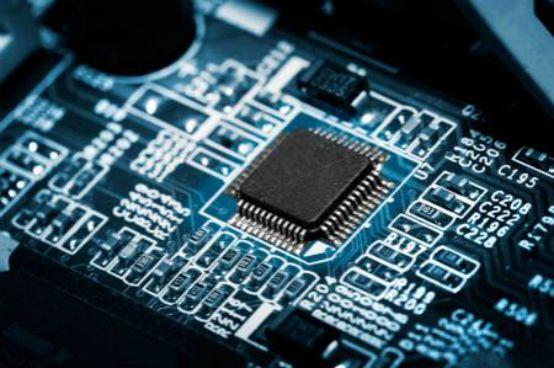
Solder resistance layer and circuit board manufacturing
To fabricate a double-sided PCB board, a dielectric core material is sandwiched between two layers of copper, including a component PAD, a zon-filled copper foil, and a connection line. This basic structure also applies to the layering of multilayer circuit boards, except that the copper and dielectric materials are thinner and do not include the inner PAD. Finally, all of these layers are compacted into a multilayer circuit board, drilled, and the finished board is prepared and sent to the patch process for installation of electronic components (PCB Assembly). However, before the PCB can be sent to the patch, there is another process that must be done to help protect the PCB: applying a coating that impedes welding.
Solder resistance coating is a kind of protective material suitable for the exterior surface of circuit board. The solder resistance coating will cover the entire surface of the board, including metal and dielectric materials, except for the pads and holes to be welded. This covering will protect the board from metal oxidation, corrosion, dirt and even human contact. A weld-coated barrier between two exposed metal areas also helps prevent solder from bridging between open areas and accumulating on the metal surface.
Welding coating materials can be applied to circuit boards through two different processes:
Liquid: Using the screen printing process, welding coating material can be applied directly to the board, which hardens and exposes PAD and drill holes.
Photosensitive material: Welding coating Photosensitive material can be applied as a liquid or can be laid as a dry film. The board is then exposed to ultraviolet light in addition to the pads and holes to be welded. This exposure hardens the solder sensitized material across the board, while the unexposed material on the hole and PAD is washed away.
Resins are commonly used for welding coating materials because they are resistant to high temperature, humidity and solder. Welding coatings are usually green, but other colors can be applied to Oems who wish to use boards of different colors to identify different production steps. For example, a PCB bare board might be red, while green indicates a regular production color. It is also important to apply the welding coating material to the correct thickness to ensure even application and optimal curing. Next, we'll look at patch fenestrations and their role in PCB assembly, and see how it differs from welded coatings.
Image of welding coating in PCB CAD system
Patch fenestration and circuit board components
Wave soldering
There are two main methods for welding components to production circuit boards. The first is wave soldering. This process requires the through-hole component to be inserted into the drill hole and the surface-mounted component to be attached to the plate on the PAD. The PCB board is then passed on a conveyor belt through a machine with a furnace of molten solder. This molten solder rushes up through the borehole in a wave, welding the through-hole parts and forming a welded joint between the PAD and the lead of the surface-mounted element.
Reflow welding
The second process -- called reflow soldering -- is where the pasted PAD is used. The reflow soldering process begins with a layer of solder paste that is deposited on the surface mount PAD to be welded. Solder paste is a material composed of metal solder particles and viscous flux with a putty consistency. The flux not only cleans the welded surface of the sheet and components to be welded, it also acts as an adhesive to hold the parts in place until welded. When passing through the reflow oven tunnel, the solder paste melts and then forms a strong solder joint for its sticky fixing elements to weld securely to the PCB.
There are three main ways to apply solder paste to the circuit board:
Manual: For PCB rework or limited production operations, such as template, the solder paste can be applied manually using a syringe. However, this is a very labor intensive and slow process that is impractical for production runs.
Jet printing: Using a PCB CAD system to patch layer data, solder paste can be deposited on each surface mounting pad on the board using a jet printer. This is a very precise operation, but not necessarily the fastest method of production.
Steel mesh template: For the mass production of circuit boards, manufacturers will use the same PCB CAD system in the PCB layer data to carve out steel mesh template. Steel mesh formwork is usually manufactured by laser and treated with different materials to accurately apply solder paste and long life of steel mesh formwork. Using a silk screen scraper, solder paste can be applied to the circuit board in less than one minute, which is the fastest application method for mass production.
As you can see, the main difference between the solder coating and the patch layer is that the weld cover is the material applied to the circuit board to protect it, and the patch layer is the pattern used to apply the solder paste. Next, we'll look at how to use a PCB CAD system for each system.
PCB design layer: Weld coating and paste mask
PCB CAD systems will use different internal layers to represent Top and Bottom soldered coated Windows and top and bottom patch Windows. Each layer in the CAD system conveys the data needed to make the fenestration, template, or pattern used to apply solder coatings and solder paste to the circuit board.
In the two images above, you can see an example of the green PCB CAD weld coating and the red patch solder paste layer. Note that the solder coating has more data than the patch layer. This is because you see all the drilled, through, and surface mount pads that will be welded, while the patch layer only shows the pads that need to be welded on the surface. The solder coating element defines where the solder coating is not to be applied, while the patch layer element defines where the solder paste is to be applied.
In most cases, the creation of layers for soldering pads and pasting pads in PCB CAD systems is automated. While PCB designers will control the size and shape of the weld coat and patch layer elements, most will choose to make them the same size as the pad or hole on the PCB line. This places the onus on board fabrication and PCB assembly workshops to change the size and shape of any of these elements for PCB manufacturability. However, for those designers who do wish to control PAD elements, this can be done by editing the PCB circuit or running the data through post-processing routines.
Cross section editor in Allegro PCB editor, showing solder paste layer and solder coating
Use PCB CAD layer
Households have complete control over the shape and size of their weld coat and patch layer by using the Pad stack editor. This enables the designer to add, remove, or edit any pad stack element used in the design. In the meantime, you can set the rules governing these elements in the constraint manager. Checking manufacturing and PCB Assembly rules will alert the designer to manufacturability issues, such as insufficient weld coating between fine spacing pads to prevent weld bridging.
Using the correct solder coating with solder paste layer configuration design is done in the cross section editor. In the image above, you can see the design layer stack structure displayed in the editor, including the different PAD layers. These layers can be configured with width and material information to aid in the laminated structure planning of PCB manufacturing.