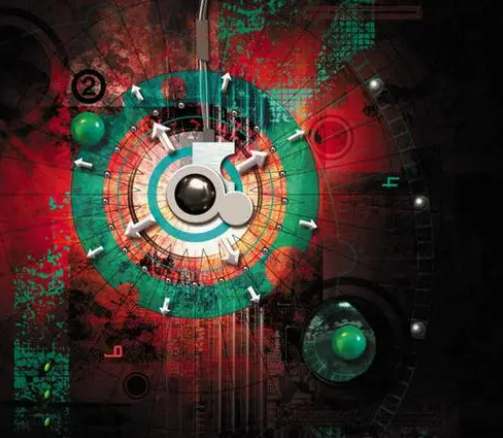
There are many kinds of surface treatment processes for PCB circuit boards, common are hot air leveling, organic coating (OSP), electroless nickel plating/gold dipping, silver sinking, tin sinking, etc. The following Jingbang circuit board manufacturer Xiaobian for you to introduce one by one, so that you can clearly understand the differences of these surface treatment processes.
1, hot air leveling
Hot air leveling, also known as tin spraying, is a commonly used treatment process for early PCB boards. It is a process in which molten tin lead solder is coated on PCB and heated compressed air is used to flatten (blow flat), so that it forms a coating layer that is resistant to copper oxidation and can provide good solderability. The solder and copper form copper tin gold compounds at the joint of hot air polishing, the thickness of which is about 1 ~ 2mil.
2, OSP organic coating
OSP process is different from other surface treatment processes. It acts as a barrier layer between copper and air. Simply put, OSP is a chemically grown organic skin film on a clean, bare copper surface. This layer of film has anti-oxidation, heat shock, moisture resistance, mainly used to protect the surface of copper in the normal environment no longer rust; At the same time, it must be easily removed by flux quickly in the subsequent welding high temperature for welding. OSP process is simple, low cost, widely used in PCB manufacturers.
3, electroless nickel plating/gold leachin
Electroless nickel plating/gold leaching is not as simple as OSP process, which requires a thick layer of coating on the copper surface. Unlike OSP, which is only used as a rust barrier layer, nickel gold alloy with good electrical properties can protect the PCB for a long time and achieve good electrical properties. In addition, it also has the environmental tolerance that other surface treatment processes do not have, effectively prevent PCB board damage.
4. Sink silver
The silver sinking process is simple and fast, which is between OSP and electroless nickel plating/gold leaching. Silver does not need to cover the PCB board with a thick coat of armor. It can also provide good electrical properties and maintain good solderability in hot, wet and polluted environments. The disadvantage is that it will lose luster. In addition, sunken silver also has good storage, usually placed a few years assembly will not have a big problem.
5. Sinking tin
Because all solder is currently based on tin, so tin layer can be matched with any type of solder, which also makes tin sinking process has a good prospect for development. When the tin sinking process was not perfect before, tin whisker was easy to appear on PCB board after tin sinking, and tin whisker and tin migration in the welding process would bring reliability problems. Now, organic additives are added to the tin solution, so that the tin layer structure is granular structure, overcome the problem of tin whiskers, but also has good thermal stability and solderability, enhance the applicability.
The direction of PCB design should be paid attention to
The direction of resistance and diode placement in pcb layout:
pcb design is divided into two kinds: flat and vertical:
(1) Flat: when the number of circuit components is not much, and the size of the circuit board is larger, it is generally better to use flat; For the resistance below 1/4W flat, the distance between the two pads is generally taken 4/10 inch, and for the resistance of 1/2W flat, the distance between the two pads is generally taken 5/10 inch; Diode flat, 1N400X series rectifier, generally 3/10 inch; 1N540X series rectifier tube, generally 4 to 5/10 inch.
(2) Vertical placement: When the number of circuit elements is large and the size of the circuit board is not large, the vertical placement is generally adopted in the pcb design. When the vertical placement, the spacing between two pads is generally taken 1 ~ 2/10 inch.
2. Wiring direction:
From the perspective of the welding surface, the arrangement orientation of the components should be consistent with the schematic diagram as far as possible, and the wiring direction should be consistent with the wiring direction of the circuit diagram. Because various parameters are usually detected in the welding surface during the production process, it is convenient to do so for inspection, debugging and maintenance in the production (note: it refers to the premise of meeting the requirements of circuit performance and the installation of the whole machine and the layout of the panel).
3. Each component arrangement, distribution should be reasonable and uniform, strive to neat, beautiful, rigorous structure of the process requirements.
4. Layout directions of incoming and outgoing terminals
(1) The distance between the two leads should not be too large. Generally, it is about 2 ~ 3/10 inches.
(2) The end of the inlet and outlet line should be concentrated on 1 to 2 sides as far as possible, not too discrete.
5 Potentiometer: IC seat placement principle
(1) potentiometer: used to adjust the output voltage in the voltage regulator, so the design of potentiometer should be full of clockwise adjustment when the output voltage rises, counterclockwise regulator section when the output voltage decreases; In the adjustable constant current charger potentiometer used to adjust the size of the charging current fold, the design of potentiometer should be full clockwise adjustment, the current increases. Potentiometer position xuan should be full in the machine structure installation and panel layout requirements, so it should be placed on the edge of the plate as far as possible, rotating handle outward.
(2)IC seat: the design of printing board, in the use of IC seat under the occasion, we must pay special attention to the positioning slot on the IC seat position is correct, and pay attention to the IC foot position is correct, such as the first foot can only be located in the lower right corner of the IC seat line or the upper left corner, and close to the positioning slot (from the welding surface).
6. When designing wiring diagram, minimize turning and strive for simple and clear lines.
7. Wiring strip width and line spacing should be moderate, capacitor two pad spacing should be as far as possible and capacitor lead pin spacing;
8. When designing the wiring diagram, pay attention to the pin arrangement sequence, and the spacing of component feet should be reasonable.
9. Under the premise of ensuring the performance requirements of the circuit, the design should strive to reasonable wiring, less use of external crossover wire, and according to certain smooth charging requirements of the wire, and strive to intuitive, easy to install, height and maintenance.
10. The design should be carried out in a certain sequential direction, such as from left to right and from top to bottom