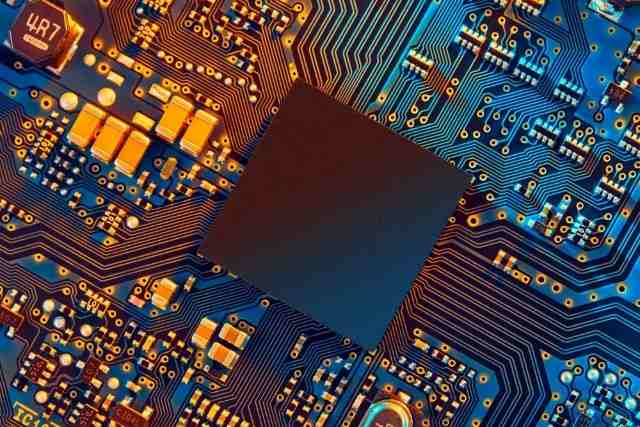
The development of electronic communication products has gone through the stages of 1G, 2G, 3G, 4G and so on, and now it is moving towards the 5th generation of communication products. As the 5th generation of electronic communication, compared with 4G, 5G has undergone great changes in peak rate, spectral efficiency, delay and other aspects, which puts forward new requirements for PCB and copper clad materials. From the perspective of 5G communication terminal products, this paper will put forward the technical requirements for PCB technology, copper clad plate technology, upstream and downstream copper foil, glass cloth, resin and other technologies, so as to provide references for related fields of PCB industry.
I. Analysis of key technical indicators of 5G
5G products will bring you infinite beautiful vision and experience of mobile Internet. Technically speaking, there are many challenges to face. By solving these problems, there will be many technological breakthroughs and improvements.
In the 5G era, there will be a large number of MIMO antenna applications. In Massive MIMO antenna, due to the increase in the number of antenna channels, the number of channels corresponding to each antenna channel in the power amplifier will also increase correspondingly. This change will lead to the increase in the overall power of the power amplifier, which requires the power amplifier to have higher power efficiency. As one of the ways to improve power efficiency, how to reduce the loss of PCB board bearing power amplifier, improve the thermal conductivity of PCB board becomes particularly important.
In addition, due to the increasing number of radiation units in the MassiveMIMO antenna, the hardness of printed circuit board is required to provide better support, and the complexity of circuits increases. Therefore, multilayer antennas will be used more frequently than traditional double-sided PCB antennas.
2. PCB technical requirements and difficulties of 5G communication products
PCB technical requirements for 5G communication
With the trend of miniaturization and increasing capacity of communication products, the design space of product front end is severely squeezed. In order to relieve the design pressure, communication chip manufacturers have to choose to develop IC products with higher speed to meet the needs of large capacity and small volume products. However, as the speed increases, the pressure on signal integrity engineers increases rather than eases. High speed products can be achieved using fewer lines, but the increase in speed directly leads to the strict requirement of signal quality, and the margin becomes less and less. Under 10Gbps signal, the UI of the signal can reach 100ps bit width, but under 25Gbps signal, the bit width of the signal is only 40ps, which means that every link of the channel should be optimized design to strive for each ps margin.
5G communication, as the fifth generation of mobile communication products, has applied a lot of new technologies, but in any case, it can not be separated from the PCB carrier, the requirements for PCB are more and more stringent, especially for PCB substrate materials, processing technology, surface treatment and so on put forward very high requirements.
The increasing working frequency of 5G communication products has brought new requirements for the manufacturing process of printed boards. Millimeter-wave PCB is usually a multi-layer structure, and microstrip line and ground coplanar waveguide circuit are usually located in the outermost layer of the multi-layer structure. Millimeter wave belongs to the extremely high frequency (EHF) range in the whole microwave field. The higher the frequency, the higher the dimensional precision of the circuit is required.
Comparison of PCB process capability requirements of 5G and 4G
Appearance control requirements: The microstrip lines in key areas are not allowed to have pitting and scratching defects, because high-frequency PCB board lines do not transmit current, but high-frequency electrical pulse signals, pits, notches, pinholes and other defects on the high-frequency wire will affect transmission, and any such small defects are not allowed. 2.1.3 Control microstrip antenna corner: to improve antenna gain, direction and standing wave; Avoid the resonant frequency to high frequency deviation, improve the antenna design margin, need to microstrip antenna patch Corner sharpness control (EA), such as ≤20um, 30um, etc. 2.1.4 For single-channel 112G high-speed products, PCB copper-clad materials are required to have lower Dk and Df, new resin, glass cloth and copper leaf technologies are required, PCB process is required to have higher back drilling precision, more strict thickness tolerance control, smaller aperture, etc. 2.1.5HDI high-density technology application: PCB technology requirements for products in the 5G era include second-order HDI technology application, multiple laminating technology, asymmetric design, 0.15mm tiny hole, 0.20mm high-density hole wall spacing, mixed pressing of materials of different systems, etc.
PCB technical difficulties in 5G communication
5G chips require smaller PCB hole spacing, with the minimum hole wall spacing of 0.20mm and the minimum aperture of 0.15mm. Such a high-density layout brings great challenges to CCL materials and PCB processing technology, such as CAF problems and cracks between heated holes.
0.15mm small aperture, the maximum aspect ratio of more than 20:1, how to prevent the problem of broken needle drilling, how to improve the PCB electroplating aspect ratio, to prevent the hole wall without copper, etc., is the PCB process urgent problems.
The pad is warpe
In order to reduce signal loss, high speed PCB is expected to use high speed materials, and the hole ring is as small as possible, from 5.0mil to 3.0mil, but the binding force between high-speed copper foil and resin is lower than that of conventional FR4 material. Then using small hole ring, PCB after reflow or wave soldering, due to thermal stress impact, The defects of warping of pad or cracking of surface PP resin occur, as shown in Figure 2-5. Solution: Rapid development is the trend, the hole ring will be smaller and smaller, in order to reduce the welding pad warping or PP layer cracking defects, it is necessary to optimize the resin flow and pressing process parameters.