Building 6, Zone 3, Yuekang Road,Bao'an District, Shenzhen, China
+86-13923401642Mon.-Sat.08:00-20:00
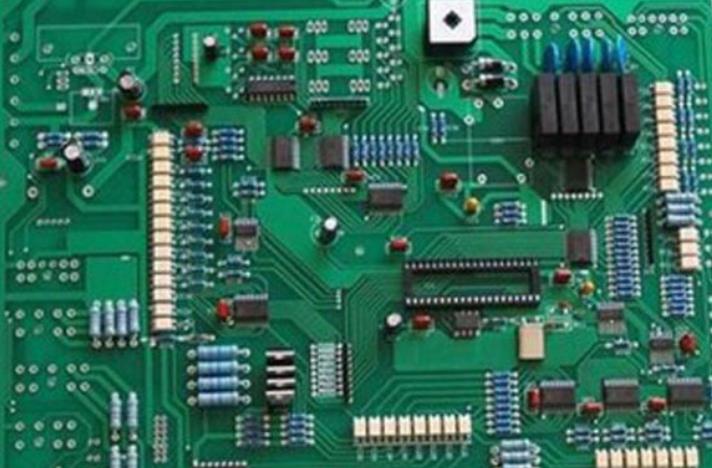
PCBA wave soldering operation and processing plant costs
In production, if you encounter a large amount of solder, then you need to choose wave soldering for processing When operating wave soldering, you should pay attention to:
The wave crest surface is covered by a layer of oxide skin, which is almost static in the whole welding wave length. During wave soldering, the PCB contacts the front surface of the tin wave, and the oxide skin is damaged. The tin wave in front of the PCB is pushed forward instead of wrinkles, which indicates that the entire oxide skin moves at the same speed as the PCB.
Generally, in order to avoid bad wave soldering, the following methods can be used: use components/PCBs with good solderability to improve the welding activity, increase the preheating temperature of the polychlorinated biphenyls, increase the wettability of the gasket, increase the temperature of the solder, remove harmful impurities, reduce the adhesion of the solder, and facilitate the separation of solder between two solder joints
How to calculate the PCBs patch processing factory?
1. PCB board fee
If you want to find a PCB processor to help you deal with it, you must provide PCB files and BOMs. The PCB processor will help you make bare PCB boards according to your PCB files. At this point, the first part of the cost, namely PCB, will be generated. The cost of cost PCB is determined by the difficulty of the board. For example, the prices of 4-layer board, 8-layer board, aluminum substrate and carbon ink board are different. Of course, you can also find a PCB factory for processing. The price is definitely not that cheap. After all, others have long-term cooperation. There must be a discount. Don't worry about the local tyrants and evil gentry.
2. Component purchase cost
The second part is the PCB patch processing cost and component procurement. The processing manufacturer purchases the components you need according to the BOM. When purchasing components, due to the load of magnetic chips (such as resistors and capacitors) and the loss of SMT patches (such as wrong boards and tapes not cleaned in time), it is necessary to cover about 5% of the data loss; The processing manufacturer has long-term cooperation with the component manufacturer, and the price will be lower.
3. SMT processing fee (patch+immersion welding)
When calculating SMT processing cost, you must first understand how large your processing batch is. If it is greater than 2000 pic, there is no need to charge the project fee, otherwise, the project fee will be charged. Next, calculate the points and multiply by the unit price of the points. The unit price of the patch point is between 0.01-0.015 yuan. The point is calculated according to the SMT patch data of 2 feet and 1 point and DIP parts of 1 foot and 1 point. Multiply the two. Refinement can be divided into:
1.0402 Parts shall be calculated at RMB 0.015 per point. 0603-1206 components are calculated at 0.015 yuan/point
2. One foot of a piece of data is a point; Calculated at 0.015 yuan/point.
3. Slot type 1 point 4 pin; Calculated at 0.015 yuan/point.
4. Ordinary integrated circuit, 4 pins for 1 point; Calculated at 0.015 yuan/point.
5. Close pin IC, 2 pins are 1 point; Calculated at 0.015 yuan/point.
1 point for 6.2 foot BGA; Calculated at 0.015 yuan/point.
