Building 6, Zone 3, Yuekang Road,Bao'an District, Shenzhen, China
+86-13923401642Mon.-Sat.08:00-20:00
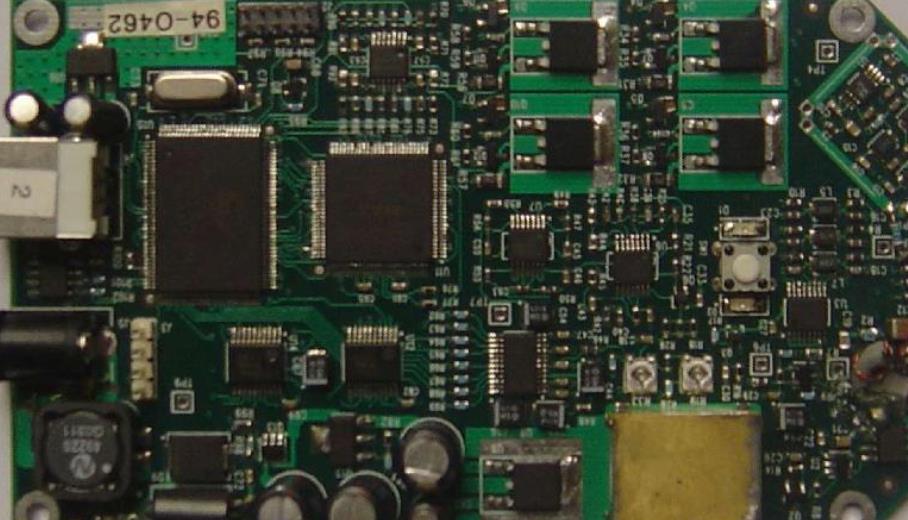
For PCB, PCBA processability review content
Polychlorinated biphenyls processability review
1. Selection of components. Weldability. Heat resistance. Coplanarity.
In the PCB design, chip modules shall be used as much as possible, and the duty cycle of chip modules shall be more than 95%
2. Selection of PCB substrate. Weldability. Heat resistance. planeness.
3. PCB design rules.
Conductive pattern layout and wiring.
Design requirements for pad design and component spacing.
The size of printed wire, pad and metallized hole (insertion hole, relay hole) and the safe distance between them.
Electromagnetic compatibility.
Heat conduction and heat dissipation.
PCB surface coating.
Solder mask graphics.
Machinability.
Detectability.
4. Prohibited and restricted design and process requirements.
5. Component installation.
6. Requirements for special components.
7. Member reinforcement and three prevention requirements.
PCB and PCB pattern design process review
1.PCB。
According to the requirements of GJB 3243-1998, SJ/T 10670-1995 and IPC-SM-7351B-2010, the same pad shall not be shared between surface mounted components, between surface mounted components and through hole insertion components, and between surface mounted components and wires.
The name, drawing number, bit number, model, specification, etc. of the PCB design file are identical with the actual product: the diameter of the metallized hole should be greater than the lead diameter of the component or the outer diameter of the wire core. 2~0.3mm. The relationship between the wire diameter, the diameter of the metallized hole and the diameter of the pad is shown in the following table. Or install components and chip components on the tin coating for grounding and heat dissipation. The non mounting welding area on the printed circuit board surface must have a welding mask, and there must be no fusible metal under the welding mask.
Resistance welding coating requirements.
Surface coating requirements for printed wires and pads.
When the printed circuit board needs to pass large current, the width of the printed circuit can be widened by using external wires or using thicker copper and platinum substrates.
2. Polychlorinated biphenyls.
The overall dimensions and installation and fixing methods of printed circuit boards shall match the reserved positions and fixing methods of structural members.
Elements, especially high-density integrated circuit layout (density, installation space and adjacent spacing) and reinforcement measures.
Heat conduction and heat dissipation measures, reinforcement measures and installation space.
Rationality, stability and safety distance of component installation.
Polychlorinated biphenyls (PCBs) are resistant to warping, mechanical environment reinforcement and environmental erosion
Installation requirements for terminals and wires.
