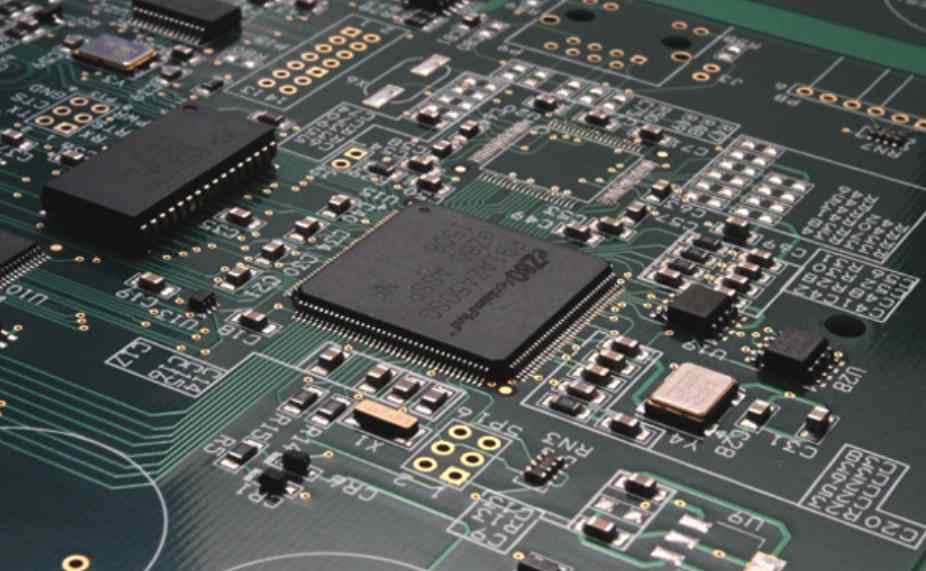
In the design, processing and testing of PCB circuit boards, there are many places that need to use electric soldering iron for manual welding. Today, the senior first-line manual welding master of Nuo Electronics will tell you the skills of manual welding.
The difference between manual welding of electric iron and machine welding, such as wave soldering and flow welding, is that there are more human factors in manual welding of soldering iron. Unlike machine welding, once the process parameters are adjusted, the production is very stable, manual welding also has the problem of welding temperature and welding time, we first introduce the electric iron manual lead-free welding process, welding process window, and the principle of the heat conduction of the electric iron to the pad, to deeply understand the meaning of welding temperature welding time, through the theoretical guidance, coupled with diligent practice, To become a qualified skilled worker.
1. Prepare for welding
(1) When we just use a new electric iron, we should first of all have a preliminary understanding of the characteristics of the iron, such as working voltage, electric power, reheating rate, the size and variety of the iron head
(2) It is necessary to know whether the variety of solder is lead-free solder, and the thickness of their melting point tin wire
(3) Understanding of component types, such as plug-in or patch components, and heat-sensitive keys
(4) the printed board material, welding plate coating type, such as whether the tin base, gold plating, osp and parameters have an understanding, usually welding osp, the temperature of the gold plate should be higher than the tin substrate, the heat absorption of the multilayer plate is greater than the double plate and single plate;
(5) Familiar with the size of welding spot and the speed of heat dissipation of welding surface;
(6) The anti-static performance of the electric iron, whether the workbench has an anti-static grounding port, usually when the electric iron is connected to the power supply, it should also be connected to the anti-static channel.
In short, familiar with the performance of the tool, as well as the basic parameters of the welding object, is very beneficial to adjust the temperature and type of soldering iron head, of course, when conditions, can be further confirmed by PCB board temperature test and welding test parameters.
2. Operation method of electric soldering iron
The operator who uses electric iron for manual welding for the first time should be strict with himself, develop good operating habits, do the right welding posture, and master the basic operating steps of welding and the basic essentials of manual welding.
(1) Correct welding posture
In the manual welding of electronic products, generally take the seated welding, the height of the workbench and the seat should be appropriate, the relative position between the head of the operator and the electric iron should be maintained between 30 ~ 50cm, one hand holding the iron and one hand holding the tin wire, and visual welding points.
(2) The method by which the welding operator holds the electric soldering iron
Usually according to the size of the electric iron, there are three different operation methods: reverse grip, is grip, pen grip, which is suitable for high-power electric iron more than 75 watts of welding large solder joint operation; The positive grip method is suitable for the operation of the medium power electric iron and the electric iron with elbow, and the pen grip method is suitable for the welding of the components on the printed board with the small power electric iron, which is mainly used for the manual welding of electronic products.
(3) direction of electric soldering iron contact solder spot
When welding electronic products with a pen grip, the electric iron should contact the solder joint in a 45 degree direction, which is conducive to the operation and observation of the forming of the solder joint.
(4) The handling of tin wire
There are usually two ways to take the solder wire, one is suitable for continuous welding, the other is suitable for intermittent (welding is usually relatively large solder joint), in the actual welding operation, when taking the solder wire to wear good gloves, especially the lead tin wire, to prevent the skin from often contacting with lead.
(5) Basic operation of manual welding
The manual welding operation process can be subdivided into five steps, which are required to be completed within 3 ~ 5 seconds. They are:
a. Prepare to bring the soldering iron head and tin wire close to the pad
b. Heating, first of all, the soldering iron head on the pad, the pad is the first to preheat
c. Lean the tin wire on the contact point between the soldering iron head and the pad to melt it quickly
d. After the solder joint is formed, first remove the tin wire
e. Remove the electric soldering iron and cool the solder joint for forming
In the case of small solder joints on the circuit board, the three-step method can also be used to complete the welding, and step b.c and step d.e in the five-step method can be integrated into one.