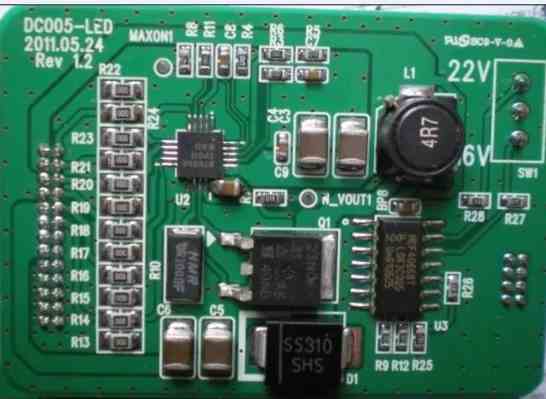
Sometimes there will be some poor processing phenomena in the production and processing process of the patch factory. The most intuitive feeling for the patch processing is the quality of the solder joint, and the quality of the solder joint has a direct impact on the quality of PCBA processing. Next, I will introduce the common reasons for the non-rounded solder joints in SMT processing.
There may be seven reasons for the non-rounded solder joints in SMT processing:
1. Slag and bubbles: During the welding process, the solder will react with the PCB surface after melting, and then if there are impurities on the solder surface, such as bubbles and solder slag, it will make the solder joint not round.
2. Improper temperature control: If the temperature is insufficient, the solder will not be completely melted, and the solder joint may not be rounded. On the other hand, if the temperature is too high, the solder joint may be deformed.
3. Insufficient welding time: Short welding time may lead to unrounded solder joints. If the solder does not have enough time to melt and flow during the solder joint formation process, the solder joint may not be round.
4. Insufficient amount of solder: If the amount of solder is insufficient, the solder joint may not be round. If the amount of solder is too little, the solder joint will not fill the pad adequately.
5. PCB surface is not smooth: If the PCB surface is not smooth, the solder joint may not be round. During the welding process, the solder will follow the PCB surface to form a solder joint, if the PCB surface is not smooth, the solder joint may not be rounded.
6. The solder particle is too large: if the solder particle is too large, the solder joint may not be round. This is because the solder particles are too large to make the solder joint surface is not smooth.
7. Dirty welding tip: If the welding tip is not clean, the solder joint may not be round. This is because the dirt on the weld mouth will affect the fluidity and adhesion of the solder.
Therefore, in the SMT process, in order to ensure the quality of the solder joint, it is necessary to pay attention to the above factors, and make corresponding adjustments and improvements according to the specific circumstances.
PCBA processing is a complex process that requires attention to many details to ensure processing quality. The following are four ways to ensure the quality of PCBA processing:
1. Quality control: By implementing good quality control procedures, it is possible to ensure that all PCBA boards can meet the expected quality standards. This can include inspection and testing at different stages, from PCB manufacturing to component procurement and assembly, where strict quality control is required.
2. Inspection and testing: In the process of PCBA processing, inspection and testing is an essential step. These tests can cover aspects such as component mounting position and orientation, weld quality, and circuit connectivity. Through these tests, potential problems can be found and solved in time to ensure the quality of the PCBA board.
3. Use high-quality raw materials: Selecting high-quality raw materials can ensure the reliability and performance of the PCBA board. When selecting PCBS, components, welding materials and other accessories, attention should be paid to their quality and source. Choosing a certified supplier can reduce potential risks and ensure the quality of the PCBA board.
4. Professional technical team: A professional technical team can ensure that every step of PCBA processing is strictly supervised and controlled. The technical team should have in-depth PCBA processing knowledge and experience, and can provide guidance and support throughout the processing process to ensure the quality of the PCBA board.