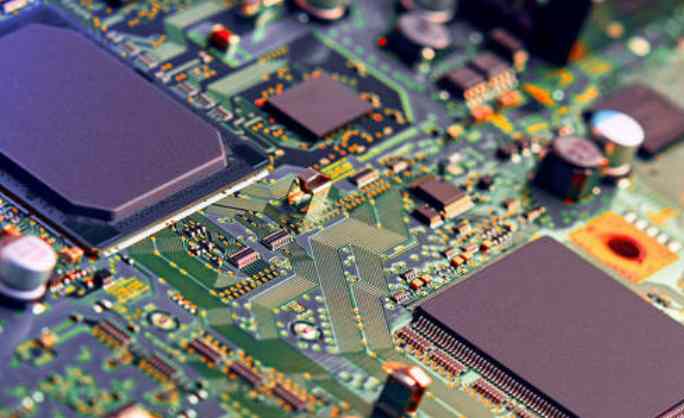
Bad solder joints that need to be repaired are a complex subject. First of all, it must be determined that the design is poor, weldability problems, ineffective solder material, or processing and equipment problems. In addition, many considered poor solder joints, in fact, there is no problem, but too many widely recognized inspection standards, the wrong emphasis on the beauty of the solder joints and ignore its function. In view of some problems, we do the following discussion: Introduction to problem solving When a problem occurs, the first thing that must be checked is the basic conditions of the manufacturing process, which we classify as the following three factors:
1. Material problem:
These include solder chemical materials such as flux, oil, tin, cleaning materials, as well as PCB coating materials such as anti-oxidation resins, temporary or permanent anti-solder inks and printing inks.
2.Poor solderability:
This involves all solder surfaces, such as parts (including surface-attached parts /SMT parts), PCBS and electroplated through holes, which must be taken into account.
3. Deviation of production equipment:
Including machine equipment and maintenance deviations and external factors, temperature, conveyor belt speed and Angle, and depth of immersion, etc., are variables that have a direct relationship with the machine. In addition, other factors such as ventilation, reduction of air pressure, and changes in voltage must also be included in the scope of analysis.
Micro components electronic product category market
The demand of the application market has promoted the continuous expansion of the market for various miniature connector products. PCB connectors, FPC connectors, circular connectors: rectangular connectors, IC sockets, coaxial connectors, etc., have been miniaturized to varying degrees. Among them, the micro-I products of PCB and IC socket connectors will grow fastest.
PCB connectors are mostly used for in-machine wiring, with the increasing portability of electronic equipment, the whole factory on their miniaturization requirements are increasing in 1994 the world connector product market, PCB connectors to 6.713 billion US dollars ranked first, according to forecasts. PCB microplastic connector has great potential for development, due to the extremely fierce competition in the PCB connector market, the price has dropped significantly, the price of IIII micro PCB connector is relatively stable, and manufacturers i are strengthening the development of high-end micro PCB connectors. Recently, the United States and Japan have mass-produced 0.8mm spacing
0.5mm PCB connector products, including the world's largest PCB connector supplier Taiwan, including Asian countries are also developing in this regard.
IC socket is also the focus of manufacturers to develop micro products, microprocessor competition is fierce, chip upgrading, SPAM, DRAM, VRAM and other memory IC growth, have promoted the development of micro IC socket, at present, the number of integrated circuit packages is gradually increasing, lead spacing reduction. There have been very large scale integrated circuit sockets with more than 2000 cores in foreign countries. The DIP socket with a center distance of 2.54 mm has been replaced by a PLCC socket with a center distance of 1.27mm, and the PQFP socket with a pitch of 0.635mm is increasingly widely used. There is also a new type of LGA socket. Because it is a needle-free ceramic grid array, the contact part is not a needle but a disk, and it does not need to be welded to the PCB. Therefore, small spacing can be achieved and suitable for surface installation.
New trend of PCB inspection Non-contact visual inspection has broad prospects
In recent years, with the development of communications, computers, consumer electronics and other industries, the printed circuit board (PCB) industry as the main components of these industries have also developed rapidly. According to relevant statistics, the global PCB output value accounts for about 20% of the total output value of electronic components, and China as a manufacturing and raw material processing country, the output value and output are ranked first in the world.
Printed circuit board (PCB), as one of the most basic and active industries in the electronics industry, is developing rapidly. However, at the same time of rapid development, the PCB industry is facing severe challenges, because the quality of the printed circuit board depends on the quality of each line and each hole on the printed circuit board, and any one of the thousands of lines and holes on a board is too thin, too thick, incomplete, pinhole adhesion, disconnection, dislocation will affect the quality of the product. Therefore, in the production process, how to minimize the scrap rate and how to improve the quality of printed circuit boards has been the unremitting pursuit of major circuit board manufacturers.
In the traditional circuit board inspection process, manual inspection means are usually used, the detection accuracy of this means is easily restricted, and it is easy to cause secondary damage in the detection. More and more manufacturers need a new high-speed and efficient online inspection means to complete the detection of PCB boards.
At present, some manufacturers use non-contact machine vision inspection method for PCB board inspection, this technology because of the high speed and high precision of non-contact measurement and detection, has been trusted by these manufacturers, it can be predicted that in the near future, the use of machine vision technology for PCB board inspection will become the first choice for manufacturers.