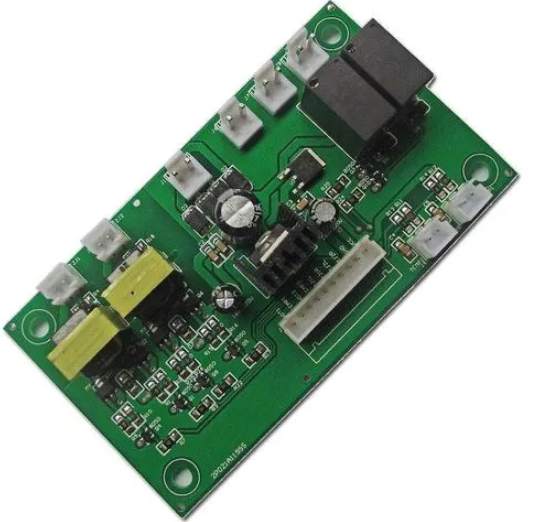
More and more people in the industry are aware of the adverse consequences caused by the poor quality of SMT products. This situation indicates that manufacturers should spare no effort to check their own production procedures and install necessary automatic optical monitoring devices to reduce the loss caused by poor quality. Users' demand for miniaturization of electronic products is increasing. The following post explains how to solve the SMT patch processing quality problems and SMT patch processing quotation how to quote the relevant knowledge.
1. How to quote the SMT SMT processing quotation sheet
One: SMT patch material 2 feet for 1 point; 0402 components are calculated at RMB 0.015 per point, and 0603-1206 components are calculated at RMB 0.015 per point. 1, plug-in material 1 foot for 1 point; According to the calculation of each point is RMB 0.015; 2. 4 feet of socket type are 1 point; According to the calculation that each point is RMB 0.015. 3. Ordinary IC, 4 feet are 1 point; According to the calculation that each point is RMB 0.015 4. Dense foot IC, 2 feet is 1 point; If each point is RMB 0.015, 5. 2 BGA feet are 1 point; The machine stick aniseed is calculated according to the doubling of the volume of components. 7. The additional charge is calculated as 20 Yuan per hour
Ii: In some product delivery plants and processing plants, ie often needs to calculate the product processing fee. How to calculate the SMT processing fee? 1. Understand SMT production process and each process content: feeding - printing paste - patch components - eye inspection - over reflux furnace - ultrasonic washing - cutting - appearance inspection - packaging (some products need ic programming and pcba function test) 2. SMT processing fees are generally calculated by the number of component points. A patch (resistor, capacitor, diode) counts as a point, a triode counts as 1.5 points, ic feet below 50, two feet counts as a point, more than 50 feet of ic4 feet counts as a point, and all pcb patch points are counted. Processing fee = points * the unit price of 1 point (the processing fee includes: red glue, solder paste, washing water and other auxiliary materials) 4. Measuring frame, steel mesh and other fees agreed by both parties shall be calculated separately.
Three: The following is my specific quotation to the company's boss about the mobile phone board SMT patch, you have any suggestions, welcome to put forward! The quotation for the trial production of SMT patches of the new model is ¥10000 for each trial production of the mobile phone board. The trial production quantity is less than 300 pieces. (The mobile phone products tested in *** SMT workshop for the first time are called new models and belong to the trial production stage.) Note: 1. The above quotation is only applicable to the patch trial production stage. 2. The above quotation unit is RMB. 3, the above steel mesh, auxiliary materials, bottom filling and other costs have been included.
Remarks:
1. The above quotation is only applicable to the patch mass production stage. 2. The above quotation unit is RMB. 3. According to the company's existing patch outsourcing processing price, 0402 component is 0.018RMB/ component, and 0603 component is 0.016RMB/ component. 4, IC, connector calculation method is every 4PIN counts a component, BGA calculation method is every 4 balls counts a component. 5. The cost of steel mesh shall be subject to the cost charged by the supplier of steel mesh. If the order quantity of the same product exceeds 100K pieces, it shall be deducted from the patch processing fee. 6. The above quotation is for non-rohs products, and the RoHS products will be increased by 20% on the basis of this quotation. 7. The mass production quantity is less than 350 pieces, and the minimum patch cost is ¥3000 / time; The amount of mass production exceeds 350 pieces shall be calculated according to the above quotation.
2. How to solve the SMT patch processing quality problem
We need and will need smaller, better quality, better performance and more efficient mobile phones, computers, digital cameras and so on. With the need for miniaturization of electronics, we face the challenge of producing products with hundreds of thousands of components that are invisible under normal conditions. The surface mount industry faces the following major challenges: Manufacturers typically assemble tiny components onto tens of thousands of PCB boards, where the component density is extremely high. During the assembly of components, the equipment used by the manufacturer may have occasional or frequent systematic positioning deviations due to a number of factors.
These include: aging; Ability to mount 0402 or 0201 components; Keep the installation and positioning accurate setting problems; Due to the accumulation of debris suction nozzle before the production of 0402 plate; The number of components mounted per hour before performance degradation; Operator's ability to turn over the reel. On top of that, there is the quality of the standard solder. It's enough to understand why the cost of poor product quality is huge. By the time errors are found, it is too late. Some errors are found during online testing, and online testing can catch up to 60% of errors. Many products cannot be tested online due to high assembly density or design characteristics. Other errors are found during functional testing (if such testing is done on the product).
Most of the defects are discovered by consumers. Most of us have either suffered from shoddy products or read in the newspaper about poor quality records and massive returns that would have cost more than a repair. These systematic positioning errors generally occur in the process of component processing, which is caused by the absence of automatic optical detection equipment. Many errors in patch processing cannot be detected with the naked eye. Even testing a board over a period of hours doesn't help. However, the only test used by many countries, including China, is visual inspection. More surprisingly, each tester spent an average of 10 minutes examining a circuit board with more than 400 components. Even if the same inspector was given 40 minutes to examine a larger, simpler board, he would not be able to detect 90% of the problems.
And the problem is not just related to mid - to high-volume SMT. I have noticed similar problems with high mixing-low volume surface mount products. In many cases, fast conversions cause serious problems with SMT processes. In short, if we do not use AOI, we lose a reliable way to guarantee the intrinsic quality of SMT products. Although the image comparison type automatic optical inspection device has a defect and does not support the SMT of medium to high capacity, the parametric automatic optical inspection device can fill the gap. Whether you choose the image comparison model for low volume mount or the parametric model for medium-high volume mount, the manufacturer has the ability to perform 100% AOI-supported tests. Manufacturers' efforts to implement reliable automated optical inspection will not only reduce their own production costs, but also ensure that most consumer products are of high quality. This is the most basic expectation of advanced smt manufacturers in the 21st century