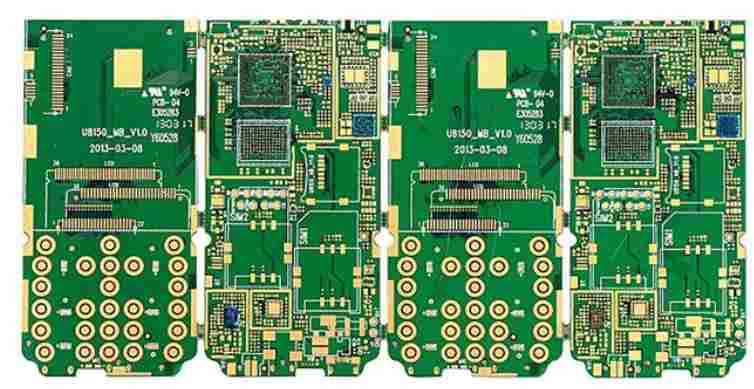
If you are entering the line of PCBA processing plant for more than 4 years of electronic processing manufacturing practitioners, you may have a simple and not perfect cognition of the whole industry, why say so? Because we generally enter the industry in the first 3 years are in a deep cultivation and learning of this position
In the process, it will take at least 4 years to have a comprehensive understanding of the storage and management of components, PCB processing and SMT patches, as well as subsequent testing and inspection, but you may not know some insider!
Today Kingford Xiaobian to share with you about the PCBA processing plant has what unknown insider
1, the recycling of tin slag
SMT patch and DIP plug-in post welding will produce some waste, among which tin slag is the most proportion of a link. In addition, because tin residue itself is harmful to human body, the tin is not the tin needed by our body, and the tin used in the patch processing is mainly tin gold combination
Therefore, the price itself is not cheap. After the tin slag is produced, regular PCBA factories will collect it with special storage containers and store it separately. It is then handed over to a company that specializes in recycling tin residue.
However, in order to save production costs, many PCBA manufacturers will directly return the tin slag to the furnace and use the DIP plug-in for welding. This is something that many companies will do, but will not be openly stated. Being in a factory is also something few people know about.
Kingford always adhere to the "quality is life", for tin slag we adhere to the principle of never recycling, which is our guarantee to customers.
2, the material consumption rate
A lot of customers probably know. Suppose you produce 100 sets of products, generally very standard engineering will give a loss table according to the entire PCBA circuit board BOM list. It will show which material is wearing part and which material is not wearing part. In the wear parts of the material purchase will be more prepared
Some materials, in order to maintain the entire order can be completed on schedule, after all, due to the loss of several materials, the product delivery time can not keep up, it is not advisable.
Therefore, generally experienced customers will prepare this information in advance. In fact, they have already explained their tolerance of loss to PCBA manufacturers with this information. Don't exceed my expectations. If you exceed my delivery date, you won't be able to keep up. Therefore, the manufacturer is also involved in SMT patch processing
Will pay close attention to this matter.
So for those customers who do not mention any requirements, and then encounter an irresponsible factory, and then come to a careless operator, you will wait for the last 100 pieces of the board can complete hand only 90 pieces, the rest is 10 pieces, such as these loss parts to complete, hand welding to
You. So be sure to make clear my requirements to the business or project directly connected with you in PCBA factory before production. You feed the sum does not ask, the final result is not the same!
These are two of the most inside-the-closet stories in PCBA processing.
Kingford focus on the high-quality PCBA order demand of "Multiple varieties, medium and small batch, and short lead time"