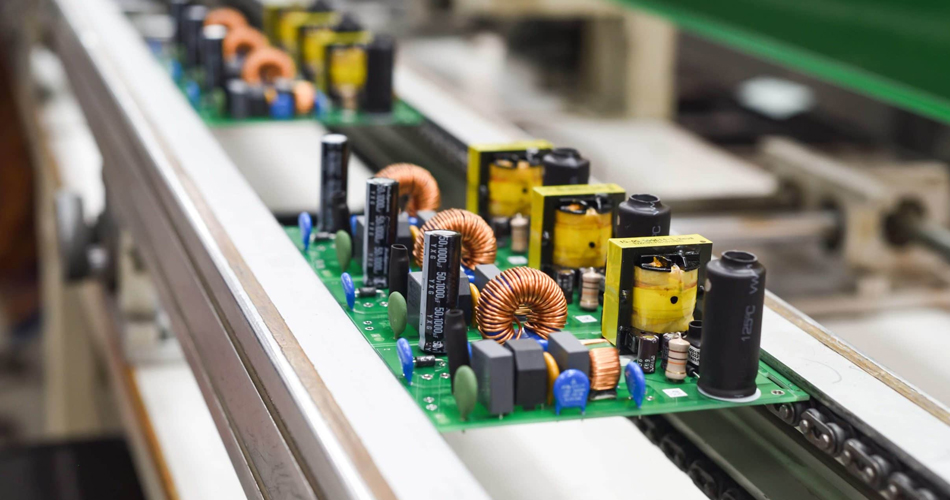
The PCB manufacturer and designer explain the SOP operation of PCBA factory staff
SOP (Standard Operating Procedure) is the operating standard for operators and the working principle of factory operators. It describes and standardizes the work of operators to achieve the consistency and standardization of operations.
There is a phenomenon in a PCB factory:
Such things happen almost every day when you do not operate according to SOP.
Why do workshop staff not operate according to SOP? What is the problem?
1. SOP is too simple, and the steps and requirements are not clearly described
SOP should be from the beginning of the action to the end of the action. Each action and specification in the middle should be described in detail, and each undesirable phenomenon should have pictures of good products and defective products.
2. The content of SOP is unreasonable
Each process, step and definition in the SOP should be based on a basis. It is not allowed for the person who wrote the SOP to define it casually. The most basic point is to consider the comfort of employees.
3. The staff found that the operation according to SOP was not smooth
Is it to overcome difficulties and work according to SOP? Or do you work in your own way? Will the employee feed this information back to the team leader? In most cases, employees will not actively give feedback.
At this time, the workshop team leader needs to take the initiative, not only to find problems, but also to take the initiative to analyze and improve.
Part 1 Functions of SOP
1. Record the technology and experience accumulated by the enterprise in standard documents to avoid technology loss due to the flow of technicians;
2. Enable operators to quickly master more advanced and reasonable operation technology after short-term training;
3. It is easy to trace the causes of defective products according to the operation standards;
4. Standardize the production management and make the production process orderly, standardized, visualized and simple;
5. Establish a good corporate image and improve customer trust and satisfaction;
6. It is the most basic and effective management tool and technical data of the enterprise.
Part 2 Six Elements of SOP
1. Material name and quantity
Before production, it is required to confirm whether the materials required by this station are consistent with the materials prepared, whether the quantity is correct, and whether the materials have passed the IQC inspection. The production can be started only after all are confirmed to be correct.
Never accept, produce or transfer defective products during production.
2. Fixture
Calibrate and check the fixture before going to work every day to confirm whether the fixture can be used normally.
3. Equipment name and parameters
The equipment operators must be trained and qualified before they can operate the machine. Before starting the equipment, they should carefully read the equipment instruction manual and the setting values of various parameters of the equipment, and then operate the machine according to the instruction manual, and confirm that the set parameter values are the same as the required parameter values.
4. Operation Steps
The operation steps are the key points in the SOP content, which must be concise and clear, so that people can understand and know how to operate at a glance.
The effect that SOP needs to achieve is that a newcomer can operate independently and the product quality is qualified, which is also the highest level of SOP.
5. Staffing
Personnel must be determined for each work position in SOP, so as to avoid the need for team leaders to assign personnel to work every day.
In this way, the employees know what they need to do before going online every day, and can make them more proficient in their own work position. The fixed number of workers can not only save time, but also ensure the quality.
6. Safety factors
Any operation may cause product quality problems, so we must include operation precautions, inspection items and some personnel safety instructions in SOP.
Part 3 Standard template of SOP
1. Company name (full name)
2. Standard Operation Instructions (SOP)
3. Document name, version number, page number and effective date
4. Production process diagram
5. Operation Steps
6. Precautions for human, machine, material and measurement
7. Date of production, review, approval and signature
SOP is formulated by the enterprise according to the current process, tooling, equipment and other current conditions. If the current situation changes, or the old SOP is no longer applicable, it should also be continuously improved according to the changes, which is also the essence of lean production.
According to SOP operation, it is the most common and simple thing for employees, but there will be many problems behind it. These problems are not only related to the front-line manufacturing departments, but also closely related to the auxiliary departments (quality, IE, PE, TE, etc.).
Only when all departments work together to improve the efficiency of the corresponding work through each SOP, the enterprise will inevitably improve the overall operating efficiency.
The above is the sop operation explained to you by the pcb manufacturer.