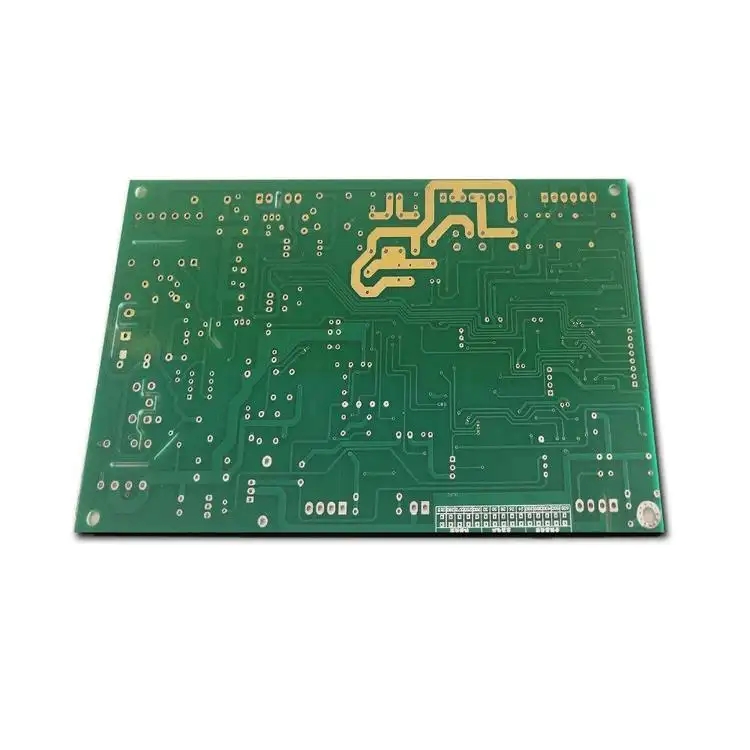
Specification and production process of aluminum substrate
All aluminum based circuit board manufacturers will have corresponding aluminum substrate production specifications and aluminum substrate production process guidance. The aluminum substrate production specifications are the main basis for production preparation and the main technical documents of aluminum substrate manufacturers. The perfect aluminum substrate production process guidance is a practical measure for circuit board manufacturers to effectively implement fine management.
Aluminum PCB has been widely used in hybrid integrated circuit, automobile, office automation, high-power electrical equipment, power supply equipment and other fields in recent years due to its excellent heat dissipation, machinability, dimensional stability and electrical performance. The aluminum based copper clad laminate was first invented by Sanyo in 1969. China began to develop and produce it in 1988. Since 2000, it has been developed and mass produced. In order to adapt to mass production, chemical production and stable quality production, this production specification is specially prepared. The mainstream aluminum substrate is relatively famous in the market. The aluminum substrate mainly depends on the thermal conductivity, withstand voltage value and thermal resistance value, which are related to the life and life of the aluminum substrate.
Aluminum substrate
2. Scope: This production specification introduces and explains the whole process of aluminum base copper clad laminate to ensure its smooth production in our company.
3. Process flow:
Cutting → drilling → dry film optical imaging → plate inspection → etching → etching → green oil → character → green inspection → tin spraying → aluminum substrate treatment → punching → final inspection → packaging → shipment
4. Precautions:
4.1 The aluminum substrate is expensive, so special attention should be paid to the standardization of operation during the production process to prevent scrap caused by non-standard operation.
4.2 Operators of each process must handle with care to avoid scratches on the board surface and aluminum base surface.
4.3 Operators of each process shall avoid touching the effective area of aluminum substrate with their hands as far as possible. During tin spraying and subsequent processes, only the edges of the plate shall be held. It is strictly prohibited to touch the plate directly with fingers.
4.4 The aluminum base plate is a special plate, and its production should be highly valued by each process in each area. The section head and the foreman should personally check the quality to ensure the smooth production of the plate in each process.
