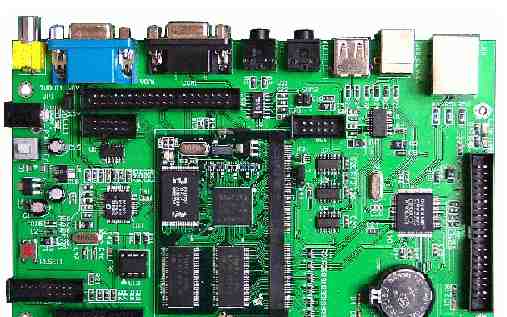
Many customers of PCBA sampling processing want to get the product immediately after signing the contract, it is best to drink a cup of tea, and will continue to want to reduce the delivery time and frequently urge the salesman. In fact, every process of PCBA proofing processing takes time, and many processes of PCBA proofing can not be rushed. So what are the production processes of PCBA proofing processing? Next, PCBA processing manufacturer kinhford Electronics will introduce you.
1.Repair: The function of repair is to rework the PCBA board that has detected faults.
2. Mounting: The role of mounting is to accurately install the surface assembly components to the fixed position of the circuit board.
3. Detection: The function of detection is to detect the SMT welding quality and assembly quality of the assembled circuit board.
4. Curing: The role of curing is to melt the patch glue, so that the surface assembly components and the circuit board are firmly bonded together.
5. Cleaning: The role of cleaning is to remove welding residues such as flux that are harmful to the human body on the assembled circuit board.
6. Solder paste printing:
Use solder paste printing machine to print solder paste on the circuit board to prepare for SMT welding of electronic components.
7. Reflow welding: The role of reflow welding is to melt the solder paste, so that the surface assembly components and the circuit board are firmlybonded together.
8. Dispensing: Dispensing is to drop red glue to the fixed position of the circuit board, and its main function is to fix the components to the PCB board. This is an optional process, mainly for heavy devices on the board, the use of red glue process can increase the adhesion.
Kinhford Electronics Co., Ltd. specializes in providing integrated PCBA electronic manufacturing services, including upstream electronic component procurement to PCB production and processing, SMT patches, DIP plug-ins, PCBA testing, finished product assembly and other one-stop services.
The company gives full play to its competitive advantages in scale procurement and quality control, and has signed long-term cooperation agreements with many electronic component manufacturers at home and abroad and around the world to ensure the quality and stable supply of raw materials, and transfer the benefits to customers.
Long-term maintenance of IC, resistors, capacitors, inductors, audiodes and other components procurement advantages, can greatly save customers' inventory costs, improve production turnover efficiency, save time. Currently for the United States, Britain, Japan, Russia, France, Canada, Australia, Romania, Switzerland and other countries and regions to provide PCBA processing services.
1.Strength guarantee
▪SMT workshop: with imported SMT machines, optical inspection equipment, can produce 4 million points per day. Each process is equipped with QC personnel, who can keep an eye on product quality.
▪DIP production line: there are two wave soldering, of which there are more than 10 old employees who have worked for more than three years. The workers have high proficiency and can weld all kinds of plug-in materials.
2. Quality assurance, cost-effective
▪ High-end equipment can be attached to precision special-shaped parts, BGA, QFN, 0201 materials. Also can be template patch, loose material hand. Sample and size batch can be produced, proofing from 800 yuan, batch 0.008 yuan/point, no start-up fee.
3. Rich experience in SMT and welding of electronic products, stable delivery
▪ Accumulated services for thousands of electronic enterprises, involving many types of automotive equipment and industrial control motherboard SMT processing services, products are often exported to Europe and the United States, quality can be affirmed by new and old customers. Delivery on time, normal 3-5 days after complete materials, small batches can also be expedited on the same day.
4. Strong maintenance ability, perfect after-sales service
▪ Experienced maintenance engineers can repair all kinds of patch welding caused by bad products, to ensure the connectivity of each circuit board. ▪ 24-hour customer service staff responds at any time to solve your order problems as quickly as possible.