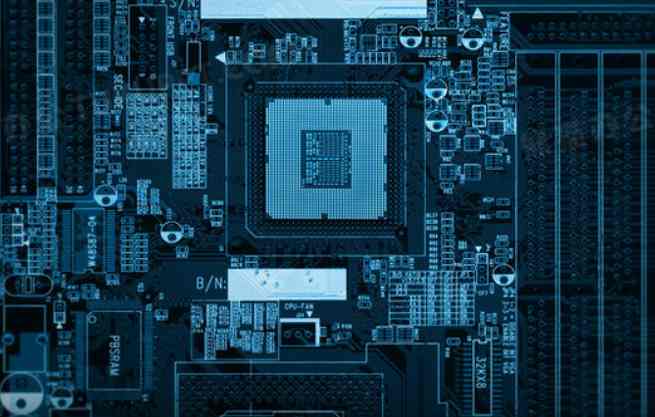
As an electronic processing supplier, we must have a thorough understanding of all the processing processes in the plant, especially the SMT patch processing as the main process.
Inside each production workshop, there will be SMT patch processing lines. In this line, we can divide into the following parts.
1, lead-free solder paste printing machine
In the previous article, I already mentioned lead-free solder paste printing. In this part, the machine we use is SMT semi-automatic printing machine. In this operation, we should pay attention to the steel mesh and PCB segment, the steel mesh and PCB pad must be completely coincident, determined after 3 blocks of test, start normal production. After printing each PCB should be self-tested, solder paste printing does not allow a lot of tin, tin, and even tin, migration and other undesirable phenomena. Printed defective products should be carefully cleaned. Remove the wire mesh in time. Supplement the paste in time to ensure the amount of steel mesh rolling of the solder paste.
2. Mounting of small materials
The machine we use in this process is the CP machine. Materials can be installed quickly. Before starting, the work that needs to be done, such as placement of materials, positioning of the machine, when the machine is yellow, should be prepared to fill the material.
3. Mounting of large materials
This process is designed to help add CP to PCBS of large materials that the machine cannot install, such as crystal before. For this part, we used XP machines. It can achieve huge material automatic installation. The notification process is similar to CP.
4, QC before the furnace
This link is an important part of the overall SMT process. This process can ensure that all semi-finished products in the furnace are completely problem-free, so it is called the furnace QC. This position is usually used in QC to check the exhaustion of machines from PCB boards. To see if there is leakage, part of the material, etc. Then, the paper is made to leak or part of the material manually corrected.
5, the role of reflow welding is to make the solder paste reflow melting layout, so that the material is welded to the plate tight. This process requires the machine to wave soldering. Wave soldering should point out that there are several points. The first is the temperature regulation in the furnace, which needs to take into account the degree of heat resistance in the PCB board and the material, and then the optimal temperature will be set so that the PCB board is basically no problem after the furnace.
6, QC after the furnace
Quality is the life of an enterprise. In the furnace, there will certainly be some problems, such as air welding, welding, welding, etc. So how do you spot these problems? We must also test the problem in this link with the past QC, after the furnace plate. Then modify it manually.
7. QA random inspection
When all the automatic post-assembly process is gone, we still have the last step, which is sampling. Sampling this step, you can roughly calculate the production of our products, the qualified rate, that is, the quality. Of course, the sampling must be carefully done every step, do not miss every detail of the layout, so as to ensure the quality of the company's products.
8. Storage
Final storage. Storage also needs to pay attention to packaging, can not be sloppy. This gives the customer a perfect experience.
Ten points to note during SMT patch processing
SMT
SMT is the Surface assembly Technology (surface Mounted technology)(Surface Mounted Technology), is currently the most popular technology and process in the electronic assembly industry. Electronic circuit Surface Mount Technology (SMT), known as surface mount or surface mount technology. It is a pin-free or short-lead surface assembly component (referred to as SMC/SMD, Chinese called chip components) installed on the surface of the Printed Circuit Board (PCB) or other substrate surface, by reflow welding or dip welding and other methods to weld the circuit assembly technology.
SMT patch processing
SMT refers to the short term PCB(PrintedCircuitBoard), the Chinese name is called printed circuit board, also known as printed circuit board, printed circuit board, is an important electronic part, is the support body of electronic components, is the provider of electrical connections of electronic components. Because it is produced by electronic printing, it is called a "printed" circuit board.
Under normal circumstances, the electronic products we use are all designed by pcb plus a variety of capacitors, resistors and other electronic components according to the design of the circuit diagram, so all kinds of electrical appliances need a variety of different SMT patch processing technology to process.
Ten points to note for SMT patch processing
1. Generally speaking, the temperature specified in the SMT processing workshop is 25±3℃;
2. Materials and tools required for solder paste printing solder paste, steel plate, scraper, wiping paper, dust-free paper, cleaning agent, stirring knife;
3. The commonly used solder paste alloy composition is Sn/Pb alloy, and the alloy ratio is 63/37;
4. The main components of the solder paste are divided into two parts: tin powder and flux.
5. The main function of flux in welding is to remove oxides, destroy the surface tension of melting tin, and prevent re-oxidation.
6. The volume ratio of tin powder particles and Flux(flux) in the solder paste is about 1:1, and the weight ratio is about 9:1;
7. Warehouse material access principle is first in first out;
8. When the solder paste is used in opening, it must go through two important processes of warming and stirring;
9. The common production methods of steel plates are: etching, laser, electroforming and other production methods;
10. The full name of SMT is Surface mount(or mounting) technology, which means surface mounting technology in Chinese;