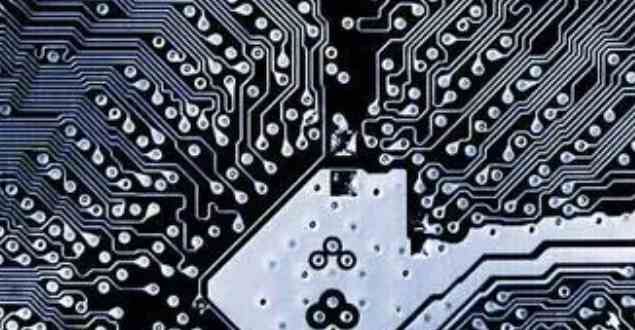
The design performance of multi-substrate is mostly similar to that of single or double substrate, that is, care should be taken to avoid crowding too many circuits into too small a space, resulting in unrealistic tolerances, high inner capacity, and possibly even compromising product quality safety. Therefore, the performance specification should consider a complete evaluation of the thermal shock, insulation resistance, welding resistance, etc. of the inner line. The following describes the important factors to be considered in the design of multi-substrate.
First, mechanical design factors
Mechanical design includes the selection of appropriate plate size, plate thickness, plate stacking, inner copper cylinder, aspect ratio, etc.
1. Board size
Board size should be optimized based on application requirements, system box size, board manufacturer limitations and manufacturing capabilities. Large boards have many advantages, such as fewer substrates, shorter circuit paths between many components, allowing for higher operating speeds, and more input/output connections per PCB board, so large boards are preferred in many applications, such as personal computers, where larger motherboards are seen. However, it is difficult to design signal line layout on large PCB boards, requiring more signal layers or internal wiring or space, and heat treatment is more difficult. Therefore, the designer must consider various factors, such as standard plate size, manufacturing equipment size, and manufacturing process limitations. Some guidelines for the selection of standard printed circuit/board sizes are given in 1PC-D-322.
2. Plate thickness
The thickness of the multi-substrate is determined by a variety of factors, such as the number of signal layers, the number and thickness of the power supply boards, the aspect ratio of the aperture and thickness required for quality drilling and plating, the length of the component pins required for automatic insertion, and the type of connection used. The thickness of the entire circuit board is composed of conductive layer, copper layer, substrate thickness and prepreg material thickness on both sides of the PCB board. It is difficult to obtain strict tolerances on synthetic multi-substrate, and a tolerance standard of about 10% is considered reasonable.
3, the layer of the board
In order to minimize the chance of PCB board distortion and obtain a flat finished board, the layering of the multi-substrate board should be kept symmetrical. That is, it has an even number of copper layers and ensures that the thickness of the copper and the copper foil pattern density of the plate layer are symmetrical. Usually the radial of the construction material used for laminating (e.g., fiberglass cloth) should be parallel to the sides of the laminate. Because the laminates shrink radial after bonding, the layout of the circuit board will be distorted, showing flexibility and low spatial stability.
However, the warping and distortion of the multi-substrate can be minimized by improving the design. The warping and warping can be reduced by evenly distributing the copper foil on the whole layer and ensuring the structural symmetry of the multi-substrate, that is, ensuring the same distribution and thickness of the prepreg material. Copper and roller laminates should be made from the center layer of the multi-substrate up to the outermost two layers. The minimum distance (dielectric thickness) between the two copper layers is 0.080mm.
As a rule of thumb, the minimum distance between the two copper layers, that is, the minimum thickness of the prepreg material after bonding, must be at least twice the thickness of the embedded copper layer. In other words, two adjacent layers of copper, if each layer is 30μm thick, the prepreg material is at least 2(2x30μm) =120μm thick, which can be achieved by using two layers of prepreg material (a typical value for glass fiber weaving is 1080).
4. Inner copper foil
The most commonly used copper foil is 1oz (1oz per square foot surface area). However, for dense PCB boards, whose thickness is extremely important and requires strict impedance control, such PCB boards need to be used
0.50z copper foil. For the power layer and ground, the best choice of 2oz or heavier copper foil. However, etching heavier copper foils results in reduced controllability and does not easily achieve the desired line width and spacing tolerances of the pattern. Therefore, special processing techniques are required.
5. Holes
The diameter of the plated through-hole is usually kept between 0.028 0.010in, depending on the size of the component's pin diameter or diagonal, which ensures adequate volume for better soldering.
6. Aspect ratio
Aspect ratio is the ratio of the thickness of the plate to the diameter of the hole. 3:1 is generally considered the standard aspect ratio, although a higher aspect ratio like 5:1 is also commonly used. Aspect ratio can be determined by drilling, slag removal or corrosion back and electroplating. When maintaining the aspect ratio within the producible range, pass holes should be as small as possible.