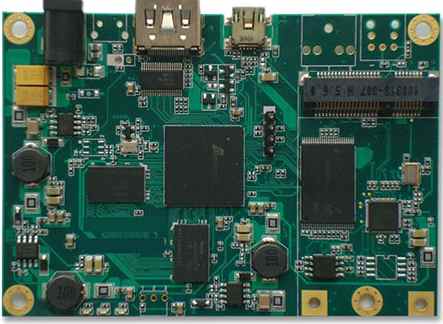
SMT manufacturers share the solution of pad warping
Even the most professional SMT manufacturers can't guarantee that their products are 100% qualified. The problem is not terrible. Just find a solution and solve it in time. Pad warping is a relatively easy problem in SMT processing. Next, kinhfordSMT manufacturer - Electronics will share with you the solution of pad warping.https://www.kingfordpcb.com/yuan.php
Common causes and solutions of pad warping
There are many reasons for the tilt of the pad. Because the position of the pad is below the component, the blind spot of the repair technician may try to move the component, resulting in the tilt of the pad, because he cannot see the solder joint during the operation. Or because the heating temperature is too high, excessive heating and so on leads to this situation.
Solution: Step 1: Clean up the area in need of repair and make sure it is clean.
The second step: remove the failure part, will be the failure of the pad and a small section of wire are removed.
The third step: Use a knife to scrape off the SMT patch processing residue, stains, burn materials, etc.
Step 4: Scrape off solder resistance and coating on the patch processing connection line and clean the area.
Step 5: Add a small amount of flux to the surface of the board, tin. Clean and insert the new BGA pad wire into the original access hole. Remove the solder resistance from the original access hole. Keep the new pad area smooth and grind into the surface slightly if necessary.
Step 6: Cut and trim the new pad.
Step 7: Select appropriate new pad shape bonding nozzle, position PCB, ensure smooth, at the same time after SMT machining positioning, remove the positioning tape.
Step 8: Dip a small amount of liquid flux to weld the connection line of the new pad to the PCB surface circuit, in order to prevent reflux, you can put tape.
Step 9: Apply the mixed resin to the connection line joint.
1. Strength guarantee
▪SMT workshop: We have imported SMT machines and several sets of optical inspection equipment, with a daily output of 4 million. Each process is equipped with QC personnel, who can keep an eye on product quality.
▪DIP production line: We have two wave-soldering machines, among which there are more than 10 old employees who have worked for more than three years. The skilled workers can weld all kinds of plug-in materials.
Quality assurance, cost-effective
▪ High-end equipment can stick precision shaped parts, BGA, QFN, 0201 materials. Can also template patch, loose material hand.
▪ Sample and size batch can be produced, proofing from 800 yuan, batch 0.008 yuan/point, no start-up fee.
3. Rich experience in SMT and welding of electronic products, stable delivery
▪ Accumulated SMT SMT processing services for thousands of electronic enterprises, involving many kinds of automotive equipment and industrial control motherboard. The products are often exported to Europe and the United States, and the quality can be affirmed by new and old customers.
▪ On time delivery, normal 3-5 days after complete materials, small batch can also be expedited on the same day shipment.