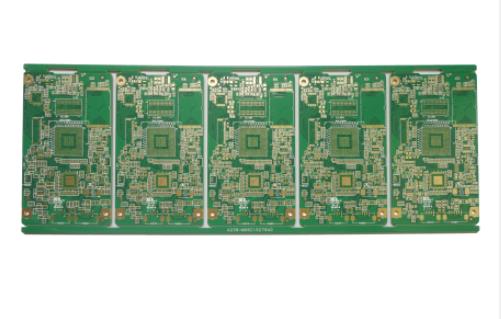
Circuit board manufacturer explains the use of special copper foil of FPC
PCB manufacturers, PCB designers and PCBA manufacturers will explain to you the use of special copper foil of FPC
With the high density and diversification of PCB wiring technology, the standard requirements for material properties are increasing. In order to adapt to manufacturing Fine Pattern by etching, the thickness of copper foil must be thinner and the copper surface must be defect free. Low Profile copper foil should be used for the direction and requirements pursued by multilayer circuit boards, and it has superior mechanical properties when heated at high temperature. However, copper foil used for flexible board or flexible IC carrier plate has different requirements on mechanical properties. Therefore, in addition to meeting new requirements, its original basic characteristics cannot be ignored. Therefore, some special copper foils will appear with the demand of application.
1. Very thin copper foil
Assuming that the Etching speed of the copper foil is constant and the etching factor is also constant, the thinner the copper foil is, the shorter the Etching time will be, and the etching solution will easily be directly driven into the valley to be etched, resulting in the minimization of side erosion, overhang, foot residue and other defects. Therefore, thin foil can be said to be the most appropriate demonstration spokesperson for manufacturing Fine Pattern. 18 of the most commonly used and bulky thin models in the circuit board market μ M copper foil, which has gradually turned to 12 thinner foils μ m、9 μ m、5 μ M development trend.
Thickness less than 9 μ The copper foil of m becomes extremely thin copper foil. This type of copper foil contains a carrier. Generally, aluminum or copper is used as the carrier. When processing and making the copper faced substrate, the carrier is pressed together, and the carrier is removed by Etching or stripping before the circuit board is manufactured. The processing types are divided into Etchable and Pillable.
2. Special copper foil with enhanced mechanical properties
The tensile strength and elongation of copper foil have been described previously. In order to adapt to the existing Class 3 standardized varieties with enhanced elongation in high temperature environment, another copper foil with higher performance has been developed in recent years, called Super HTE. After heating at 180 ℃ for one hour, this Super HTE will undergo recrystallization of metallurgical structure, and has a high elongation of more than 20%. Generally, this phenomenon is only unique to calendered copper, and it is not found in electrolytic copper foil. The application of super malleable copper foil has the following special properties in downstream laminate manufacturing:
(1) Prevent cracking of copper foil under thermal stress
(2) Change in reducing substrate size
(3) Reduce the warpage of two substrates with different thicknesses
Using Super HTE to make FPC also has a high reliability. Because of the low price of electrolytic copper foil and the high mechanical properties of calendered copper foil, Super HTE copper foil has become a new general choice for high-density soft and hard boards.
3. High performance, defect free copper foil
When the copper foil products are provided to the copper foil substrate factory or PCB factory of the downstream industry to make the circuit, it is often found that there are problems in the process products caused by the appearance defects such as copper surface breakage, scar, bump, foreign matter, Pinhole, etc. In order to reduce and avoid the above defects, special attention should be paid to the control of the following problems in the copper foil process:
(1) The air, water, chemicals, mechanical parts and packaging items in contact with the copper foil during the manufacturing process shall be kept clean to prevent the copper foil from being damaged, oxidized and mixed with foreign matters.
(2) In addition to manual visual inspection, the appearance quality inspection is also carried out with CCD automatic appearance inspection machine. In case of any abnormality, it can be handled quickly and effectively, and the record is kept in the product work order.
(3) In addition to improving the quality assurance awareness, the process operators need to cultivate the concept of manufacturing flawless copper foil on a daily basis, and thoroughly implement and maintain the stability of process conditions and control.
The manufacturing process of the copper foil factory is mostly driven roller equipment that is easy to consume. In addition, the raw material of the process is copper sulfate chemical solution that is easy to crystallize and strong acidic. It is a wet process, and a large amount of acid gas occurs. The process is operated continuously day and night, with a daily output of hundreds of thousands of meters. Therefore, it is very difficult to achieve defect free copper foil.
Therefore, the maintenance and improvement of process equipment and operation is bound to invest more energy and R&D funds. As a result, of course, the quality level can be improved, but the relative cost has increased significantly. However, there is not much difference in price due to different grades. In the future, it will also become a major problem and challenge for copper foil manufacturers to meet customers' requirements for the quality of defect free copper foil. PCB manufacturers, PCB designers and PCBA processors will explain to you the use of special copper foil for FPC.