5. Specific process flow and special manufacturing parameters:
5.1 Opening
5.1.1 Strengthen incoming material inspection (the sheet with protective film on the aluminum surface must be used).
5.1.2 The baking board is not required after cutting.
5.1.3 Handle with care and pay attention to the protection of aluminum base (protective film).
5.2 Drilling
5.2.1 The drilling parameters are the same as those of FR-4 plate.
5.2.2 Aperture tolerance is very strict, and 4OZ based Cu shall pay attention to controlling the generation of flaring.
5.2.3 Drill with the copper sheet facing upwards.
5.3 Dry film
5.3.1 Incoming inspection: Before grinding the plate, the protective film of the aluminum base surface must be inspected. If it is damaged, it must be stuck firmly with blue glue before pretreatment.
5.3.2 Grinding plate: only the copper surface is treated.
5.3.3 Film pasting: copper surface and aluminum base surface must be pasted.
The interval between the grinding plate and the film is controlled to be less than 1 minute to ensure that the film temperature is stable.
5.3.4 Clamping: pay attention to the accuracy of clapping.
5.3.5 Exposure: exposure ruler: there is residual glue in 7-9 grids.
5.3.6 Development: pressure: 20~35psi; speed: 2.0~2.6m/min
Each operator must operate carefully to avoid scratches on the protective film and aluminum base surface.
5.4 Inspection plate
5.4.1 The line surface must check all contents according to MI requirements.
5.4.2 The aluminum base surface shall also be checked, and the dry film of the aluminum base surface shall be free from falling and damage.
5.5 Etching
5.5.1 As the copper base is generally 4OZ, there will be some difficulties in etching. The first board can only be made after being approved by the foreman. The spot check of line width and line gap shall be strengthened in the process of making the board. The line width shall be spot checked every 10PNL board and recorded.
5.5.2 Recommended parameters: speed: 7~11dm/min Pressure: 2.5kg/cm2
Specific gravity: 25Be Temperature: 55 ℃
(The above parameters are for reference only, subject to the test panel results)
5.5.3 During film stripping, it shall be noted that the time shall be controlled within 4~6min. As aluminum reacts with NaOH, it must be ensured that the film is stripped clean. During film stripping, the film stripping solution shall not be heated. For the plate without protective film on the aluminum surface, after it is taken out of the film remover, the plate shall not be left standing and the film remover on the plate shall be cleaned with water in time to prevent alkali from biting the aluminum surface.
5.6 Corrosion inspection
5.6.1 Normal inspection plate.
5.6.2 It is forbidden to repair the circuit with a blade to avoid damaging the medium layer.
5.7 Green oil
5.7.1 Production process:
Grinding plate (copper surface only) → silk screen green oil (first time) → pre drying → silk screen green oil (second time) → pre drying → exposure → development → acid washing and soft brush of the plate grinder → post curing → next process
5.7.2 Reference parameters:
5.7.2.1 36T+100T screen yarn
5.7.2.2 75 ℃ for the first time × 20-30min; 75 ℃ for the second time × 20-30min
5.7.2.3 Exposure: 60/65 (single side) 9~11 grids
5.7.2.4 Development: speed: 1.6~1.8m/min Pressure: 3.0kg/m2 (full pressure)
5.7.2.5 Post curing: 90 ℃ × 60min+110℃ × 60min+150℃ × 60min
The above parameters are for the use of DSR-2200TL ink and are for reference only.
5.7.3 Pay attention to the control of bubbles during silk screen printing. If necessary, 1-2% thinner can be added.
5.7.4 The clapper shall check the board surface before clapping, and ask the foreman for instructions in case of problems before clapping.
5.8 Tin spraying
5.8.1 Before tin spraying, remove the protective film from the aluminum substrate with protective film before tin spraying.
5.8.2 Hold the edge of the plate with both hands, and do not touch the plate directly (especially the aluminum base surface).
5.8.3 Pay attention to operation and prevent scratching.
5.8.4 Bake the plate at 130 ℃ for 1 hour before tin spraying, and the interval between the baking plate and tin spraying shall be less than 10 minutes. To avoid stratification and oil loss caused by large temperature difference.
5.8.5 Reworked plates are only allowed to be re sprayed once. If there are plates that have been re sprayed more than once, they should be distinguished for special treatment.
5.9 Passivation treatment of aluminum base surface
5.9.1 Horizontal passivation line process:
① Grinding plate (500 # brush) → ② water washing → ③ passivation → ④ water washing × 3 → ⑤ Blow dry → ⑥ Dry
Remarks: ① Grinding plate: only grind the aluminum surface, and grind the plate according to FR4 parameters. It is required to check that the circuit is free of scratches, tin surface blackening and other defects, and the abrasion marks are even.
