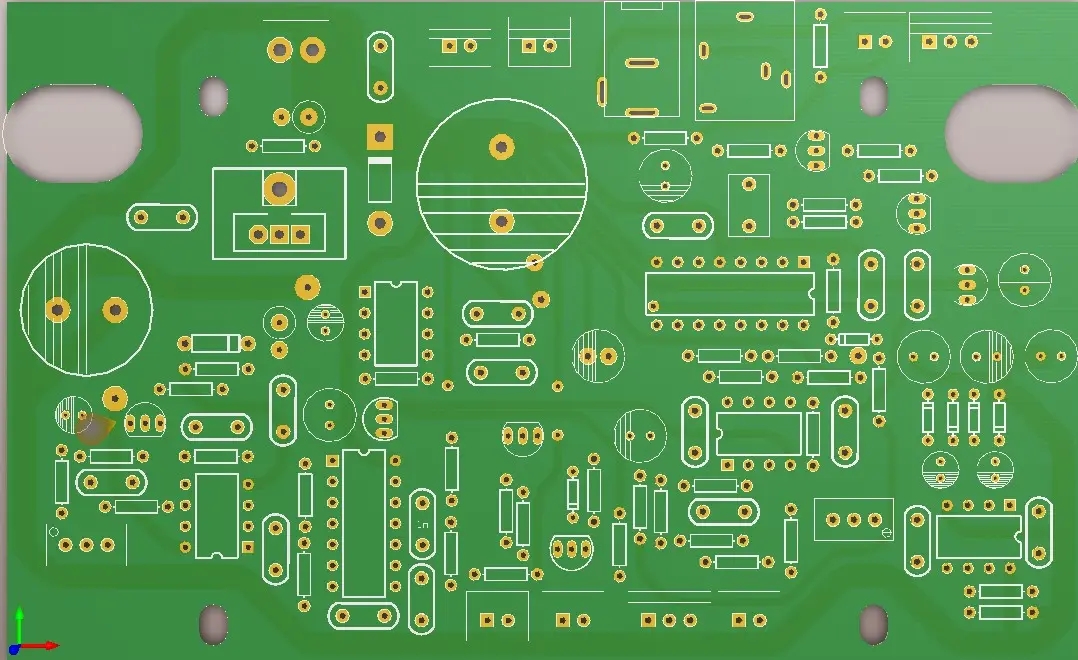
Rust on PCB: What's the problem?
When PCBA is returned due to corrosion, the analyst needs to find the pollution source that causes corrosion in order to eliminate it.
Contamination can come from a variety of sources, such as manufacturing operations, packaging, installation, and the environment. There are many methods that can be used to determine the composition of pollutants. Once its composition is known, possible sources can be identified. In this paper, an example is given to illustrate the process used by analysts to identify the source of PCBA contamination.
When the printed circuit board assembly (PCBA) is returned due to corrosion, the analyst needs to find the pollution source that causes corrosion in order to eliminate it. Contamination can come from a variety of sources, such as manufacturing operations, packaging, installation, and the environment.
There are many methods that can be used to determine the composition of pollutants. Once its composition is known, possible sources can be identified.
Element identification
The corrosion area was imaged using scanning electron microscope (SEM). SEM is usually equipped with an energy dispersive X-ray detector (EDX) to determine the element composition of the sample. The EDX system cannot determine whether there is chemical combination between the two elements, but it knows which elements exist, so that we can learn about the chemical composition.
The solder mask (blue spectrum) contains silicon (Si), which is used to control the viscosity of liquid solder mask before curing. It also contains barium (Ba) and sulfur (S), which are combined to form barium sulfate and used as flame retardants. All these elements are expected to be included in the solder mask, as shown by the blue spectrum.
The contaminated area contains copper (Cu) and chlorine (Cl), which cannot be found in the solder mask. Copper comes from copper conductor, which has been etched and chemically removed from the metal conductor and is now deposited on the solder mask. Chlorine is a pollutant that should not exist on PCBA.
Chlorine can be found in many places in the environment - salt contains chlorine, and many chemicals used to make PCBA also contain chlorine. However, these chemicals should not be the source of chlorine because they will be washed away during the PCBA manufacturing process. No chlorine is found in the solder mask sample, so the manufacturing process of PCBA can be ignored.
Chlorine is used throughout the welding process - chlorinated compounds are added to the flux to promote good solder bonding. These compounds can quickly remove any oxide layer on the copper to achieve a good solder joint. However, during the transition from eutectic solder to RoHS compliant solder, the type of flux used was also changed. Instead of chlorinated rosin flux, a low solid content flux containing organic acid is used to clean the copper surface to realize welding. During welding, organic acids are usually decomposed into harmless products due to heating. These PCBAs were manufactured after the introduction of RoHS compliant solders, and were made using organic fluxes with low solid content.
Corrosion is isolated in only one area of PCBA. If chlorine is present in salt water mist or chlorine vapor in the air, chlorine will be present in the entire PCBA. Chlorine is used in various industrial processes (as well as swimming pools), resulting in the presence of chlorine and chlorinated compounds in the air in these areas.
Through visual inspection of PCBA, it was found that several components near the corrosion area had been reworked. Visual inspection shows that the flux residue is not from organic acid flux with low solid content.
These rework locations were inspected using SEM's EDX system and found chlorine in the flux residue. The chlorine contained in the flux indicates that the old activated flux was used during the rework of components. Then the source of this flux was found in the assembly workshop and eliminated as a corrective measure - there was a bottle of old liquid flux in one repair station that had not been removed from the factory.
If the chlorine is not traced back to the flux used in the rework process, the necessary corrective measures may not be taken, but may be taken in several possible places to eliminate the pollution. In this particular case, the activated rosin flux is a retention of the previous process and has not been removed from this repair station. Other measures to eliminate pollution will be ineffective. Corrective measures must be based on the evidence collected during the investigation. If the chlorinated flux is eliminated by shotgun approach, the problem cannot be eliminated because the bottle of flux may not be found in a single repair station.
How does EDX work?
In the sample, when the electron changes its energy and fills the vacancy in the atom, the EDX system will capture the X-ray generated by it. It calculates the number of X-rays captured at each energy level. Each electron around the nucleus of an atom has a specific energy, which varies from element to element. Because these energies are different, the atomic composition of the sample can be determined.
The electrons emitted by SEM to the sample will interact with the electrons of each atom. In some cases, this interaction will cause the electrons of the atom to escape from the atom, leaving a vacancy. If the atom has a second electron with higher energy to fill this vacancy, it must release a certain amount of energy. The energy released will be in the form of X-rays of specific energy or wavelength. By capturing and measuring these X-rays, a list of existing elements can be summarized. The software of EDX system will display the data on the chart - the energy of X-ray will be displayed on the horizontal axis, and the calculated amount of X-ray will be displayed on the vertical axis.