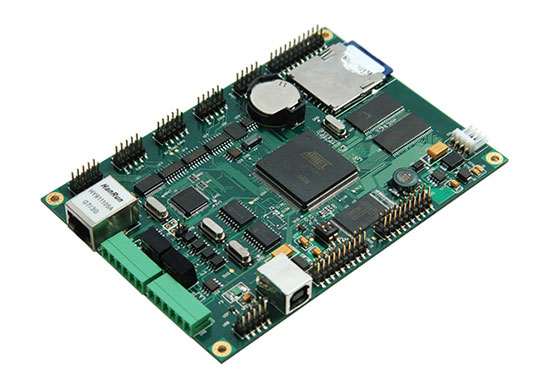
During SMT patch processing, we often come into contact with three kinds of paste, namely, solder paste, solder paste and solder paste. Three kinds of paste from the name of the sound are similar, but from a professional point of view, it will be very different, the next Shenzhen SMT patch processing manufacturer -kingford to introduce the SMT patch processing solder paste, solder paste, welding paste difference and contact.
The difference and connection of solder paste, solder paste and solder paste in SMT patch processing
In fact, in a way, solder paste, solder paste and solder paste are the same thing, that is, solder paste. They are just different in name. But there are many people will take solder paste and solder paste as a product, in fact, solder paste is solder paste. Its main component is a paste of metal alloy powder.
The welding paste is different, mainly plays a role of welding aid, its main components are rosin, active agent and solvent. Solder paste in the process of production will be added to a certain proportion of solder paste.
The role of solder paste: alloy powder; Complete mechanical and electrical connections between electronic components and circuit boards.
The role of welding paste:
1. The carrier of tin powder particles provides suitable rheology and wet strength, which is conducive to heat transfer to the welding area, reduce the surface tension of solder, and prevent reoxidation of solder and welding surface during welding.
2. Remove the oxide layer of the welding surface and tin powder particles, and form a protective layer and a safe residue layer on the surface of the welding point.
3, welding paste ratio, can be any ratio of various kinds of solder powder (tin, silver, copper, bismuth, lead), can also be high, medium and low temperature (100-260) ℃. After matching into solder paste, it has the advantages of good weldability, continuous printing and less residue.
To sum up, solder paste, solder paste, and solder paste are actually two kinds of products - solder paste and solder paste. It is also very simple to distinguish the three, from the appearance of the color can distinguish solder paste and solder paste, solder paste is yellow, solder paste will be gray or black. This is because the solder paste added tin powder composition, and the solder paste is just a simple paste to play a certain role in welding.
The above is the introduction of the differences and connections between solder paste, solder paste and solder paste in SMT patch processing. Next, we will introduce our SMT processing capabilities and advantages.
2.PCBA processing tin beads can receive standards
PCBA processing of the tin bead size on the PCBA board has requirements, this requirement is determined by customers, according to different products and customer requirements, acceptable requirements for tin beads will be different, generally on the basis of the national standard, combined with customer requirements to determine the standard
PCBA processing tin beads can receive standard
Tin beads are explained in some industry standards. The categories range from no tin beads allowed in MIL-STD-2000 to less than five per square inch in IPC-A-610C.
In IPC-A-610C, tin beads with a diameter within the minimum insulation gap of 0.13 nm are considered to be qualified; Tin beads greater than or equal to 0.13 mm in diameter are not qualified, and manufacturers must take corrective measures to avoid this phenomenon. The latest version of IPCA-610D standard for lead-free welding does not clearly specify the tin bead phenomenon. The rule about fewer than five tin beads per square inch has been removed. However, the standards for automotive and military products do not allow any tin beads, so the PCB board must be cleaned after welding or the tin beads must be removed by hand. This is the acceptable standard for PCBA processing tin beads.
SMT patch processing capability
1. Maximum board card: 310mm*410mm(SMT);
2. Maximum plate thickness: 3mm;
3. Minimum plate thickness: 0.5mm;
4. Minimum Chip parts: 0201 package or parts above 0.6mm*0.3mm;
5. Maximum weight of mounted parts: 150g;
6. Maximum parts height: 25mm;
7. Maximum parts size: 150mm*150mm;
8. Minimum spacing of pin parts: 0.3mm;
9. Minimum ball parts (BGA) spacing: 0.3mm;
10. Minimum ball parts (BGA) ball diameter: 0.3mm;
11. Maximum parts mounting accuracy (100QFP) : 25um@IPC;
12. Patch capacity: 3-4 million points/day.
SMT patch processing advantage
1. Highly professional: The company focuses on processing samples and small and medium-sized batches, and promises to deliver the materials within 3-5 working days after confirmation.
2. Professional equipment: The company's equipment is tailored for sample and small and medium-sized batch production of advanced equipment, can stick 0201, BGA spacing 0.3MM, QFN, CSP, CON and other components.
3. Professional technology: 100% of technical backbone workers have more than 5 years of work experience, 85% of front-line operators have more than 3 years of work experience.
4. The company implements the 5S and 6σ concepts in daily operation, so as to ensure that the shipment is checked at least 7 times. If the quantity reaches 100PCS, our company promises to pass AOI optical inspection.
5. The company promises that the straight through rate of welding is more than 99%. If customers find welding defects, the company promises to repair them free of charge.