③ Passivation:
Liquid medicine composition control concentration, cylinder opening, cylinder volume, liquid medicine temperature, spraying pressure, conveying speed, tank changing frequency
Na2CO3
(CP grade) 50g/l 6500g 130L 40~50 ℃ 2.0~3.0 1.0~1.5m/min Effective soaking time 10~15S 100m2
K2CrO4
(CP grade) 15g/l 1950g
NaOH
(CP grade) 3g/l 390g
⑥ Drying: 80~90 ℃ is required.
5.9.2 Precautions:
a. The board receiving operator must pay attention to the inspection when receiving the board. Those not well polished can be removed for grinding again, and those with scratches can be removed and sanded with sandpaper (2000 #) before removing the grinding board.
b. In case of discontinuous production, maintenance must be strengthened to ensure that the conveying is clean and the water tank is clean.
5.9.3 After the foreman confirms that the aluminum base surface has been treated, the plate can be transferred downward.
5.10 Punching plate
5.10.1 Hold the plate edge with both hands and pay attention to the protection of aluminum base surface.
5.10.2 The aluminum base plate shall be formed with high-grade beer die punching plate, and the punching and shape shall be punched at one time or separately. When punching the plate, a white paper back punching plate shall be placed on the aluminum surface according to MI requirements.
5.10.3 The inspection shall be strengthened during punching, and the green oil and the surface of the board shall not be removed.
5.10.4 It is unnecessary to wash the board during final inspection, and white paper is separated between boards.
5.10.5 Clean the mold with a brush every time the plate is punched.
5.11 Final inspection: carry out various inspections according to IPC comprehensive enterprise standards.
5.12 Packaging
5.12.1 Plates with different cycles and different material numbers shall be packed by category.
5.12.2 During packaging, paper separation and moisture-proof beads shall be placed, and the version number, production cycle (one month is one cycle), etc. shall be indicated after the model number on the minimum package label.
6. Rework method of final inspection scratch and oxidized aluminum substrate
The aluminum substrate with oxidation and scratch caused in the production process at the final inspection shall be reworked as follows.
6.1 Aluminum substrate with aluminum surface oxidized:
First, put the aluminum substrate circuit face up and place it on the desktop, cover the circuit with blue glue and press it tightly, then stick several double-sided adhesive tapes on the blue glue and stick a piece of bare copper plate on it, press it tightly, and then take it to the deburring machine for polishing. Note that the pickling must be turned off before grinding the plate, and the traveling wheel at this section must be washed with tap water to prevent acid from polluting the tin surface, or it can be directly put in from the water washing section after pickling, with the aluminum base surface facing upwards, and only the upper part of the plate can be turned on for grinding. If the ground plate still has oxidation, it can be grinded again.
Take down the grinded plates and put them on the drying section of the plate grinder for drying. Place them for 5~10min, or put them on the white paper in the tray and take them to the oven for drying at 100. ℃ × 5~10min, be careful not to take it to the forming washing machine for drying, because its low temperature will lead to aluminum surface oxidation.
6.2 Aluminum base plate with aluminum surface scratching:
6.2.1 For aluminum substrate with slightly scratched aluminum surface, rework the aluminum surface according to 6.1 aluminum surface oxidation method.
6.2.2 For the aluminum substrate with serious scratches on the aluminum surface, first use 2000 # sandpaper to smooth the scratches, then use 4000 # sandpaper to lightly brush it once, and then handle it according to 6.2.1 Rework method for aluminum substrate with oxidized aluminum surface.
To sum up, as long as the aluminum substrate manufacturer has a perfect aluminum substrate production process and standardized management, and then implements it to every job post and every work item in the production department, it is a practical measure for the circuit board manufacturer to effectively implement refined management. Only by implementing standardized management layer by layer, everything is standardized, everyone has something to do, aluminum substrate production has a standard process, and work has a specific plan, Only in this way can we improve the overall management level of the enterprise, fundamentally improve the execution of the enterprise, improve production efficiency, improve product quality, and enhance the market competitiveness of PCB manufacturers.