Maintainability and enforceability.
3. Scientific and technical requirements for printed circuit board assembly drawing.
Assemble and weld according to QJ165B.
The installation height of the assembly (the distance between the top of the assembly and the PCB surface) and the special molding requirements of the assembly.
Components that are not installed, shorted, or connected.
Requirements for components equipped with sockets.
Describes the code, name, and model of the anti-static component.
Parts with a mass greater than 14g shall be marked with reinforcement bonding requirements.
Fixing point and method of jumper wire. High temperature components that may cause short circuits (such as metal film resistors and wire wound resistors above 1W) shall not be installed on the circuit board.
Cross mounting of transistor pins is not allowed.
Three verification requirements for printed circuit boards.
4. Except for high-frequency microwave circuits, overlapping wires are not allowed on the printed circuit board, and overlapping installation mode is not allowed for plug-in components, that is, separate R, C, L, IC, G and other components are overlapped and installed on the bonding pad, printed wires and component leads of the printed circuit board.
5. Jumper wire on the printed circuit board.
Normally, jumper wires are not required on the printed circuit board. If it is necessary to use, the number of jumper wires allowed in principle shall not exceed two: if the number of jumper wires exceeds two due to the discreteness of components, it shall be approved by the chief engineer of the project.
The jumper wire should be as short as possible.
The wiring must not prevent the replacement of components or other jumper wires.
The jumper shall have a fixed point every 25 mm at most.
The jumper wire shall be considered as an axial lead component and shall meet the detailed requirements for the installation of axial lead components.
The jumper wire shall not pass through the upper or lower part of other components, including the jumper wire.
When the length of the jumper wire is less than 12.5 mm, and its wiring does not pass through the conductive area and meets the requirements of power spacing, bare silver plated copper wire can be used.
Jumper wire in "Repair and modification of printed circuit board assembly".
A. A maximum of two jumper wires can be connected to any spare part pad.
B. The jumper wire shall be routed along the X-Y axis, and there shall be no twist or crack on the wire.
C. Jumpers shall be as short as possible and shall not be routed above or below components.
D. The length of the jumper wire contact shall not be less than 1/2 of the length or height of the metallized terminal of the component (see Appendix A of SJ 20632-1997).
E. If you weld multiple jumper wires to one end, you can wrap the uninsulated parts of the wires together and then weld them.
F. The jumper wire shall be firmly fixed at the place where it needs to be positioned with adhesive, and the adhesive must be fused with the conformal coating.
Only one element lead or one wire is allowed to be welded to each metallized hole.
The surface mounted components must match the bonding pads on the printed circuit board and meet the requirements of GJB 3243-1998, SJ/T 10670-1995 and IPC-SM-7351B-2010.
The printed circuit board shall adopt nickel plating process or hot air leveling process (SMOBC), which shall be indicated on the assembly drawing.
Polychlorinated biphenyls processability review
1. Selection of components. Weldability. Heat resistance. Coplanarity.
In the PCB design, chip modules shall be used as much as possible, and the duty cycle of chip modules shall be more than 95%
2. Selection of PCB substrate. Weldability. Heat resistance. planeness.
3. PCB design rules.
Conductive pattern layout and wiring.
Design requirements for pad design and component spacing.
The size of printed wire, pad and metallized hole (insertion hole, relay hole) and the safe distance between them.
Electromagnetic compatibility.
Heat conduction and heat dissipation.
PCB surface coating.
Solder mask graphics.
Machinability.
Detectability.
4. Prohibited and restricted design and process requirements.
5. Component installation.
6. Requirements for special components.
7. Member reinforcement and three prevention requirements.
PCB and PCB pattern design process review
1.PCB。
According to the requirements of GJB 3243-1998, SJ/T 10670-1995 and IPC-SM-7351B-2010, the same pad shall not be shared between surface mounted components, between surface mounted components and through hole insertion components, and between surface mounted components and wires.
