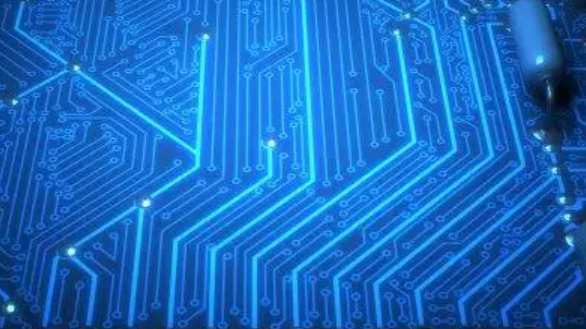
In the design of multi-layer PCB, the number of PCB layers depends on the complexity of the circuit board, from the PCB processing process to consider, multi-layer PCB is a number of "double panel PCB" through the stacking, pressing process to manufacture, but the number of layers of multi-layer PCB, the stacking sequence between the layers and the board selection is determined by the circuit board designer. This is known as "PCB cascading design".
As the saying goes, the best practice is also based on theoretical knowledge. In this section, Banermei focuses on sharing theoretical knowledge about the concept of PCB laminated design and suggestions on the design of laminated structure.
A, PCB stacked composition
The layer Settings in the PCB design file include the following: screen printing layer, solder resistance layer, wiring layer, plane layer.
SilkScreen: Physical layer where device description information and board name identification are placed on PCB board.
Soldermask: Soldermask is an important part of PCB, which mainly plays the role of welding prevention and environmental protection. Soldermask is a layer of ink attached to the surface of PCB. Its role is to cover the PCB area that does not need welding, prevent tinning, and protect the line from external damage to a certain extent.
Conductor: A physical layer that connects components of a PCB board in positive mode.
Plane: It is the physical layer that realizes the PCB board's power supply, ground network connection and provides impedance reference and return path.
2. Suggestions for the design of layered structure
Usually refers to the "cascade design", in fact, is the layout of the wiring layer, the plane layer of the design.
1. PCB lamination is recommended as Foil method.
2. As far as possible, reduce the use of PP sheet and CORE type and type in the same layer (no more than 3 PP layers per layer of media).
3, the thickness of PP medium between the two layers should not exceed 21MIL (thick PP medium processing is difficult, generally add a core plate to lead to the increase of the actual number of layers, thus increasing the processing cost).
4, PCB outer layer (Top, Bottom layer) generally choose 0.5OZ thickness copper foil, the inner layer generally choose 1OZ thickness copper foil.
General according to the size of the current and wire thickness to determine the thickness of copper foil, such as the power board generally use 2-3OZ copper foil, ordinary signal board generally choose 1OZ copper foil, fine wire may also use 1/3QZ copper foil to improve the yield; At the same time avoid the inner layer using two copper foil thickness inconsistent core plate.
5. The distribution of wiring layer and surface layer of PCB board shall be symmetrical up and down from the overlapping center line of PCB board (including the number of layers, distance from the center line, copper thickness of wiring layer and other parameters).
Note: PCB stacking method shall adopt symmetrical design. Symmetrical design refers to the thickness of insulation layer, type of semi-cured sheet, thickness of copper foil, pattern distribution type (large copper foil layer, line layer) relative to the center line of PCB as far as possible.
6. The design of line width and medium thickness should have sufficient margin to avoid design problems such as SI caused by insufficient margin.
In a small number of PCB designs, wiring is adopted in the ground plane layer of the power supply or in the wiring layer of the power supply and ground network. For this mixed type of layer design, it is uniformly called the signal layer.
Introduction to salt spray test methods for PCB circuit boards
1. Test purpose: As PCB may be used in sea or seaside areas with high salinity in the air, its function will be affected due to poor salinity resistance, and serious accidents will be caused. Salt spray test will be conducted to verify whether the product has corrosion appearance. The salt spray test is divided into neutral salt spray (NSS), acetic acid spray (AASS), copper accelerated acetic acid spray (CASS) test, etc. The neutral salt test is suitable for metal coating, organic coating, etc. The other two kinds are suitable for decorative coating such as copper + nickel + chromium.
2. Reference standards
Basic environmental testing procedures for electrical and electronic products Test Ka: salt spray test method;
2.2 GJB150.11-1986 Environmental test methods for military equipment salt spray test;
2.3GB /T 6461-2002 Pattern of metal and other inorganic overlays on metal base bodies after corrosion tests and grade of test pieces;
2.4 ISO14993-2001 Corrosion of metals and alloys -- accelerated testing involving cyclic exposure to salt mist," dry” and“wet” condition
3. Test method for neutral salt spray:
A solution containing 5%+/-0.1% sodium chloride is prepared in distilled or deionized water with a conductivity not exceeding 20µs/cm at a PH of 6.5-7.2,
In the temperature of 35+/-2 degrees, humidity above 85%, with pressure 0.7-1.8kgf/cm2, spray volume 1.0-2.0ml/80 cm2/h continuous spray for 24 hours (with
The body time shall be specified by the customer), the samples in the salt spray tank shall be placed at a 30 degree Angle, and the samples shall be removed from the salt spray tank within 30 minutes after the end of the test.
In order to reduce the loss of corrosion products, the sample should be dried in indoor air for 0.5h to 1h. Then use clean running water with a temperature of no more than 35℃
The test sample will be carefully washed to remove residual salt spray solution on the sample surface, followed by a pressure of not more than 200Kpa at a distance of 30cm from the sample
Air dry and check the sample
4. Result judgment
A. Appearance:
B. Corrosion rating
The corrosion rating is based on the percentage of the total area of the sample with corrosion defects, as shown in the following table:
If Rp=10, you can pass directly
Rp=7-9 If the customer has no special requirements, we can make concessions to receive
Rp=3-6 Needs to be evaluated by relevant departments and judged according to the evaluation results
Rp=0-2 Disqualified