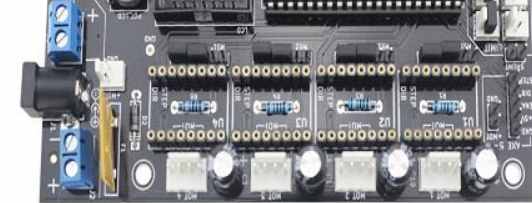
pcba manufacturers must select the PCB board and determine the material type of the board before production, and then the pcba patch processing and production can be carried out. There are many pcba OEM factories, it is necessary to select stable suppliers to ensure the quality of customers' products, so there are many types of boards. kingford takes a look at what flexible printed boards are. There are many types of flexible printed boards with different structural characteristics. According to the specific structure of flexible printed boards, IPC-6013 standard divides them into the following five types. The structural characteristics of different types are as follows.
Type 1: Flexible single-sided printed board, consisting of only one conductive layer, with covering film, with or without reinforcing layer.
Type 2: Flexible double-sided printed board consisting of two conductive layers interconnected by coated through holes, with or without reinforcing layers.
Type 3: Flexible multilayer printed boards, consisting of three or more layers of conductive layers with coated through holes, with or without reinforcing layers.
Type 4: Rigid flexible composite multilayer printed boards consisting of three or more conductive layers interconnected by coated through holes.
Type 5: Flexible or rigid flexible printed board, consisting of two or more conductive layers, without plating through holes.
Among the above five types of flexible plates, if there are too many conductive layers in type 3 plates, the bending performance will be reduced due to the increase of copper foil layer. Therefore, when flexible multilayer plates are really needed in pcba manufacturing, they should be made into the form of pages, so that the number of curved copper foil layers is reduced, which is conducive to bending. Four layers of flexible plate divided into two pages
2. SMT solder joint quality and appearance inspection
With the progress of technology, some electronic products such as mobile phones and tablet computers are developing towards light, small and portable. The electronic components used in smt processing are also getting smaller and smaller. The resistance and tolerance parts of 0402 before have been largely replaced by 0201 size. How to guarantee the quality of solder joint has become an important subject of high precision patch. As a bridge of welding, the quality and reliability of solder joint determine the quality of electronic products. In other words, in the production process, the quality of SMT is ultimately reflected in the quality of solder joints.
At present, in the electronics industry, although the research of lead-free solder has made great progress, has begun to popularize the application in the world, and environmental issues have been widely concerned by people, the soft brazing technology using Sn-Pb solder alloy is still the main connection technology of electronic circuits.
A good solder joint should be in the service life of the equipment, its mechanical and electrical properties do not fail. Its appearance is as follows:
(1) Complete, smooth and bright surface;
(2) The appropriate amount of solder and solder completely cover the welding parts of the pad and lead, and the height of the components is moderate;
(3) Good wettability; The edge of the welding point should be thin, and the wetting Angle between the solder and the pad surface should be less than 300, and the maximum should not exceed 600.
SMT processing appearance inspection contents:
(1) there are no omissions in components;
(2) whether the components are pasted incorrectly;
(3) there is no short circuit;
(4) there is no virtual welding; The reason of welding is relatively complicated.
First, the judgment of virtual welding
1. Use the special equipment of online tester for inspection.
2. Visual or AOI inspection. When it is found that the solder solder solder is too little solder infiltration, or the solder joint in the middle, or the solder surface is convex ball, or solder and SMD do not melt, it is necessary to pay attention to, even a slight phenomenon will cause hidden trouble, should immediately determine whether there is a batch of virtual welding problem. The way to judge is to see whether more pcb solder joints at the same position have problems, such as individual PCB problems, may be the solder paste is scratched, pin deformation and other reasons, such as in many PCB at the same position have problems, at this time is likely to be caused by bad components or solder plate problems.
Two, the reason and solution of virtual welding
1. The design of welding pad is defective. The existence of through-hole welding pad is a major defect of PCB design, less than all must not be used, do not use, through hole will cause solder loss resulting in solder shortage; Pad spacing, area also need to match the standard, otherwise should be corrected as soon as possible design.
2.PCB board has oxidation phenomenon, that is, the welding disc is not bright. If there is oxidation, you can use an eraser to remove the oxide layer, so that its bright return. PCB board damp, if suspected can be placed in the drying oven drying. PCB board has oil stains, sweat stains and other pollution, at this time to clean with anhydrous ethanol.
3. PCB printed with solder paste will be scraped and rubbed, which will reduce the amount of solder paste on the relevant pad and make solder insufficient. It should be made up in time. The method of filling can be dispensed with a little or a bamboo skewer.
4.SMD (table sticker components) quality is poor, expired, oxidation, deformation, resulting in virtual welding. This is a common reason.
(1) The oxidized element is not bright. The melting point of the oxide increases. At this time, it can be welded with more than 300 degrees of ferrochrome and loose flavor flux, but it is difficult to melt with more than 200 degrees of SMT reflow welding and the use of less corrosive no-clean solder paste. Therefore, oxidized SMD is not suitable for reflow welding furnace welding. When buying components, be sure to see if there is oxidation, and buy back to use in a timely manner. Similarly, oxidized solder paste should not be used.