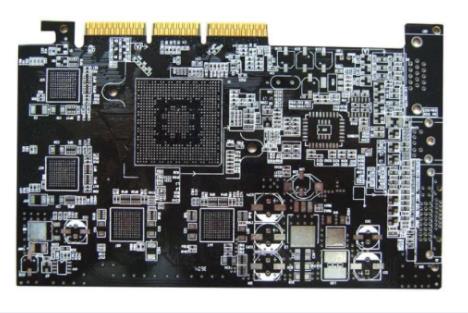
Design skills and key points for realizing efficient automatic routing of PCB boards
Although EDA tools are now powerful, with smaller and smaller PCB size requirements and higher device density, PCB design is difficult In order to solve the design problems and speed up the product launch, many manufacturers now prefer to use special EDA tools to implement PCB boards However, the dedicated EDA tool cannot produce the desired results. It does not implement 1.00% routing, which is a mess. It usually takes a lot of time to complete the rest of the work There are many popular EDA tools and software on the market, but they are the same except for the terms used and the location of function keys How to use these tools to better implement PCB boards? Careful analysis of the design and careful configuration of the tool software will make the design more compliant before starting wiring The following is the general design process and steps
PCB board
1. Determine the PCB board
The board size and wiring layer need to be determined early in the design. If the design requires the use of high-density ball grid array (BGA) components, the low number of routing layers required to route these devices must be considered. The number of routing layers and stacking method directly affect the routing and impedance of traces. The size of the circuit board helps determine the stack and trace width to achieve the desired design effect. For many years, it has been believed that fewer layers are cheaper, but there are many other factors that affect the manufacturing cost of circuit boards. In recent years, the cost difference between multilayer boards has been greatly reduced. Design from more circuit layers and distribute copper evenly to avoid being forced to add new layers when a small number of signals do not meet the defined rules and space requirements until the end of design. Careful planning before design will reduce a lot of trouble in cabling.
2. Design rules and restrictions
The auto routing tool itself does not know what to do. To complete the routing task, the routing tool needs to work within the correct rules and constraints. Different signal lines have different wiring requirements. All signal lines with special requirements need to be classified, and different design classifications are also different. Each signal category should have a priority. The higher the priority, the stricter the rules. Rules related to trace width, number of vias, parallelism, interaction between signal lines, and layer limits have a great impact on the performance of routing tools. Careful consideration of design requirements is an important step for successful cabling.
3. Layout of components
To simplify the assembly process, the design for manufacturability (DFM) rules constrain the layout of components. If the assembly department allows parts to move, the circuit can be properly optimized for automatic wiring. The rules and constraints you define affect the layout design. The routing channel and through-hole area shall be considered in the layout. These paths and areas are obvious to the designer, but the automatic routing tool only considers one signal. By setting the routing constraints and the layers that signal lines can route, the routing tool can operate according to the designer's imagination. Complete wiring.
4. Fan out design
In the fan out design stage, in order to allow automatic wiring tools to connect component pins, surface mounted devices should have at least one through-hole for each pin, so that when more connections are needed, boards can be connected between layers. Connection, On Line Testing (ICT) and circuit reprocessing. In order to make the automatic routing tool efficient, make sure to use the size of through-hole and trace as much as possible, and the ideal interval is set to 50 mils. The type of through-hole to use to make the number of routing paths available. When designing fan out, consider the problem of in circuit test. Test fixtures can be expensive and are usually ordered near full production when it is too late to consider adding nodes to achieve 100% testability. After careful consideration and prediction, the design of in circuit test can be carried out at the early stage of the design and realized at the later stage of the production process. The type of through hole fan out is determined according to the wiring path and the test in the circuit. Power and grounding also affect cabling and fan out design. In order to reduce the inductive reactance generated by the connecting line of the filter capacitor, the through-hole should be as close as possible to the pin of the surface mounted device. If necessary, manual wiring can be used, which may affect the originally envisaged wiring path, or even cause you to reconsider which through-hole to use. The relationship between the through-hole and the lead inductance must be considered, and the through-hole specification must be given priority.
5. Manual wiring and processing of key signals
Although this paper mainly discusses automatic routing, manual routing is an important process in PCB design. The use of manual routing can help the automatic routing tool to complete the routing work. As shown in Figures 2a and 2b, the path that can be followed in the automatic routing process can be formed by manually routing and fixing the selected network. Regardless of the number of critical signals, please route these signals manually or using automatic routing tools first. Critical signals usually require careful circuit design to achieve the desired performance. After the wiring is completed, the relevant engineers will check the signal wiring, which is much easier. After the check is passed, the wires are fixed and the automatic wiring of the remaining signals starts.
6. Automatic wiring
The wiring of key signals needs to consider the control of some power parameters during the wiring process, such as reducing the distributed inductance and EMC. The wiring of other signals is similar. All EDA suppliers provide methods to control these parameters. After understanding the input parameters of the automatic routing tool and the influence of the input parameters on the routing, the quality of automatic routing can be guaranteed to a certain extent. General rules shall be used for automatic signal routing. By setting constraints and no wiring areas to limit the number of layers and vias used for a given signal, the wiring tool can automatically route according to the design idea of the engineer. If there is no limit to the number of layers and vias used by the auto route tool, each layer will be used during auto route and many vias will be created. Once the constraints are set and the created rules are applied, the automatic routing will achieve similar results as expected, although some sorting may be required to ensure the space for other signals and network routing. After a part of the design is completed, fix it to protect it from the influence of the subsequent wiring process. Use the same procedure to route the remaining signals. The number of traces depends on the complexity of the circuit and the number of general rules you define. After completing each type of signal, the restriction on the remaining network routes is reduced. But then comes a large number of signal routing that requires manual intervention. Today's automated routing tools are very powerful and can usually complete 100% routing. However, when the automatic wiring tool does not complete the wiring of all signals, the remaining signals need to be manually wired.
7. Key points of automatic wiring design include:
7.1 Change the setting slightly and try various paths for wiring;
7.2 Keep the basic rules unchanged, try different wiring layers, different printing lines and spacing widths, different line widths, and different types of through-hole, such as blind through-hole, buried through-hole, and observe how these factors affect the design results;
7.3 Let the routing tool handle these default networks as needed;
7.4 The less important the signal is, the more free the automatic wiring tool is.
8. Wiring layout
If the EDA tool you are using can list the wiring length of signals, please check this data. You may find that some signals with few constraints have very long wiring lengths. This problem is relatively easy to handle. Manual editing can shorten the signal wiring length and reduce the number of vias. In the sorting process, you need to determine which cabling is reasonable and which is unreasonable. Like manual routing designs, automatic routing designs can also be organized and edited during the review process.
9. Circuit board appearance
In the past, the design often focused on the visual effect of the circuit board, but now, the situation is different The PCB designed automatically is not as beautiful as manual design, but it meets the specified requirements in terms of electronic characteristics, ensuring the integrity of the design
The above is the explanation given by the editor of pcb circuit board company. If you want to know more about PCBA, you can go to our company's home page to learn about it. In addition, our company also sells various circuit boards,
High frequency circuit board and SMT chip are waiting for your presence again.