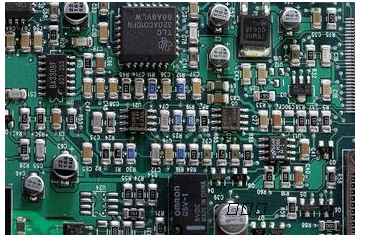
What are the solder paste processes in SMT patch processing?
The solder paste process is a crucial part. Solder paste process directly affects the quality and reliability of PCB patches. In this paper, the solder paste process in SMT processing will be introduced in detail, and the influence of different process parameters on the effect of SMT will be discussed.
First, let's understand what solder paste is. Solder paste is a material used for welding and consists of a conductive powder (usually tin powder) and flux. Conductive powders provide electrical conductivity, while fluxes help weld flow and wet surfaces. In SMT patch processing, the solder paste is printed on the solder pad on the PCB surface, and then the component is precisely placed on the solder paste, and finally melted by heat to form a solder joint.
The solder paste process in SMT patch processing includes the following aspects:https://www.kingfordpcb.com/yuan.php?time=1686665727
1. Composition of solder paste: The composition of solder paste plays an important role in welding quality. Usually, the solder paste consists of conductive powder, flux and solvent. The particle size and shape of conductive powder will affect the reliability and electrical properties of solder joints. The composition and proportion of flux will affect the fluidity and wettability of the welding. Suitable solvent can control the viscosity and fluidity of the solder paste. 2. Viscosity and fluidity of solder paste: The viscosity and fluidity of solder paste are crucial to the printing process and welding quality. Too high viscosity will lead to poor printing, too low viscosity will affect the solder paste coverage and solder joint formation. In the printing process, it is necessary to select the appropriate printing pressure and printing speed to ensure that the solder paste is evenly distributed on the pad.
3. Welding temperature curve: welding temperature curve refers to the temperature change curve of heating in the welding process. A suitable welding temperature curve ensures that the solder paste is fully melted and a reliable solder joint is formed. In general, the welding temperature curve includes a preheating zone, a thermal activation zone and a cooling zone. The preheating zone is used to remove volatiles from the pads and solder joints, the heat activation zone is used to melt the solder paste and form the solder joints, and the cooling zone is used to cure and cool the solder joints. 4. Welding equipment and process parameters: The selection of appropriate welding equipment and process parameters is essential to obtain high-quality welding results. Common welding equipment includes reflux furnaces and hot blast furnaces. Reflux furnaces are usually used for batch production, while hot blast furnaces are suitable for small batch or manual welding. The temperature control accuracy and heating uniformity of the welding equipment will also affect the welding results
5. Inspection and quality control: In the SMT patch processing process, the inspection and quality control of the solder paste process is essential. Common methods include solder paste viscosity test, solder joint appearance inspection and solder joint reliability test. Through regular inspection and quality control, potential problems can be detected and corrected in time to ensure the quality and reliability of the patch.
It should be noted that different PCBS and components may require different solder paste process parameters. Therefore, in practical applications, it is necessary to adjust and optimize the process parameters according to the specific situation. To sum up, the solder paste process in SMT patch processing involves the composition of the solder paste, viscosity and flow, welding temperature curves, welding equipment and process parameters, as well as inspection and quality control. Through reasonable selection and optimization of these process parameters, high quality and reliable welding results can be obtained.