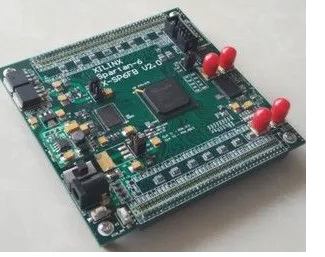
PCB Rapid proofing is a circuit board proofing service that is designed, manufactured, assembled and tested in a short period of time in an accelerated process. Production times can range from 24 hours to 7 days, depending on the complexity of the design.
Manufacturing a prototype PCB contains all the vague requirements and details needed to reduce delivery time and manufacturing costs. In addition, PCB prototypes allow users to test how the finished product works. It enables customers to make required changes while manufacturers can check for faults to improve performance and efficiency.
Therefore, corrections, omissions, corrections, additions and subtractions are captured in this phase to ensure that the production PCB has zero technical or mechanical defects.
Test run/pre-production
The beta run involves building fast flip boards in batches of hundreds to thousands of pieces. This is one of the most important stages of the process, as these PCB templates are often turned into final products. So the manufacturer must eliminate all errors at this stage.
This process requires electrical testing, optimizing board layout, checking tool arrangements, avoiding traps, and more.
The stage is rapid PCB manufacturing for market applications. Orders at this stage are higher and better than the other steps, but may take longer to complete.
Only after the design and engineering team has completed the previous phase to fine tune everything and build a high-quality board can a rapid shift to PCB manufacturing enter this phase.
Adherence to DFM and DFT guidelines can reduce completion times and provide high-quality boards. Also, check the usability of components before including them in your design and determine the best layout strategy for a compact design. Finally, establish clear testing protocols and requirements in advance to reduce turnaround time.
High-density interconnect (HDI) boards with multiple through-hole structures require sequential lamination cycles, a task similar to manufacturing multilayer boards. This type of board increases manufacturing time, cost, and complexity.
The time required for each lamination cycle depends on the number of board layers in the stack and the materials used. Each individual layer adds an average of 4-5 days to the production process, including drilling, filling and plating time. And board manufacturers need at least an extra day for the outer layer processing.
Via-in-Pad plating
Through holes in pads have become a typical application in most PCBS because they can keep heat away from the lower part of the component or save space. However, merging them will add at least one day to the cycle time.
The manufacturing diagram represents the important manufacturing data, as shown below.
Therefore, you need to understand the PCB manufacturer's ability to close the gap between the design document and the DFM to reduce or avoid rework time delays. And always mention whether the prototype complies with IPC Class 2 or Class 3 manufacturing standards.
Similarly, multilayer PCB lamination is carried out while considering material cost and availability. Rare materials will take more time to source, increasing turnaround time. During this time, the controlled impedance meter of the plot is verified to ensure that it identifies the track width and target impedance that need to be controlled to avoid delays due to mismatches of information.
Finishing is also time consuming, as each coating takes a specific amount of time to complete. For example, ENIG takes about 1.5-2 hours to complete, while HASL takes only 15-20 minutes at most.
As a result, it will take more time to complete high-quality PCBS with two surface finishes, such as ENIG for surface mount connectors and hard gold for edge connectors. Each finish is applied individually and the time will add up.
Assembly drawings and manufacturing instructions
Manufacturing instructions and assembly drawings help with board inspection because they contain part lists, bottom and top views, shapes, and more. So consider the following points to prevent delays during board assembly.
- Comply with DFA guidelines while confirming component footprints do not match. If parts are supplied, follow the accompanying guidelines
- Ensure that the silk screen feature marks remain visible
- Send a full BO with manufacturer part number and product description
Circuit board manufacturing is a complex process. Getting it done faster requires more attention, so be sure to consider these factors before choosing a PCB quick proofing manufacturer.
Rapid prototyping and production requires experience if the final product is to be functional and of high quality. Therefore, consider a manufacturer/assembler with a good reputation in the market.
Also, consider lead times before handing over designs. Some manufacturers can complete the process in 24 hours, while others can do it in a few days. But faster is not always better. The key factor is to ensure that the manufacturer's speed fits your schedule. Short-term production is usually more expensive.
Any PCB rapid proofing manufacturer should have equipment that can manufacture high-quality boards faster. You can ask them for a list of equipment, but the sure way is to go to the factory and see for yourself.
Manufacturers should focus more on quality than speed, so high-speed manufacturing should not affect product quality. Ideally, this partner should have a certified quality control process.
Not only does kinhord have several certifications, but we also have several well-known customers. This combination guarantees you our quality in PCB manufacturing and assembly.
The cost is high because you can only close the deal if the offer is within your budget. Cheap is not always best, because quality can be compromised. So try to get a good deal through quality assurance.