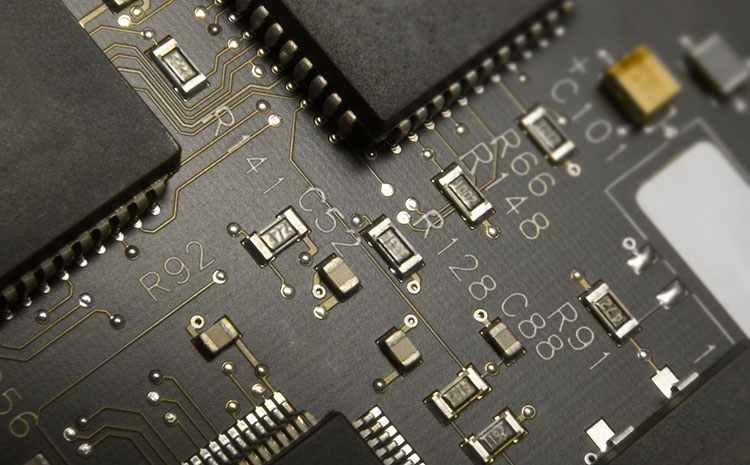
In the electronics manufacturing industry, a pollutant is a variety of surface sediments or impurities and a substance adsorbing or absorbed by the surface that can degrade its performance.
In the first place, these pollutants reduce the quality of circuit board : electronic products made in a polluted environment can cause many problems. Pollution can change the size of electronics, change the cleanliness of surfaces, and cause dented surfaces.
The second, more serious problem is the minor omission in the process. Unwanted chemicals in process steps may change the size of electronic products or the quality of materials.
The biggest concern is the impact of pollution on the reliability of electronics. Small doses of contaminants may enter the electronics during the process without being detected by the usual electronics tests. However, these contaminants can travel inside the electronics and end up in electrically sensitive areas, causing the electronics to fail. This failure mode became a primary concern for the automotive,shipborne, aerospace and defense industries.
The pollutants exist mainly in ionic and non-ionic forms in the environment. Ion-type pollution sources mainly come from process pollution such as PCB board etching, coating, doping, oxidation and solder resistance layer, as well as contact pollution such as component packaging materials, solder paste, flux, equipment oil, personnel fingerprints and environmental dust, manifested in a variety of organic or inorganic acids and salts. Therefore, in the process of manufacturing, it is necessary to strictly control polar ion pollutants.
Ionic pollutant molecules have eccentric electron distribution, easy to absorb moisture, in the air under the action of carbon dioxide to produce positive and negative ions, resulting in product corrosion, cause surface insulation resistance decline, in the presence of electric field conditions will also occur electromigration, dendritic crystallization, resulting in leakage and short circuit. The low surface energy of polar pollutants can also enable them to penetrate the solder resistance layer and grow dendrites under the product surface. Some polar pollutants may also be non-ionic, in the presence of bias voltage, high temperature or other stresses, a variety of electronegative molecules on their own row to form a current.
In the production process of PCB circuit board products, almost all metal elements involved in product manufacturing will be released into various metal particles and metal compounds, forming ammonium, calcium, lithium, magnesium, potassium, sodium and other cations, in addition to a large number of residual "acid ions". Such as chloride ions, bromine ions, weak organic acid ions, sulfate ions, Flux (flux) and other acidic negative ions, these pollutants composed of cations and anions are polar pollutants.
Among them, the metal ions in the metal particles and cations exceed the standard, which is easy to cause insulation reduction of electronic components, capacitance drift and electrical signal interference, and even cause direct short circuit of the electronic circuit. In addition, the active metal particles and metal cations will also replace some of the components of the electronic circuit in the conductive material with low activity of the precious metal to be replaced. Cause the performance of the electronic circuit to degrade.
And pollutants in the negative ions, such as chloride ions mainly from HASL flux resistance, sweat, tap water, welding flux (active or mildly active rosin flux in high, resin or rosin based water-soluble flux and free cleaning flux low), chloride ions and moisture in the water differentiation and formation of ion electrode potential, will cause leakage, erosion and ionization of metal substances.
In the process of Printed Circuit Board, the content of chloride ion is affected by the PCB material. The material condition of the PCB board (including its insulating base and the metal to which it is attached) determines the allowable chloride ion content during assembly. Ceramic mixture substrates or other materials formed on refractory materials, such as lead, are more sensitive to the presence of chloride ions than organic substrates, such as epoxy glass fabric substrates, due to the extent to which the surface integrated distribution has reached the microscopic scale. In terms of the surface metal layer, the nickel/gold surface itself is much cleaner than the lead/tin surface.
The effect of bromine ion is less than chlorine, as a flame retardant in epoxy glass cloth added to solder resistance ink, character ink and some solder resistance residue with bromine as active material. The bromine content is related to the porosity of the sheet or the porosity of the welding layer, so the condition of the sheet or the welding layer reflects the bromine content. The number of high temperature cleaning of the PCB circuit board also plays a role in the bromine content. The size of the effect of bromide is related to the process of the printed board, especially the cleaning of the hot air smoothing solder solder before welding of the assembly.
Like chlorine and bromine, sulfate comes from a variety of processes, including kraft paper, plastics and etching acids. Most of the time, sulfate ions come from the tap water used for rinsing or cleaning.
Meso-sulfonic acid is commonly used in many electroplating processes and is sometimes used as a substitute for active agents in some HASL fluxes. If not sufficiently neutralized or cleaned, its corrosive effect will be many times that of chlorine.