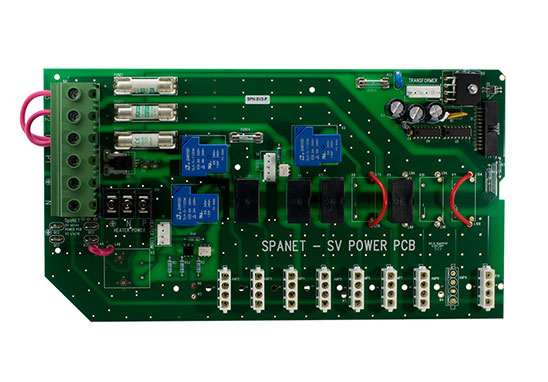
The deformation causes of PCB board processing are very complex and can be divided into thermal stress and mechanical stress. The thermal stress is mainly produced in the process of pressing, and the mechanical stress is mainly produced in the process of stacking, handling and baking. The following is a brief discussion in process order.
Analysis of the deformation cause of PCB board in the process of processing
1. Incoming materials of copper clad plate:
Copper clad plates are double panels, symmetrical structure, no graphics, copper foil and glass cloth CTE is almost the same, so in the process of pressing almost no deformation caused by different Ctes.
However, the large size of the copper clad plate press and the temperature difference in different areas of the hot plate will lead to slight differences in the curing speed and degree of the resin in different areas during the pressing process. Meanwhile, the dynamic viscosity under different heating rates is also very different, so the local stress caused by the difference in the curing process will also be generated.
Generally, the stress will maintain balance after pressing, but will gradually release and produce deformation in the future processing.
2. Pressing:
The pressing process of PCB is the main process of generating thermal stress. Similar to the pressing process of copper clad plate, it will also produce local stress caused by the difference of curing process. The thermal stress of PCB board will be more and more difficult to eliminate than that of copper clad plate due to the thicker thickness, diversified pattern distribution, more semi-cured sheets and other reasons.
The stress in the PCB board is released in the process of drilling, shaping or barbecuing, resulting in the deformation of the board.
3. Welding resistance, character and other baking process:
Since the solder resistance inks cannot be stacked on each other when they are solidified, PCB boards will be placed vertically on the shelf for drying board curing. The solder resistance temperature is about 150℃, which is just above the Tg point of medium and low Tg materials. The resin above the Tg point is in high elastic state, and the board is easy to be deformed under the action of dead weight or strong wind of oven.
4. Hot air solder leveling:
The temperature of the tin furnace is 225℃~265℃, and the time is 3S-6S. The temperature of hot air ranges from 280 ° C to 300 ° C.
Solder plate from room temperature into the tin furnace, out of the oven within two minutes and room temperature post-treatment washing. The whole hot-air solder leveling process is sudden heating and sudden cooling process.
Due to the different materials and uneven structure of the circuit board, thermal stress will inevitably occur in the process of cooling and heating, resulting in microscopic strain and overall deformation and warping.
Step 5 Store:
The storage of PCB board in the semi-finished product stage is generally vertically inserted in the shelf, the shelf tightness adjustment is not appropriate, or the stacking of the board in the storage process will cause mechanical deformation of the board. Especially for the thin plate less than 2.0mm, the impact is more serious.
In addition to the above factors, there are many factors affecting PCB board deformation.
2.PCBA proofing welding requirements
Welding is a very important process in PCBA proofing. So, what are the conditions for PCBA proofing and welding? Next, Shenzhen PCBA processing manufacturer kingford will introduce you.
PCBA proofing welding to meet the conditions
1. Make the welds have good weldability
The so-called weldability, refers to the alloy at the appropriate temperature, can form a good combination between the metal material to be welded and the solder performance. Not all metals are good solderability. In order to improve the solderability, tin plating, silver plating and other measures can be taken to prevent the surface oxidation of materials.
2. Keep the surface of the welds clean
In order to achieve a good combination of solder and solder, the welding surface must be kept clean. Even weldables with good weldability may produce oxide film and oil stains on the surface of weldables that can cause harmful penetration due to storage or contamination. The dirty film must be removed before welding, otherwise the welding quality cannot be guaranteed.
3. Use the right flux
The function of the flux is to remove the oxide film from the surface of the weldment. Different welding process should choose different flux. When welding precision electronic products such as printed circuit boards, rosin flux is usually used to ensure reliable and stable welding.
4. The welding parts should be heated to an appropriate temperature
Welding temperature is too low, is not conducive to the penetration of solder atoms, can not form alloy, so it is easy to form welding failure; If the welding temperature is too high, the solder will be in a non-eutectic state, accelerate the decomposition and volatilization of flux, reduce the quality of solder, and in serious cases will lead to the loss of the solder pad on the printed circuit board.
5. Appropriate welding time
Welding time refers to the time required for physical and chemical changes to occur during the entire welding process. When determining the welding temperature, the appropriate welding time should be determined according to the shape, nature and characteristics of the welds. The welding time is too long, the parts or welding parts are easy to damage; If it is too short, it will not meet the welding requirements. Generally, the maximum welding time of each solder joint is 5s.
Shenzhen kingford is a professional manufacturer of printed circuit board manufacturing circuit board, for many years focused on single, double-sided, multi-layer circuit board production. We can provide PCB proofing and mass production services such as FR4 hard board, FPC soft board, HDI board and metal substrate.