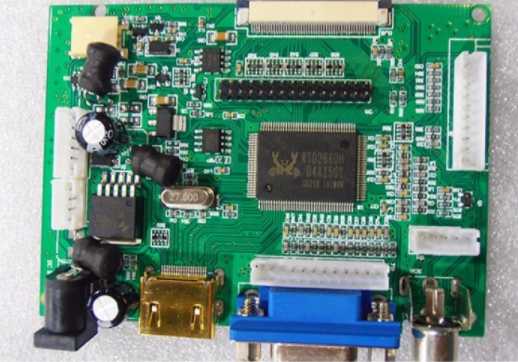
Aluminum substrate is generally led aluminum substrate, because it is commonly used in LED lighting products. There are positive and negative sides, the white side is welded LED pin, the other side shows aluminum color, generally will be coated with thermal coagulation in the thermal part of contact. Next, Shenzhen aluminum substrate manufacturer -kingford to introduce the four methods of aluminum substrate proofing.
Four proofing methods for aluminum substrate
1, photographic material proofing method
Generally, the sensitive material is coated on the film base, and then the corresponding separation screen film closely attached, exposed, made of monochromatic yellow, magenta, green, black film, the superimposed together, combined into a color image; The color layer of each monochrome can also be transferred to the proofing substrate to form a color proof.
2, mechanical proofing method
Generally, under the circumstances of basically the same printing conditions (such as paper, ink, printing method, etc.), the printing plate made with the original version is installed on the proofing machine, printed, and then proofread against the original manuscript or layout design, until the tone, color, text, layout size is correct, and finally signed by the customer, you can be printed.
Preproofing method preproofing, do not need printing plate, paper, ink and prototyping, and the use of special sensitive materials, the application of optical, photochemical principles, color samples or display with the display screen, find the problems in image information processing, timely correction, improve the efficiency of mechanical proofing.
3, electronic proofing method
1, inkjet printer, print head mounted on a very thin nozzle, using the nozzle to spray ink onto the paper. The printer comes in a variety of models including four print heads, three print heads and one print.
2, thermal sublimation printer, printing head installed with a number of thermal sensitive elements, the transparent dye on the color ribbon, melted into the paper, each color overlays each other, superposition a color image like a photograph.
4, computer aided proofing method
This method has soft proofing and hard proofing.
1, soft proofing, using computer-aided color proofing system, see color images on the display screen, can not get proofs.
2, hard proofing, the use of color full-page printing system output data, obtain proof in the hard proofing system.
Hard proofing system, generally by the display terminal, keyboard, floppy disk drive device, laser recording system and online photo development machine.
2.PCB design layout constraint principle
A good circuit board, in addition to the realization of the circuit principle function, but also to consider EMI, EMC, ESD (electrostatic discharge), signal integrity and other electrical characteristics, but also to consider the mechanical structure, large power chip heat dissipation problem, on this basis to consider the beauty of the circuit board, just like art sculpture, to consider every detail. Next, Shenzhen PCB design company -kingford introduces the PCB design layout constraint principle.
There are often several considerations in PCB component layout.
1. Does the PCB board shape match the whole machine?
2. Is the spacing between components reasonable? Is there a level or level of conflict?
3. Does PCB need to be assembled? Are craft edges reserved? Are installation holes reserved? How to arrange the positioning holes?
4. How do I place the power module and dissipate heat?
5. Are the components that need to be replaced frequently placed in a convenient location? Is the adjustable element easy to adjust?
6. Is the distance between the heat sensitive element and the heating element considered?
7. What is the EMC performance of the whole board? How to layout can effectively enhance anti-interference capability?
For the problem of spacing between components and components, based on different package distance requirements and Altium Designer's own characteristics, if constrained by the rule setting, the setting is too complex, difficult to achieve. Lines are usually drawn on the mechanical layer to indicate the peripheral dimensions of the components, so that when other components approach, the spacing is roughly known. This is very practical for beginners, but also enable beginners to develop good PCB design habits.
Common PCB layout constraints
Through the above consideration and analysis, the common PCB design layout constraint principles can be classified as follows.
Element arrangement principle
1. Under normal conditions, all components should be arranged on the same surface of the PCB. Only when the top component is too dense, can some components with limited height and small heat (such as patch resistance, patch capacitance, patch IC, etc.) be placed on the bottom.
2. On the premise of ensuring electrical performance, components should be placed on the grid and arranged parallel or vertical to each other in order to be neat and beautiful. In general, components are not allowed to overlap, component arrangement should be compact, input components and output components as far away as possible, do not cross.
3. There may be a high voltage between some components or wires, should increase their distance, so as to avoid accidental short circuit caused by discharge, breakdown, layout as much as possible to pay attention to the layout space of these signals.
4. The components with high voltage should be arranged as far as possible in the place where the hand is not easy to touch when debugging.
5. Components located at the edge of the plate should be as close as possible to two plate thickness from the edge of the plate.
6 components in the whole board surface should be evenly distributed, do not this area dense, another area loose, improve the reliability of the product
Follow the signal direction layout principle
1. After placing the fixed components, the position of each functional circuit unit is arranged one by one according to the direction of the signal, and the core component of each functional circuit is taken as the center to carry out local layout around it.
2. The layout of the components should facilitate signal flow, so that the signal as much as possible to maintain a consistent direction. In most cases, the flow direction of the signal is arranged from left to right or top to bottom, and the components directly connected to the input and output terminals should be placed near the input and output connectors or connectors.
Protection against electromagnetic interference
1. For the components with strong radiation electromagnetic field and those sensitive to electromagnetic induction, the distance between them should be increased, or a shielding cover should be considered.
2. Try to avoid high and low voltage components mixed with each other and strong and weak signal components interleaved together.
3. For the components that will produce magnetic fields, such as transformers, loudspeakers, inductors, etc., the layout should pay attention to reduce the cutting of magnetic force lines on printed wires, and the magnetic field direction of adjacent components should be perpendicular to each other to reduce the coupling between each other. Figure 9-2 shows the inductor layout 90° perpendicular to the inductor.
4. Screen interference sources or easily interfered modules. The shielding cover should be properly grounded.
Suppression of thermal interference
1. For the heating element, it should be preferentially arranged in the position conducive to heat dissipation. If necessary, the radiator or small fan can be set separately to reduce the temperature and reduce the influence on the adjacent element.
2. Some integrated blocks, high-power tubes and resistors with high power consumption should be arranged in places that are easy to dissipate heat and separated from other components.
3. The thermal sensitive element should be close to the element under test and away from the high temperature area, so as not to be affected by other thermal equivalent components, causing misoperation.
4. When double-sided placing components, the bottom layer is generally not placed heating components.
Principle of adjustable component layout
For potentiometer, variable capacitor, adjustable inductor coil, micro switch and other adjustable components layout, should consider the structural requirements of the whole machine: if the machine adjustment, its position should be adapted to the position of the adjustment knob on the chassis panel; If it is adjusted in the machine, it should be placed on the PCB where it is convenient to adjust.
kingford is a professional manufacturer of double-sided aluminum substrate proofing and small and medium-sized batch production. The company can process three types of aluminum substrate, including single-sided aluminum substrate, double-sided aluminum substrate and double-sided aluminum substrate with insulation holes. The process includes gold sinking, OSP and tin spraying.