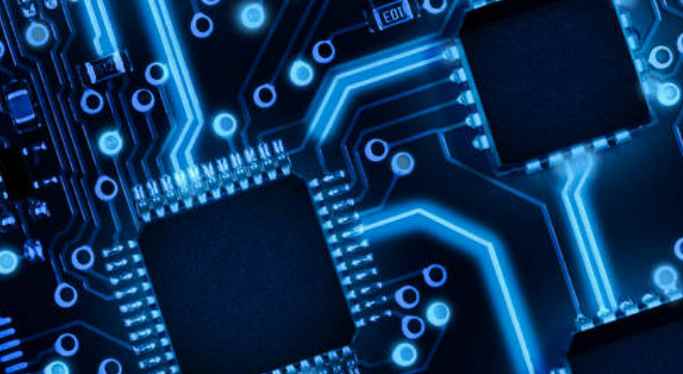
After nearly 10 years of hard work, Automatic Optical Inspection systems (AOI) have finally been successfully applied to printed circuit board (PCB) production lines. During this time, the number of AOI suppliers has increased dramatically, and various AOI technologies have also developed significantly. Today, from simple camera systems to complex 3-D X-ray inspection systems, many suppliers have been able to provide AOI equipment that can be used in almost all automated production lines.
Over the past decade, the performance of solder paste presses and SMT mounters has improved, resulting in faster, more accurate and more reliable product assembly. The yield of the big manufacturers has also improved. The increasing number of SMT packaged components provided by component manufacturers has also promoted the development of automation in the printed circuit board assembly line. The automatic mounting of SMT components can almost completely eliminate the errors that may be caused by manual assembly on the production line.
In the PCB manufacturing industry, the miniaturization and densification of components has always been the development trend. This has prompted manufacturers to install AOI equipment for their production lines. Because it is no longer possible to perform reliable and consistent inspection of closely distributed components and maintain accurate inspection records by manual means. The AOI can carry out repeated and accurate inspection, and the storage and publication of the test results can also be realized electronically.
In many cases, the process engineer's inspection and adjustment of the paste press and assembly process can ensure that the paste fouling rate (tin spatter rate) of the production line is only a few parts per million (ppm). For a high volume/low mix production line, the typical solder paste stain number is 20 to 150 parts per million. Practice has proved that it is difficult to find each and every solder paste fouling only by sampling the printed circuit board samples. Only 100% inspection of all circuit boards can ensure greater inspection coverage, thus enabling statistical process control (SPC).
To a large extent, only a small part of the specific kinds of solder paste stains actually exist, and the production of these solder paste stains can be associated with some specific production equipment. In many cases, you can also attribute a solder paste stain to a particular piece of equipment. However, for some variables, such as component offset (due to self-correcting effects in the reflux process), it is impossible to trace back to a specific production step. Therefore, in order to be able to detect all solder paste stains, it is necessary to carry out 100% testing on the production line for each production step.
However, in reality, due to economic considerations, PCB manufacturers cannot test every circuit board after every process. Therefore, process engineers and quality control managers must carefully consider how best to balance their investment in testing with the benefits of increased production.
In general, as shown in Figure 1, you can effectively apply AOI after any of the four production steps in a production line. The following paragraphs describe the application of AOI after four different production steps on an SMT PCB production line. We can roughly divide AOI into two categories: problem prevention and problem detection. In the following description, detection after solder paste printing, after (chip) device placement, and after component placement can be classified as prevention problems, and the last step? Inspection after reflow welding?? It can be classified as problem finding, because detection does not prevent defects at this step.
1. After solder paste printing: To a large extent, defective welding comes from defective solder paste printing. At this stage, you can easily and economically remove welding defects on the PCB. Most 2-D inspection systems monitor solder paste offset and skew, deficient solder paste areas, and spatter and short circuits. The 3-D system can also measure the amount of solder.
2. After (chip) device placement: This stage of inspection can detect (chip) device missing parts, shift, skew and (chip) device direction fault. The inspection system also checks solder paste on pads used to connect tightly spaced and ball grid array (BGA) components.
3. After component placement: After the device attaches components to the PCB, the inspection system can check for missing, offset, and skewed components on the PCB, and can also detect errors in component polarity.
4. After reflow welding: At the end of the line, the inspection system can check for missing components, offsets and skews, as well as defects in all aspects of polarity. The system must also detect the correctness of the solder joints and defects such as insufficient solder paste, welding short circuit and foot warping.