Building 6, Zone 3, Yuekang Road,Bao'an District, Shenzhen, China
+86-13923401642Mon.-Sat.08:00-20:00
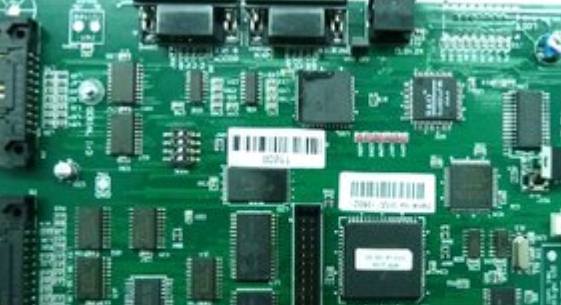
About SMT reflow welding process setting
At the beginning of this article, I mentioned that many users process reflow soldering on SMT chips Here are some common problems and mistakes Readers may want to know if these problems exist
1. Accurately set the furnace temperature according to the quota of the temperature curve provided by the solder paste supplier
At present, most users only use the information provided by the solder paste supplier as the basis for setting the welding temperature. This raises two questions. First of all, the curve proposed by the solder paste supplier only considers the solderability of the solder paste, and it is impossible to know other requirements of users for PCBs. This curve can only be used as a reference, not a standard. Especially for the temperature and time of the welding area, the user's consideration is usually not solder paste. In addition, solder paste suppliers are often not very accurate in the characteristics of the constant temperature zone, which is related to the characteristics of the solder paste supply industry. It is impossible to optimize the user's welding process settings.
2. The concept of "process window" is missing
In engineering projects, we very much avoid the lack of the concepts of "window", "upper and lower limits" and "tolerance". Because this will make us ignore and unable to optimize and control our technological characteristic parameters. The same is true of the reflow process.
3. Wrong judgment of hot and cold spots
When using the travel window, it is appropriate to ensure that PCBs are in this window In practical work, we cannot measure every solder joint Therefore, the key point of reflow welding process setting is how to confirm the coldest and hottest PCBs on the welding surface When we can meet these two requirements through process adjustment, other solder joints will naturally occur at the same time In traditional practice, the user usually determines the setting position of the temperature measurement thermocouple by observing the size of the device This is a very old practice In the past, infrared welding technology may be somewhat reliable, But its reliability in hot air welding is very low If the reader has ever seen a small rectangular part, such as 0603, with a temperature difference of up to 8 degrees at both ends, or 13 degrees around the QFP pin, or when the same device has a temperature difference of up to 20 degrees at the solder joints in different circuits, you will believe that this observation and prediction method is absolutely unacceptable
4. Not clear
When setting and adjusting the welding process, we may encounter products that are difficult to design. Due to the selection and layout of components on the circuit board, the thermal capacity of these products may vary greatly. If the capacity of the reflow furnace used is not very strong, or the resistance of the solder paste used to the welding window is not very strong, the quality of all solder joints may not be considered in the process modulation. In this case, we must balance the quality of the solder joint. Due to the lack of DFM/DFR (Design for Manufacturability/Reliability Design), or the lack of understanding of the life requirements of each data/solder joint on the product by the production department, many users cannot make effective choices. Many users are completely unaware of this process modulation and optimization method.
5. Misunderstanding five processes into one process
As mentioned earlier in this paper, SMT wafer processing reflow soldering actually includes five processes, including heating, constant temperature, welding, welding, and cooling If this important link is ignored, it may lead to confusion or wrong decisions for us to solve process problems For example, solder ball problems may occur during heating, constant temperature, or improper welding process, but the reasons are different Welding ball problems caused by heating process are mainly caused by gas explosion, most of which are related to data quality, inventory time and conditions, and solder paste printing process (Note 3) However, if it is caused by constant temperature process, it is mainly related to improper temperature/time setting or deterioration of solder paste Related to the welding process, it is caused by high oxidation and improper temperature/time setting In each case, the appearance of the solder ball is different, and the treatment method is also different If it is not analyzed as different processes and mechanisms, only SMT equipment can be adjusted without selection or blind attempt
At the beginning of this article, I mentioned that many users process reflow soldering on SMT chips Here are some common problems and mistakes Readers may want to know if these problems exist
1. Accurately set the furnace temperature according to the quota of the temperature curve provided by the solder paste supplier
At present, most users only use the information provided by the solder paste supplier as the basis for setting the welding temperature. This raises two questions. First of all, the curve proposed by the solder paste supplier only considers the solderability of the solder paste, and it is impossible to know other requirements of users for PCBs. This curve can only be used as a reference, not a standard. Especially for the temperature and time of the welding area, the user's consideration is usually not solder paste. In addition, solder paste suppliers are often not very accurate in the characteristics of the constant temperature zone, which is related to the characteristics of the solder paste supply industry. It is impossible to optimize the user's welding process settings.
2. The concept of "process window" is missing
In engineering projects, we very much avoid the lack of the concepts of "window", "upper and lower limits" and "tolerance". Because this will make us ignore and unable to optimize and control our technological characteristic parameters. The same is true of the reflow process.
3. Wrong judgment of hot and cold spots
When using the travel window, it is appropriate to ensure that PCBs are in this window In practical work, we cannot measure every solder joint Therefore, the key point of reflow welding process setting is how to confirm the coldest and hottest PCBs on the welding surface When we can meet these two requirements through process adjustment, other solder joints will naturally occur at the same time In traditional practice, the user usually determines the setting position of the temperature measurement thermocouple by observing the size of the device This is a very old practice In the past, infrared welding technology may be somewhat reliable, But its reliability in hot air welding is very low If the reader has ever seen a small rectangular part, such as 0603, with a temperature difference of up to 8 degrees at both ends, or 13 degrees around the QFP pin, or when the same device has a temperature difference of up to 20 degrees at the solder joints in different circuits, you will believe that this observation and prediction method is absolutely unacceptable
4. Not clear
When setting and adjusting the welding process, we may encounter products that are difficult to design. Due to the selection and layout of components on the circuit board, the thermal capacity of these products may vary greatly. If the capacity of the reflow furnace used is not very strong, or the resistance of the solder paste used to the welding window is not very strong, the quality of all solder joints may not be considered in the process modulation. In this case, we must balance the quality of the solder joint. Due to the lack of DFM/DFR (Design for Manufacturability/Reliability Design), or the lack of understanding of the life requirements of each data/solder joint on the product by the production department, many users cannot make effective choices. Many users are completely unaware of this process modulation and optimization method.
5. Misunderstanding five processes into one process
As mentioned earlier in this paper, SMT wafer processing reflow soldering actually includes five processes, including heating, constant temperature, welding, welding, and cooling If this important link is ignored, it may lead to confusion or wrong decisions for us to solve process problems For example, solder ball problems may occur during heating, constant temperature, or improper welding process, but the reasons are different Welding ball problems caused by heating process are mainly caused by gas explosion, most of which are related to data quality, inventory time and conditions, and solder paste printing process (Note 3) However, if it is caused by constant temperature process, it is mainly related to improper temperature/time setting or deterioration of solder paste Related to the welding process, it is caused by high oxidation and improper temperature/time setting In each case, the appearance of the solder ball is different, and the treatment method is also different If it is not analyzed as different processes and mechanisms, only SMT equipment can be adjusted without selection or blind attempt
Just upload Gerber files, BOM files and design files, and the KINGFORD team will provide a complete quotation within 24h.