7. Large machine mounted data shall be calculated by doubling the volume of components.
8. Surcharge is calculated at RMB 20 per hour
9. This quotation does not include testing fees, transportation fees, taxes, etc.
PCBs testing and assembly costs
The PCBs test fee is generally calculated at 2 yuan per board. The PCBs component and packaging costs are generally 0.8 yuan per block, which is the fourth part of the cost
Now, the total cost of the above four parts is the processing cost of PCBs patch!
In production, if you encounter a large amount of solder, then you need to choose wave soldering for processing When operating wave soldering, you should pay attention to:
The wave crest surface is covered by a layer of oxide skin, which is almost static in the whole welding wave length. During wave soldering, the PCB contacts the front surface of the tin wave, and the oxide skin is damaged. The tin wave in front of the PCB is pushed forward instead of wrinkles, which indicates that the entire oxide skin moves at the same speed as the PCB.
Generally, in order to avoid bad wave soldering, the following methods can be used: use components/PCBs with good solderability to improve the welding activity, increase the preheating temperature of the polychlorinated biphenyls, increase the wettability of the gasket, increase the temperature of the solder, remove harmful impurities, reduce the adhesion of the solder, and facilitate the separation of solder between two solder joints
How to calculate the PCBs patch processing factory?
1. PCB board fee
If you want to find a PCB processor to help you deal with it, you must provide PCB files and BOMs. The PCB processor will help you make bare PCB boards according to your PCB files. At this point, the first part of the cost, namely PCB, will be generated. The cost of cost PCB is determined by the difficulty of the board. For example, the prices of 4-layer board, 8-layer board, aluminum substrate and carbon ink board are different. Of course, you can also find a PCB factory for processing. The price is definitely not that cheap. After all, others have long-term cooperation. There must be a discount. Don't worry about the local tyrants and evil gentry.
2. Component purchase cost
The second part is the PCB patch processing cost and component procurement. The processing manufacturer purchases the components you need according to the BOM. When purchasing components, due to the load of magnetic chips (such as resistors and capacitors) and the loss of SMT patches (such as wrong boards and tapes not cleaned in time), it is necessary to cover about 5% of the data loss; The processing manufacturer has long-term cooperation with the component manufacturer, and the price will be lower.
3. SMT processing fee (patch+immersion welding)
When calculating SMT processing cost, you must first understand how large your processing batch is. If it is greater than 2000 pic, there is no need to charge the project fee, otherwise, the project fee will be charged. Next, calculate the points and multiply by the unit price of the points. The unit price of the patch point is between 0.01-0.015 yuan. The point is calculated according to the SMT patch data of 2 feet and 1 point and DIP parts of 1 foot and 1 point. Multiply the two. Refinement can be divided into:
1.0402 Parts shall be calculated at RMB 0.015 per point. 0603-1206 components are calculated at 0.015 yuan/point
2. One foot of a piece of data is a point; Calculated at 0.015 yuan/point.
3. Slot type 1 point 4 pin; Calculated at 0.015 yuan/point.
4. Ordinary integrated circuit, 4 pins for 1 point; Calculated at 0.015 yuan/point.
5. Close pin IC, 2 pins are 1 point; Calculated at 0.015 yuan/point.
1 point for 6.2 foot BGA; Calculated at 0.015 yuan/point.
7. Large machine mounted data shall be calculated by doubling the volume of components.
8. Surcharge is calculated at RMB 20 per hour
9. This quotation does not include testing fees, transportation fees, taxes, etc.
PCBs testing and assembly costs
The PCBs test fee is generally calculated at 2 yuan per board. The PCBs component and packaging costs are generally 0.8 yuan per block, which is the fourth part of the cost
Now, the total cost of the above four parts is the processing cost of PCBs patch!
Just upload Gerber files, BOM files and design files, and the KINGFORD team will provide a complete quotation within 24h.