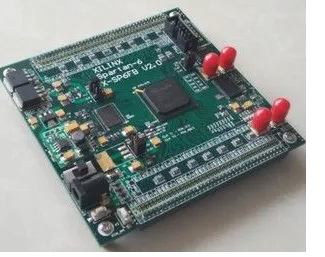
Will PCB be damaged during PCBA processing and assembly?
This article is written and edited by kinhford Electronic Technology Co., LTD. PCBA processing. Please read the following details.
A few years ago, a colleague contacted me with a question: "How can we weld a plate with a Tg of 180°C or even 200°C at 225-245°C without damaging the plate? Even with lead boards, the peak reflux temperature is much higher than the Tg of the boards. How is that possible?"
The answer is simple. Every time a printed circuit board is exposed to welding temperatures, it breaks. This is applicable not only to lead-free welding applications, but also to eutectic welding composed of tin lead. Tg is one of several parameters to be aware of. In the case of Tg, many designers refer to this value as a measure of stability. High Tg products have smaller thermal expansion on the Z axis. Below the Tg, the laminate epoxy system is hard and strong. You can expect a thermal expansion rate of about 25 ppm /°C. Above Tg, the epoxy becomes soft and pliable. When the epoxy resin is soft and pliable, the expansion rate can be up to 10 times the expansion rate compared to the expansion rate less than the Tg value.
The parameter that best determines when the board begins to suffer thermal damage is called the maximum continuous operating temperature (MOT). An MOT is a parameter tested and certified by Underwriters Laboratories (UL). Bare plate manufacturers should go through their most destructive process to construct eligible samples and submit them to UL for compliance testing. Boards with a certified MOT of 130°C will not cause thermal damage in the field when exposed to temperatures of 130°C or lower. Above the MOT value, the epoxy resin used to make the PCB begins to decompose at the molecular level. Energy is released as molecular bonds break due to thermal stress. The energy released shows up as smoke. The higher the temperature the board is exposed to, the faster the damage occurs. The damage is cumulative.
Drying and baking moisture on the PCB is a good indication of the damage threshold. For PCBS, the dry baking temperature must be above the boiling point of water (100°C) but below the MOT. In theory, you can dry a circuit board with a MOT of 120°C at 110°C for a year without thermal damage to the epoxy resin from which the PCB is made. Similarly, if the dry baking temperature is 121°C, the epoxy will begin to suffer damage. In theory, a degree above MOT could take months to do real damage. At 300°C, PCB damage is so rapid that delamination occurs in less than a minute. The higher the temperature, the less time it takes to burn off the epoxy from the PCB. In fact, the MOT is the test value. The actual PCB may exceed this value by several degrees.https://www.kingfordpcb.com/yuan.php?time=1685970626
Every time a printed circuit board is exposed to assembly temperatures, the epoxy resin that holds the PCB together is damaged. This is the case for conventional eutectic and lead-free welding temperatures. This is where the decomposition temperature (Td) value comes from. By definition, this is the temperature at which 5% weight loss occurs through thermogravimetric analysis (TGA). Decomposition is the breaking of chemical bonds in a resin system. The epoxy in the laminate is basically burning. A weight loss of 2% to 3% of this nature will adversely affect circuit performance. The damage caused by decomposition is cumulative. This limits the number of lead-free assembly cycles at temperature on the PCB.
The higher the Td, the slower the burn rate. Materials with Td equal to or below 300°C are suitable for eutectic tin-lead welding. Materials with Td above or above 300°C are more suitable for lead-free welding. In this case, the higher the Td value, the higher the heat resistance of the epoxy resin, and the better. High rated Td materials will still burn off, but decay at a slower rate. Laminates that meet the requirements for lead-free assembly are usually phenolic cured epoxy systems. Phenolic cured epoxy resin systems usually have higher Td than traditional butyl wax cured epoxy resin systems. For this reason, dice cured epoxy systems are not considered lead-free assembly friendly.
Welding has always caused damage to printed circuit boards. The damage of solder - lead welding is not enough to cause great concern about the temperature of eutectic welding. Lead-free welding is and should remain a concern for everyone.