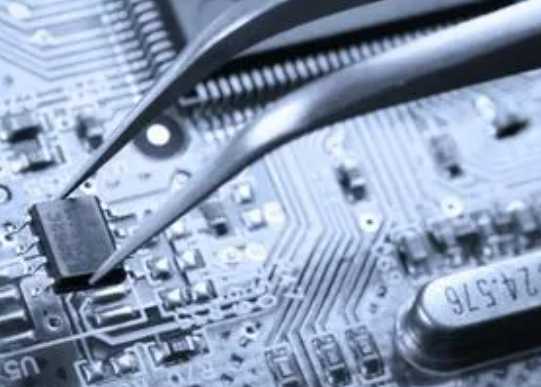
First, the 20H principle
The 20H principle refers to the 20H distance between the power layer and the formation, which is also to suppress the edge radiation effect. The edge of the plate radiates electromagnetic interference. The power layer is shrunk so that the electric field is conducted only within the range of the ground. Effectively improve EMC. If the retraction is 20H, 70% of the electric field can be limited within the grounding edge. The retraction of 100H can contain 98% of the electric field.
The 20H rule is used to ensure that the edge of the power plane is retracted at least 20 times more than the edge of the 0V plane. This rule is often required as a technique for reducing side-shot emission from 0V/ power plane structures (suppressing edge radiation effects).
However, the 20H rule provides significant benefits only under certain conditions. These specific conditions include:
1. The rise/fall time of current fluctuation in the power bus should be less than 1 NS.
2. The power plane shall be located on the internal level of the PCB, and the upper and lower levels adjacent to it are 0V planes. The two 0V planes should extend outward at least 20 times as far apart as the layers between them and the power plane.
3. The power bus structure does not generate resonance at any frequency of concern.
4. The total derivative of PCB should be at least 8 layers or more.
Two, the 3W principle
In PCB design, in order to reduce cross-talk between lines, line spacing should be ensured to be large enough. When line center spacing is not less than 3 times line width, most electric fields can be kept from interfering with each other, which is the 3W rule.
Satisfying the 3W principle can reduce the crosstalk between signals by 70%, while satisfying 10W can reduce the crosstalk between signals by nearly 98%.
Although the 3W principle is easy to remember, it should be stressed that there are prior conditions for the principle to hold. Considering the physical significance of the cause of crosstalk, to effectively prevent crosstalk, the spacing is related to the height of the stack and the wire width. For the four-layer board, 3W is sufficient for the distance between the routing and the reference plane height (5~10mils); However, the height distance between the two layers and the reference layer (45~55mils), 3W May not be enough for high-speed signal routing. The 3W principle is generally held under the condition of 50 ohm characteristic impedance transmission line.
The 3W principle refers to that when multiple high-speed signal lines travel for a long distance, the spacing should follow the 3W principle. For example, clock line, difference line, video and audio signal line, reset signal line and other key circuits of the system need to follow the 3W principle, and not all the wiring on the board should be forced to comply with the 3W principle.
Rogers high frequency board share pcb circuit board temperature is how much
How much is the temperature resistance of pcb circuit board? How to test the heat resistance of pcb circuit board? These are the customers often consult questions, the following to give you a detailed answer.
First: how much is the maximum temperature resistance of pcb circuit board, how much is the temperature resistance time?
The maximum temperature resistance of pcb circuit board is 300 degrees, 5-10 seconds. Over lead-free wave soldering temperature about 260, over lead 240 degrees.
Second: heat resistance test
Previous preparation: PCB production plate tin furnace
1. Sample 5pcs of 10*10cm base plate (or pressed plate or finished plate); "(Copper-containing substrate without bubbling stratification)
Substrate: more than 10cycle
Pressed plate: LOW CTE 150 10cycle and above
HTg material more than 10cycle
Normal material at least 5 cycles
Finished plate:
LOW CTE 150 More than 5 cycles
More than 5 cycles of HTg material
Normal material more than 3 cycles"
2. Set the temperature of tin furnace at 288+/-5 degrees, and adopt contact temperature measurement and correction;
3, soak with a soft brush for flux, apply to the board face, reoccupy crucible 煹 pliers buccal test board into tin stove, timing out 10 SEC after cooling to room temperature, visual presence of foaming board appear, this is 1 cycle;
4. If the problem of bubbling and bursting plate is found visually, immediately stop leaching tin and analyze the initiation point f/m. If there is no problem, continue the cycle until the bursting plate, with 20 times as the end point;
5. It is necessary to slice and analyze the bubbling place, understand the source of detonation point and take pictures.