-ray detector are mainly defects such as bridge after welding, cavity, too many welding spots, too small welding spots, etc.
4. ICT test equipment
(1) Where to use ICT: ICT is oriented to production process control and can measure resistance, capacitance, inductance and integrated circuit. It is particularly effective in detecting open circuit, short circuit, component damage, etc., with accurate fault location and convenient maintenance.
(2) ICT can detect defects: it can test problems such as virtual welding, open circuit, short circuit, component failure and incorrect data after welding.
In addition, to the use of these testing equipment, quality assurance SMT chip processing can not be separated from the strict quality control and monitoring of chip manufacturers
Just upload Gerber files, BOM files and design files, and the KINGFORD team will provide a complete quotation within 24h.