The name, drawing number, bit number, model, specification, etc. of the PCB design file are identical with the actual product: the diameter of the metallized hole should be greater than the lead diameter of the component or the outer diameter of the wire core. 2~0.3mm. The relationship between the wire diameter, the diameter of the metallized hole and the diameter of the pad is shown in the following table. Or install components and chip components on the tin coating for grounding and heat dissipation. The non mounting welding area on the printed circuit board surface must have a welding mask, and there must be no fusible metal under the welding mask.
Resistance welding coating requirements.
Surface coating requirements for printed wires and pads.
When the printed circuit board needs to pass large current, the width of the printed circuit can be widened by using external wires or using thicker copper and platinum substrates.
2. Polychlorinated biphenyls.
The overall dimensions and installation and fixing methods of printed circuit boards shall match the reserved positions and fixing methods of structural members.
Elements, especially high-density integrated circuit layout (density, installation space and adjacent spacing) and reinforcement measures.
Heat conduction and heat dissipation measures, reinforcement measures and installation space.
Rationality, stability and safety distance of component installation.
Polychlorinated biphenyls (PCBs) are resistant to warping, mechanical environment reinforcement and environmental erosion
Installation requirements for terminals and wires.
Maintainability and enforceability.
3. Scientific and technical requirements for printed circuit board assembly drawing.
Assemble and weld according to QJ165B.
The installation height of the assembly (the distance between the top of the assembly and the PCB surface) and the special molding requirements of the assembly.
Components that are not installed, shorted, or connected.
Requirements for components equipped with sockets.
Describes the code, name, and model of the anti-static component.
Parts with a mass greater than 14g shall be marked with reinforcement bonding requirements.
Fixing point and method of jumper wire. High temperature components that may cause short circuits (such as metal film resistors and wire wound resistors above 1W) shall not be installed on the circuit board.
Cross mounting of transistor pins is not allowed.
Three verification requirements for printed circuit boards.
4. Except for high-frequency microwave circuits, overlapping wires are not allowed on the printed circuit board, and overlapping installation mode is not allowed for plug-in components, that is, separate R, C, L, IC, G and other components are overlapped and installed on the bonding pad, printed wires and component leads of the printed circuit board.
5. Jumper wire on the printed circuit board.
Normally, jumper wires are not required on the printed circuit board. If it is necessary to use, the number of jumper wires allowed in principle shall not exceed two: if the number of jumper wires exceeds two due to the discreteness of components, it shall be approved by the chief engineer of the project.
The jumper wire should be as short as possible.
The wiring must not prevent the replacement of components or other jumper wires.
The jumper shall have a fixed point every 25 mm at most.
The jumper wire shall be considered as an axial lead component and shall meet the detailed requirements for the installation of axial lead components.
The jumper wire shall not pass through the upper or lower part of other components, including the jumper wire.
When the length of the jumper wire is less than 12.5 mm, and its wiring does not pass through the conductive area and meets the requirements of power spacing, bare silver plated copper wire can be used.
Jumper wire in "Repair and modification of printed circuit board assembly".
A. A maximum of two jumper wires can be connected to any spare part pad.
B. The jumper wire shall be routed along the X-Y axis, and there shall be no twist or crack on the wire.
C. Jumpers shall be as short as possible and shall not be routed above or below components.
D. The length of the jumper wire contact shall not be less than 1/2 of the length or height of the metallized terminal of the component (see Appendix A of SJ 20632-1997).
E. If you weld multiple jumper wires to one end, you can wrap the uninsulated parts of the wires together and then weld them.
F. The jumper wire shall be firmly fixed at the place where it needs to be positioned with adhesive, and the adhesive must be fused with the conformal coating.
Only one element lead or one wire is allowed to be welded to each metallized hole.
The surface mounted components must match the bonding pads on the printed circuit board and meet the requirements of GJB 3243-1998, SJ/T 10670-1995 and IPC-SM-7351B-2010.
The printed circuit board shall adopt nickel plating process or hot air leveling process (SMOBC), which shall be indicated on the assembly drawing.
Just upload Gerber files, BOM files and design files, and the KINGFORD team will provide a complete quotation within 24h.